- Best Practices for Equipment O&M
-
O&M Best Practice Issue Discussions
- Advanced Maintenance Approach: Reliability Centered Maintenance
- Applying Key Performance Indicators
- Comprehensive O&M Program
- Contract Challenges and Improvements
- Cybersecurity for O&M Systems
- Existing Building Commissioning Procurement
- Healthy Building O&M
- Integrating and Analyzing Building Information to Support O&M
- Maintenance Approaches
- OMETA: An Integrated Approach to Operations, Maintenance, Engineering, Training, and Administration
- Prioritizing O&M Actions
- Re-tuning Buildings
- Tools
- Glossary
Solar Photovoltaic
Table of Contents
- Introduction
- Description of Technology
- Key Components
- Safety Issues
- Maintenance of Technology
- Maintenance Checklist
- Performance Monitoring
- O&M Cost
- Additional Support
- Sources of Information
Introduction
Solar photovoltaic (PV) systems are among the most commonly used renewable energy technologies on federal sites. Effective operations and maintenance (O&M) of these systems is necessary to maximize system production and help achieve energy reduction and decarbonization goals.
The purpose of this Best Practice is to provide an overview of the system components, maintenance requirements, and reporting requirements to keep solar PV systems operating safely and efficiently. Regular O&M of solar PV arrays will ensure that systems continue to operate effectively, and tracking system performance will help identify potential issues and maximize savings. Support organizations should budget and plan for regular maintenance to ensure continuous operation.
Description of Technology
Solar PV cells convert light directly into electricity. As light enters a PV cell, photons impart energy to electrons, producing an electrical current. Before being introduced into the utility grid and/or site distribution system, this electricity typically needs to be conditioned. Solar cells produce direct current (DC) power, and this electricity must be converted to alternating current (AC) by an inverter for most applications, as well as for export to the grid. A transformer may also be required if the electricity is exported to the utility grid.
PV panels can be mounted on fixed racks or on a tracking system that follows the sun throughout the day and sometimes seasons. PV systems are typically installed in one of three locations:
- Ground-mounted arrays are typically the easiest to access for O&M.
- Parking canopy/carport-mounted arrays are becoming increasingly popular, in part because they are easy to site, and they don’t occupy areas that may be used for other purposes.
- Roof-mounted arrays are typically smaller systems because of space limitations and, in some cases, structural considerations. Maintenance costs for rooftop systems can vary based on the accessibility of the system.
Key Components
The key elements of solar PV systems include modules, mounting systems, inverters, switchgear, wiring, monitoring equipment, and sometimes a transformer. These are briefly summarized below.
- Solar PV modules – PV modules consist of rigid poly- or monocrystalline or flexible thin film panels. The module collects and converts solar energy to DC electrical energy.
- Mounting – Mounting equipment secures the PV modules either in a fixed position or to a tracking system. Rooftop mounting systems are typically fixed and use either anchors physically attached to the sub-roof structure or several on-roof ballasts integrated into the mounting structure. Ground-mounted systems use either concrete anchors beneath the Earth’s surface or aboveground ballasts and can be fixed or use single- or dual-axis tracking. Carport structures can also be a mounting platform for PV modules. They are typically in a fixed position.
- Inverter – An inverter converts DC energy from the solar PV modules into AC energy that can be used in local buildings or exported to the grid. Inverters often have digital displays that provide information on system status, such as live output power and cumulative energy production. A PV system may use one large central inverter, several central inverters, or many micro inverters. Large central inverters use internal transformers for DC-to-AC energy inversion, while smaller central and micro inverters typically use transformerless power electronics. Inverters may be located outdoors next to the PV array or inside the electrical room.
- Electric switchgear – Switchgear is safety equipment for PV systems and can be automated or manual. It includes disconnects, breakers, building isolation switching, and lightning arresters.
