- Best Practices for Equipment O&M
-
O&M Best Practice Issue Discussions
- Advanced Maintenance Approach: Reliability Centered Maintenance
- Applying Key Performance Indicators
- Comprehensive O&M Program
- Contract Challenges and Improvements
- Cybersecurity for O&M Systems
- Existing Building Commissioning Procurement
- Healthy Building O&M
- Integrating and Analyzing Building Information to Support O&M
- Maintenance Approaches
- OMETA: An Integrated Approach to Operations, Maintenance, Engineering, Training, and Administration
- Prioritizing O&M Actions
- Re-tuning Buildings
- Tools
- Glossary
Variable Speed Drives
Best Practices for Variable Speed Drives Operation and Maintenance
Table of Contents
- Introduction
- Description of Technology
- Key Components
- Safety Issues
- Maintenance of Technology
- Maintenance Checklist
- Performance Monitoring
- O&M Cost
- Additional Support
- Sources of Information
Introduction
According to the U.S. Department of Energy, motor-driven equipment accounts for well over half of the electricity used by U.S. industry (DOE 2012). Therefore, many manufacturers, businesses, and industries have turned to energy savings equipment and strategies to reduce this staggering total. One of the most accepted and cost-effective energy reduction strategies is the installation of variable speed drives (VSDs).
The term VSD is a catch-all term related to devices that affect the output speed of a drive or motor system. Under this broad heading are devices that can control motor speed via electronics (alternating current [AC] and direct current [DC] electronic drives), clutching mechanisms (eddy current clutches), and mechanical devices (fluid couplings, magnetic couplings, and a variety of pulley, belt, chain, and gear-box devices). By far, the most common VSD is the variable frequency drive (VFD) because of its efficiency and ability to affect the most popular type of electric motor—the AC induction motor.
Since the mid-1980s, VFDs have been used to control AC motors that drive fans, pumps, blowers, mixers, conveyors, and a host of other variable loads. With advances in microelectronics over the past 15 years, VFDs have become more efficient and reliable, allowing their applications to expand significantly. Appropriate operations and maintenance (O&M) of VFD systems is necessary to optimize system performance and achieve reliable and high efficiency.
The purpose of this equipment O&M Best Practice is to provide an overview of system components and maintenance activities necessary to keep VFD systems operating safely and efficiently. Regular O&M of VFD systems will assure overall system reliability, efficiency, and function throughout their life cycles, and support organizations should budget and plan for regular maintenance of VFD systems to assure continuous safe and efficient operation.
Description of Technology
VFDs reduce electrical energy use by adjusting motor speed to match the system-required load. VFDs eliminate the need for other types of energy-wasting devices, such as outlet dampers or pressure control valves, that serve a similar control function but do so by dissipating energy.
VFDs control the rotational speed of AC induction motors (both single and three-phase) by adjusting the frequency of the electrical power supplied to the motor. While there are a variety of technologies used to accomplish the variable or adjustable speeds of electric motors, the most common relies on the pulse-width modulation (PWM) technology (IntechOpen 2015; DOE 2014).
A PWM-based VFD functions by first converting incoming AC power to DC power using an AC-to-DC rectifier. Once rectified, this power is filtered to achieve the desired wave form, inverted, and then given a controlling voltage and frequency before being sent to the motor. This process allows the output frequency of the drive to control the motor speed. Figure 1 presents a schematic of a typical VFD (ASHRAE 2008).
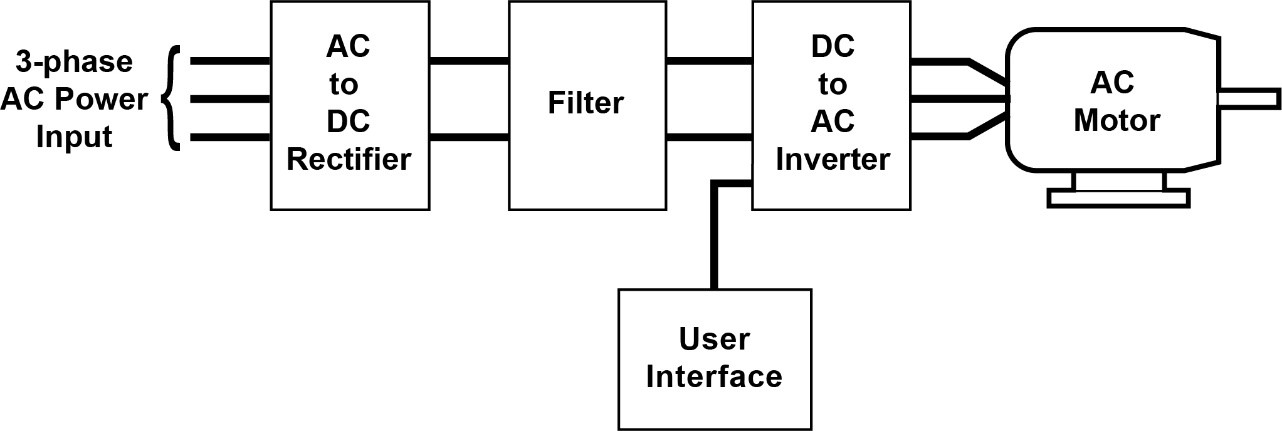
VFDs are used in a variety of commercial and industrial load-varying applications that use AC inverter-duty-rated induction motors such as fans, pumps, compressors, and conveyors.