- Wiring – Solar PV system wiring consists of conductors that connect PV panels, inverters, switchgear, a tracking system (if applicable), and the distribution system, as well as combiner boxes that combine multiple small strings of conductors into single large ones. A separate grounding system connects all metallic components to an existing grounding system or separate ground rods driven into the earth.
- Monitoring – Monitoring equipment can range from a simple utility-grade meter that displays system output for manual reading to sophisticated software that allows remote data reading and recording. Meters are found on every PV system and are typically connected in-line with conductors between the inverter and grid interconnection point. Monitoring software, if used, is installed on an on-site or remote computer, and data is transmitted from the inverter to the computer either wirelessly or via conductors. Monitoring software should be updated when the manufacturer releases the updates.
- Transformer – Some solar PV arrays require transformers. Small arrays (less than 50 kW) can be integrated directly into an electrical service panel. Larger arrays are connected directly to the transmission system and require a transformer to step up the voltage to grid voltage (i.e., from 480 V to 15 kV).
Figures 1 and 2 show some of these components. Figure 1 shows two small central inverters with related components located in an electrical room. Figure 2 is a simplified diagram of a grid-connected solar PV system that does not require a transformer.
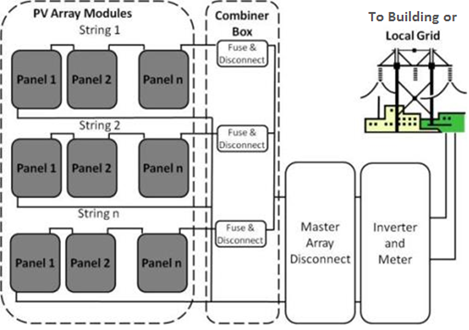
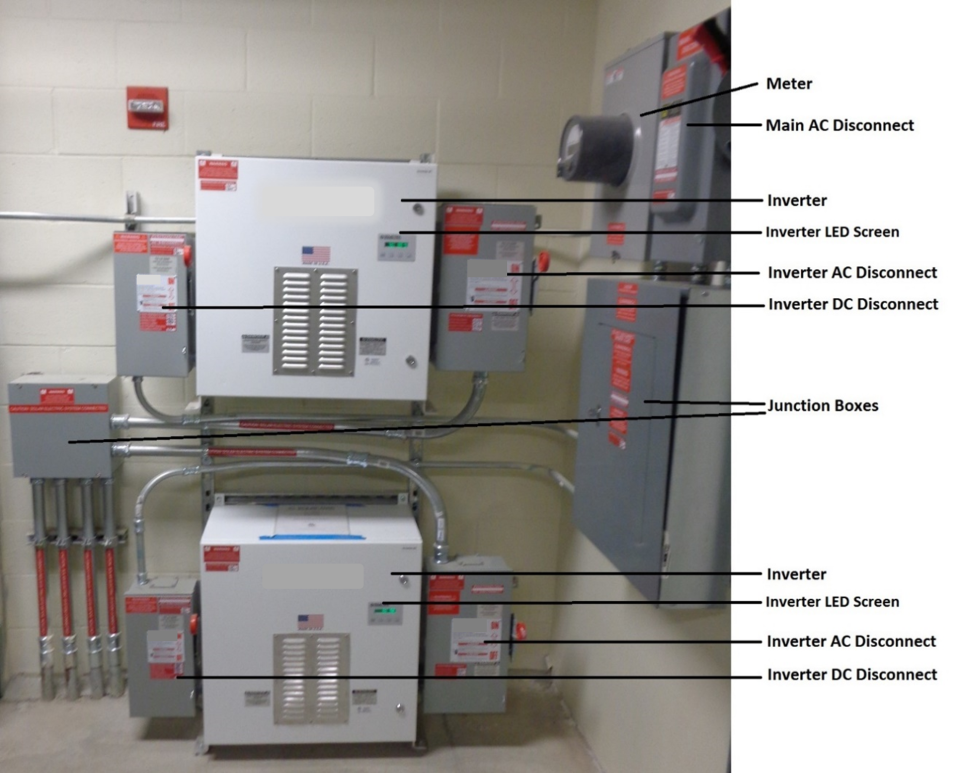
Safety Issues
As with any electrical work, servicing a solar PV system can be dangerous and potentially lethal without the correct knowledge and training because of high voltage. System shutdown instructions should be posted on the inverter according to National Electric Code (NEC), state, and local requirements. NEC requires that main AC and DC disconnects are located within sight of the inverter. To turn off the system in case of fire or another emergency, shut off the main AC disconnect and then the main DC disconnect. Assume that solar PV modules are always producing electricity during daylight hours regardless of weather conditions or disconnect status. Only trained and authorized maintenance providers with approved safety gear should connect or disconnect any system wiring.
Maintenance of Technology
Keeping solar PV systems properly maintained through preventive maintenance will minimize overall O&M requirements, improve system performance, and protect the asset. Most manufacturer warranties cover the first 10 years for PV panels, but some premium panels have 25-year warranties. Inverter warranties are typically 5 years, but extensions to 10 or 15 years are available and recommended. Installation/workmanship warranties from the installation contractor vary from 2 to 10 years.
A majority of solar PV system O&M tasks are visual inspections that don’t require specialty licensed O&M personnel. Personnel need only have knowledge of the proper appearance of electrical wiring and secure mechanical attachments.
PV panel soiling (where dust and grime build up on PV panels over time) is the biggest O&M issue for solar PV systems. It is often difficult to visually detect soiled PV panels, so it is recommended that cleaning schedules and methods prescribed by the site PV contractor that installed the system be followed. Frequency of washing PV panels depends on area-specific environmental factors such as rainfall, array tilt, and amount of air pollutants. Arrays with low tilt in arid climates may need to be washed every month in the summer, while arrays with latitude tilt in rainy climates may never need to be washed.
The washing method depends on the degree of soiling and the size of the system. Arrays in urban areas that have little airborne debris often only need to be sprayed with a water-fed “Tucker Pole” or equivalent washer. Arrays in rural areas or near dirt roads may need to first be sprayed with a water-fed pole, then scrubbed with a brush and soapy water, and finally rinsed with clean water. Very large arrays (over 500 kW) may use an automated cleaning system. The frequency of washing and extent of soiling will determine whether automated or manual cleaning is more cost-effective. Ideally, panels will always be free from obstruction; however, the cost of frequent washing can reduce monetary savings of the system.
It is important to keep a good log of service performed, inverter alarms, conditions inhibiting performance, downtime, and other relevant issues noted and resolved. This will help identify recurring warranty issues or systemic problems, as well as ensure warranties remain valid. Work orders related to the PV system should be recorded.
Maintenance Checklist
A standard maintenance plan is as follows. A site staff member or contractor can be designated to perform all of the following tasks, but repairs should be performed by the authorized maintenance provider. This checklist does not supersede maintenance recommendations from the equipment manufacturers, nor is it a replacement for contracted O&M or warranty services.
Component |
Action |
Frequency |
General |
⃣ Inspect panels for water infiltration |
Monthly |
⃣ Check for signs of electrical arcing |
||
⃣ Inspect system for loose wiring |
||
⃣ Inspect modules for dirt or droppings |
||
⃣ Check for insecure mounts |
||
⃣ Inspect system for signs of corrosion |
||
⃣ Ensure integrity of roof penetrations |
||
⃣ Check for animal infestations |
||
⃣ Remove overgrowth or obstructions |
||
⃣ Check for erosion of ground if applicable |
||
⃣ Ensure safety placards are in place and legible |
||
⃣ Inspect monitoring equipment for malfunctions |
||
Inverters |
⃣ Validate energy production |
Follow manufacturer recommendation |
⃣ Clean air intake filters |
||
⃣ Check fuses for integrity |
||
⃣ Check wire connections for integrity |
||
Solar array |
⃣ As necessary, wash panels with a water-fed pole, scrubbing with brush, mild detergent, or automated washing system, per the installer’s instructions |
Follow installer’s recommendation |
Tracking system (where installed) |
⃣ Follow manufacturer’s recommendation for checking the tracking system |
Follow manufacturer’s recommendation |
Performance Monitoring (Measurement and Verification)
Monitoring PV system performance is important to ensure proper operation and cost savings as well as for reporting purposes (when required). Solar PV systems ideally include monitoring hardware and/or software that provide system performance information (e.g., amount of electricity generated). Monitoring software provides the production data directly to a computer. If monitoring software is not provided, monthly energy production can be calculated by viewing the running tally of energy production data on the inverter LED screen or system production meter. On approximately the same day each month, the energy output of the system from either or both screens should be manually recorded. The monthly production is the current month’s reading minus the previous month’s reading. Other monitoring intervals may be used with the described procedure modified accordingly.