Depending on the application and installation, VFDs can cause electromagnetic interference (EMI) in the form of harmonics. This interference can result in maintenance issues with other sensitive equipment and the distribution system at large. To minimize this interference and potential ancillary maintenance issues, most manufacturers recommend the following:
- Short conductor lengths of less than 50 feet between the VFD and motor, if possible.
- Noise suppression and harmonic filters to help reduce electrical interference.
- Isolation transformers for the VFD’s power, allowing for a separate grounding circuit.
Key Components
This section focuses on the components of the most commonly used VFD—the PWM VFD—as typically found in commercial and industrial systems. While VFDs can come in a variety of sizes and configurations, Figure 2 highlights a common VFD configuration and form factor.
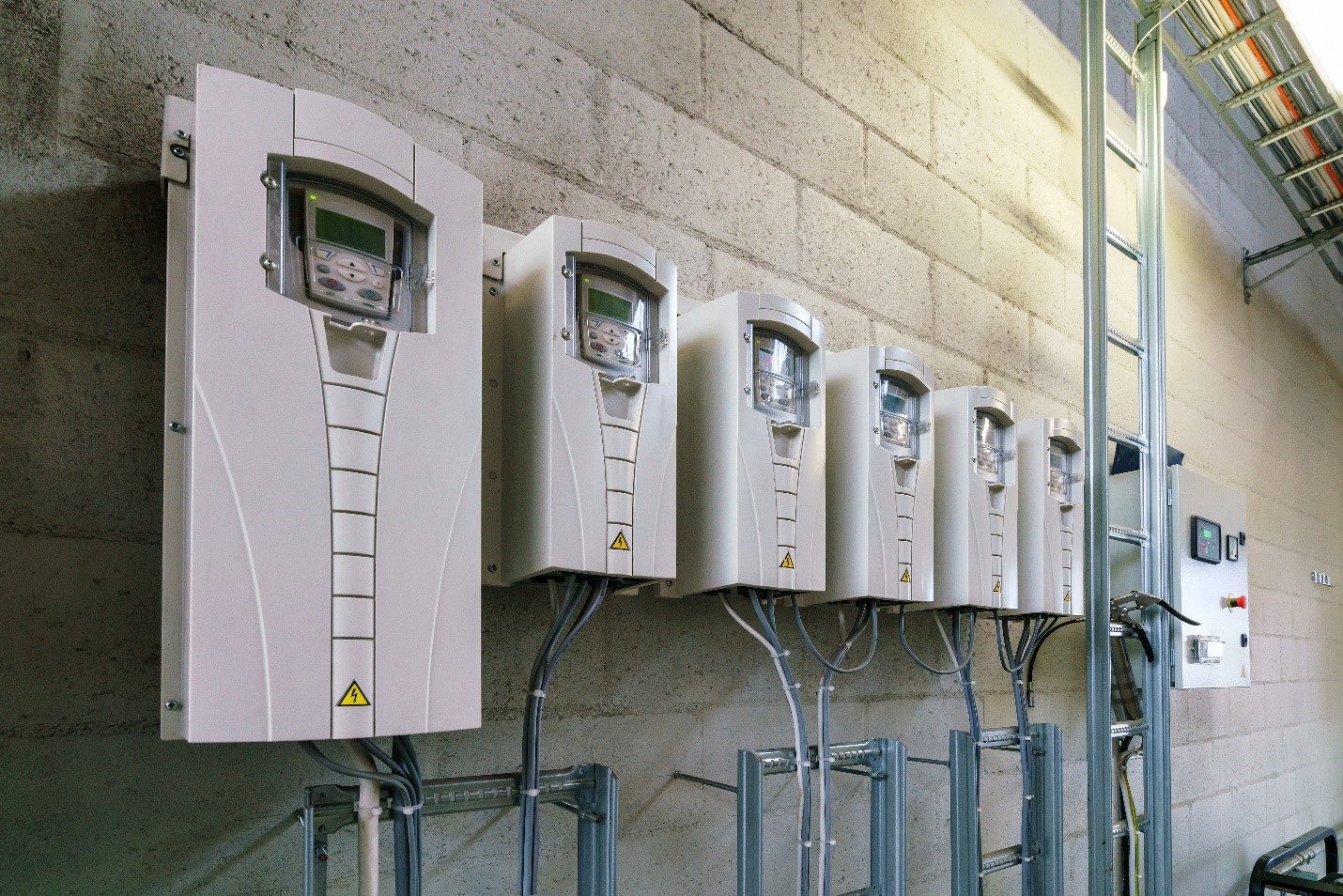
VFD drive. The primary enclosure houses the functional components, electronics, circuitry, and controls that allow the drive to operate. The drive enclosure also contains cooling components such as heat sinks and circulating fans. Usually, the drive will have a display screen allowing for setup, making adjustments, and viewing real-time operational parameters.
Network connection. Most VFDs have the ability to connect to a network for setup, operation, and monitoring. This feature allows connection to a building automation/energy management system or a VFD-specific management software system.
Wiring. A critical element of a functional VFD is properly sized and routed connection wiring to the motor. The conductor sizing and its run length (distance between drive and motor) can have functional and maintenance implications. In some instances, a bypass device is wired as part of the installation. The bypass allows the VFD to be disconnected for service or other issues and is used in critical applications where downtime is costly. Note that when the VFD is in the bypass mode, full voltage power will be supplied to the motor.
Connections. Typical terminal block connections are found on the power (input) and motor (output) sides of the drive with appropriately labeled voltages and phases.
Environment. While not specifically a component of the drive, the ambient environment in which the drive operates is critical to reliable function. All VFDs have critical temperature and humidity ranges required for reliable operation. Also, because the principal components are electronic, exposure to dust or other airborne particulates should be avoided. Consequently, VFDs are often housed in climate-controlled areas or cabinets away from the motors that they regulate.
Safety Issues
As with any electrical device, all aspects should be powered down to a safety state before any maintenance or diagnostics are performed. As needed, and per manufacturer’s and electrical safety recommendations, VFD system functions can be enabled for testing and verification of performance. Standard electrical and mechanical safety practices apply to these systems.
Maintenance of Technology
Keeping VFD systems properly maintained through preventive and predictive maintenance will minimize overall O&M requirements, improve system performance, and protect the asset. Follow the guidelines in the equipment manufacturer’s maintenance manuals for proper care.
VFD systems are designed to be relatively maintenance free. However, because they encompass a variety of sensitive electronics, fan motors, and filters, they do require periodic attention. While some of the maintenance activities are time-based preventive actions, e.g., verifying real-time settings or checking, cleaning, and changing filters or fan motors, some fall into the predictive category whereby trending operating and ambient temperatures (through infrared imaging) can allow for early or predictive fault detection. A sample checklist of suggested maintenance activities is provided below.
Occasionally, VFDs can “trip” offline. This can happen as part of a power outage, an overheating event, or other component fault. It is important to recognize that an event has occurred, but understanding the cause is even more vital. Overheating events can be common with VFDs installed in high-temperature or poorly ventilated spaces. Making sure the VFD enclosure is properly designed for the environment is critical to reliable operation.
Before resetting any offline or tripping event, diagnostics should be performed to identify and correct the root cause.
It is important to keep a written log, preferably in electronic form in a Computerized Maintenance Management System (CMMS), of all services performed. This record should include identifying features of the VFD (e.g., type, make, model, and serial number), functions and diagnostics performed, findings, and corrective actions taken.
Maintenance Checklist
For all VFD maintenance, it is important to follow the manufacturer’s recommendations. Proper maintenance should only be performed by trained and qualified personnel. The sample checklist in Table 1 provides recommended actions and the frequency at which they should be performed by VFD component type. This checklist does not supersede maintenance recommendations from the equipment manufacturer, nor is it a replacement for contracted O&M or warranty services.
Actions and activities recommended in this Best Practice should only be attempted by trained and certified personnel. If such personnel are not available, the actions recommended here should not be initiated.