At least monthly, system production levels should be checked by comparing these levels to estimated monthly production values as well as historical values. The site PV contractor should provide the system’s estimated monthly production. If not, system characteristics may be modeled with PVWatts, an online production estimation tool from the National Renewable Energy Laboratory (NREL 2016). Solar insolation (the amount of solar radiation received by a surface over a given time) can vary +/- 10% from average—begin troubleshooting when production falls outside these expected ranges. Low production can indicate malfunctioning components or soiled panels.
O&M Cost
The costs to operate and maintain solar PV systems are known to vary widely based on technology used, size of the PV installation, and the O&M service contract requirements. A multi-organization working group formed in 2016 to address PV O&M recommended budgeting 0.5% and 1% of the initial system cost for large (utility-scale and larger) and small (residential and small commercial) PV systems, respectively (NREL 2018).
Additional Support
Best Practices for Operation and Maintenance of Photovoltaic and Energy Storage Systems; 3rd Edition provides comprehensive recommendations to reduce costs and improve system effectiveness (NREL 2018). https://www.nrel.gov/docs/fy19osti/73822.pdf
O&M Best Practices for Small-Scale PV Systems is a 1.5-hour Federal Energy Management Program First Thursday Seminar about O&M best practices for PV systems of 100 kW or less. Topics include planning the scope of work and maintenance procedures to keep the system operating at optimal capacity. The seminar is available at: https://www.wbdg.org/continuing-education/femp-courses/fempfts27.
Operations and Maintenance for Optimal Photovoltaic System Performance is a 5-hour Federal Energy Management Program on-demand training course. This eTraining outlines the necessary steps for directing ongoing or new operation of PV systems for the life of the project across a variety of system types, sizes, and environments. It is designed for personnel looking to plan and direct an O&M program for a variety of PV systems. https://www.wbdg.org/continuing-education/femp-courses/femp56
PV System Operations and Maintenance Fundamentals contains detailed, step-by-step instructions on solar PV system O&M and troubleshooting (Haney and Burstein 2013). http://www.solarabcs.org/about/publications/reports/operations-maintenance/pdfs/SolarABCs-35-2013.pdf
Sources of Information
Haney J and A Burstein. 2013. PV System Operations and Maintenance Fundamentals. Solar America Board for Codes and Standards. http://www.solarabcs.org/about/publications/reports/operations-maintenance/pdfs/SolarABCs-35-2013.pdf.
NREL. 2016. PVWattsÒ Calculator. National Renewable Energy Laboratory, Golden, CO. http://pvwatts.nrel.gov/pvwatts.php.
National Renewable Energy Laboratory, Sandia National Laboratories, SunSpec Alliance, and the SunShot National Laboratory Multiyear Partnership (SuNLaMP) PV O&M Best Practices Working Group. 2018. Best Practices for Operation and Maintenance of Photovoltaic and Energy Storage Systems; 3rd Edition. Golden, CO: National Renewable Energy Laboratory. NREL/TP-7A40-73822. https://www.nrel.gov/docs/fy19osti/73822.pdf