Boilers systems require knowledgeable and experienced personnel for maintenance, diagnostics, and service. Standard electrical, mechanical, and other safety practices apply to these systems. High temperatures and pressures are present in all boiler systems, and high voltage is present in electric boilers.
Only qualified and experienced personnel should work with an ATS. High voltages are present in ATS systems. All power supplies, breakers, connections and disconnects must be understood and treated appropriately before any service is attempted. All related code and safety procedures must be understood and followed. Any service provider should follow the manufacturer’s recommendations as well as the safety guidelines found in both NFPA – 70E Standard for Electrical Safety in the Workplace (NFPA 2018), and IEEE 1584 Guide for Performing Arc Flash Hazard Calculations (IEEE 2018).
As with any electrical device, all aspects should be powered down to a safety state before any maintenance or diagnostics are performed. As needed, and per manufacturer’s and electrical safety recommendations, VFD system functions can be enabled for testing and verification of performance. Standard electrical and mechanical safety practices apply to these systems.
As with any electromechanical device, all aspects should be powered down to a safety state before any maintenance or diagnostics are performed. As needed, and per manufacturer’s and electrical safety recommendations, VAV system functions can be enabled for testing and verification or performance. Standard electrical and mechanical safety practices apply to these systems.
Standard electrical and mechanical safety practices apply to these systems. Antifreeze solution, which is typically used in the ground loop as a heat transfer fluid, is toxic to humans and animals, so disposal requires compliance with local regulations.
Performance Monitoring
The most common option for VFD performance monitoring is making use of the VFD’s network connection and using a BAS. By enabling a BAS’s trending function and reviewing the data, the VFD system operation can be assessed.
Key points to trend include the following:
- Actual run time of VFD for comparison to the scheduled or anticipated run time.
- Output frequency (hertz) and/or fan speed (typically reported as a percentage).
- VFD amperage draw trend and changes over time.
- Kilo-watt hour usage of the drive and system, as well as trends and changes over time.
- Proxy trends include metrics affected by the VFD system, potentially including:
- Static pressure in supply air ducting that is used as a control point for the system VFD fan.
- Fluid pressure in a hydraulic system that uses pressure as the pump control point.
- Zonal air temperatures.
O&M Cost
Modern solid-state VFD systems are designed to be highly reliable and require little maintenance. There is very little reliable data published on actual VFD maintenance costs, with most manufacturers deferring to standard preventive and predictive actions at the periodicities noted in Table 1.
Additional Support
Over the years, the DOE has funded numerous projects, programs, and documents focused on energy efficiency in electric motors and drives. Much of this information is still very relevant and can be accessed at: https://www.energy.gov/eere/amo/motor-systems. This website includes links to a variety of publications, including U.S. Department of Energy's Motor Challenge Program: A National Strategy for Energy Efficient Industrial Motor-Driven Systems and Continuous Energy Improvement in Motor Driven Systems: A Guidebook for Industry.
Sources of Information
American Society of Heating, Refrigerating and Air-Conditioning Engineers (ASHRAE). ASHRAE Handbook: HVAC systems and equipment. ASHRAE, Atlanta, GA:. 2008.
DOE (U.S. Department of Energy). (n.d.). Motor Systems. U.S. Department of Energy Office of Energy Efficiency and Renewable Energy Advanced Manufacturing, Washington, DC. https://www.energy.gov/eere/amo/motor-systems.
——. 2012. U.S. Department of Energy's Motor Challenge Program: A National Strategy for Energy Efficient Industrial Motor-Driven Systems. U.S. Department of Energy Office of Energy Efficiency and Renewable Energy Advanced Manufacturing, Washington, DC. https://www.energy.gov/sites/prod/files/2014/05/f16/motor_challenge_national_strategy.pdf
——. 2014. Improving Motor and Drive System Performance: A Sourcebook for Industry. U.S. Department of Energy Office of Energy Efficiency and Renewable Energy Advanced Manufacturing, Washington, DC. https://www.energy.gov/sites/prod/files/2014/04/f15/amo_motors_sourcebook_web.pdf
IntechOpen. 2015. Variable Frequency Drive Applications in HVAC Systems. IntechOpen Limited, London, United Kingdom. https://www.intechopen.com/books/new-applications-of-electric-drives/variable-frequency-drive-applications-in-hvac-systems
Actions and activities recommended in this Best Practice should only be attempted by trained and certified personnel. If such personnel are not available, the actions recommended here should not be initiated.
Published December 2020