- Best Practices for Equipment O&M
-
O&M Best Practice Issue Discussions
- Advanced Maintenance Approach: Reliability Centered Maintenance
- Applying Key Performance Indicators
- Comprehensive O&M Program
- Contract Challenges and Improvements
- Cybersecurity for O&M Systems
- Existing Building Commissioning Procurement
- Healthy Building O&M
- Integrating and Analyzing Building Information to Support O&M
- Maintenance Approaches
- OMETA: An Integrated Approach to Operations, Maintenance, Engineering, Training, and Administration
- Prioritizing O&M Actions
- Re-tuning Buildings
- Tools
- Glossary
O&M Best Practices for On-site Wind Turbines
Table of Contents
- Introduction
- Description of Technology
- Key Components
- Safety Issues
- Maintenance of Technology
- Maintenance Checklist
- Performance Monitoring
- O&M Cost
- Additional Support
- Sources of Information
Introduction
Wind turbines are a widely implemented renewable energy technology in the United States. Although much of the capacity is in utility-scale wind farms, wind turbines are also deployed as on-site distributed energy resources to power schools, businesses, government sites, and other facilities. Wind as a distributed energy resource is often called distributed wind. Unlike utility-scale wind projects, which typically carry power across long distances via transmission lines to distant end-users, distributed wind projects are interconnected behind a customer’s meter to offset on-site electricity use or to the distribution grid to support local loads and grid operations. Distributed wind can also electrify or provide backup power to remote, off-grid assets not connected to a distribution grid. These best practices focus on on-site distributed wind turbines.
A broad range of wind turbine sizes can be used in on-site distributed wind projects. While these best practices are intended to be inclusive of all turbine sizes, the costs and frequency of operations and maintenance (O&M) practices can vary widely between small (e.g., 10 kW) turbines and large multimegawatt turbines. Nevertheless, effective O&M of wind turbines, regardless of size, is necessary to maximize system production and help achieve energy reduction, decarbonization, and resilience goals.
The purpose of this Best Practice is to provide an overview of wind turbine components, maintenance requirements, and reporting considerations to ensure safe and efficient operation of on-site wind turbines. Regular O&M of wind turbines will ensure that systems continue to operate effectively, and tracking operating conditions and performance will also help identify potential issues, maximize savings, and inform future designs and standards. Owners should budget and plan for regular maintenance to ensure continuous operation.
Description of Technology
Wind energy is produced with wind turbines, which use blades to collect the kinetic energy from the wind. These blades form a spinning rotor connected to a generator, which ultimately converts the energy into electricity.
There are various sizes of wind turbines and wind projects. On-site wind turbine installations can range from a less-than-1-kilowatt (kW) wind turbine at a remote cabin or oil and gas platform, to a 15-kW wind turbine at a home or farm, to several multimegawatt wind turbines at a university campus or federal agency facility.
Wind turbine technology can be classified into two categories, according to the configuration of the rotating axis of rotor blades: horizontal axis wind turbines (HAWTs) and vertical axis wind turbines (VAWTs). The rotating axis of HAWTs is parallel to the wind stream, as opposed to the perpendicular configuration of a VAWT (as shown in Figure 1).
The ultimate goal for a wind energy project is to maximize energy production by deploying the most appropriate turbine for the site and wind resource available. HAWTs are the dominant configuration in the marketplace as VAWTs are more challenged in terms of efficiency, performance, and achieving certification to industry standards that address power performance, duration (durability), structural integrity, safety, and acoustic sound (Deign 2019; Fields et al. 2016).
It is recommended to use a wind turbine model that has been tested for performance, sound, safety, and duration at a testing facility and approved for certification by a third-party certification body. For large wind turbines (i.e., generally turbines with peak power ratings of greater than 150 kW), certification can be demonstrated through type certification through IECRE (International Electrotechnical Commission (IEC) System for Certification to Standards Relating to Equipment for Use in Renewable Energy Applications). Type certification includes the design review, manufacturing evaluation, and type testing of a wind turbine model to ensure that product design and performance can meet various safety, function, component, and load standards (Schlipf et al. 2018; NREL 2016). For a small wind turbine (turbines generally having a peak power of 150 kW or less), certification can be demonstrated by being certified through IECRE; to the American Wind Energy Association (AWEA) Small Wind Turbine Performance and Safety Standards 9.1-2009; or to the American Clean Power Association (ACP) 101-1 standard. The AWEA 9.1 and the ACP 101-1 standards both refer to the IEC standards for basic requirements and processes.
A wide range of tower designs and heights are available. Small wind turbines in the United States typically use self-supporting lattice and monopole towers as well as fixed and tilt-up guyed towers. Turbine heights for small wind turbines can range from 10 m (33 ft) to 50 m (164 ft). For turbines greater than 100 kW, towers are primarily monopoles and range from 37 m (121 ft) up to 100 m (328 ft).
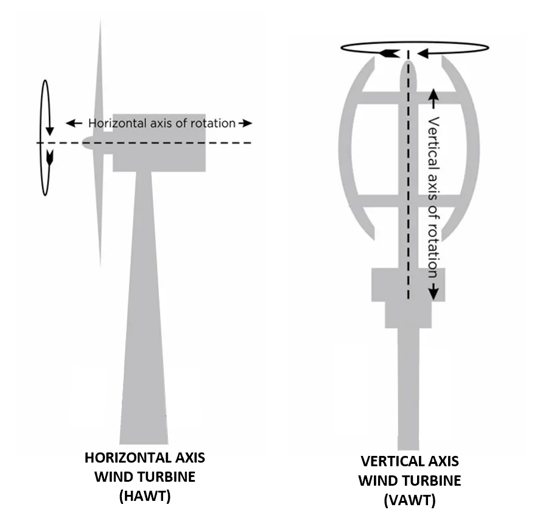
Key Components
The key elements of a wind turbine include the rotor, blades, generator, nacelle, bearings, tower, foundation, and electrical conversion equipment. Some wind turbines also have gearboxes—one of the most maintenance-intensive components of a wind turbine. Direct drive systems do not require a gearbox and therefore have fewer moving parts. Figure 2 compares a wind turbine with a gearbox system to a wind turbine with a direct drive system. The key elements are briefly summarized below.
- Rotor – Rotor blades, typically three, are attached to a hub to form the rotor. The wind spins the blades to turn the rotor. The rotor is connected to the main shaft that is connected to a generator. The generator converts this rotational energy into electrical energy.
- Nacelle – The nacelle is the main casing to which the rotor is attached. The nacelle houses key elements such as the brake, gearbox (if present), and generator. Many nacelles have spinners or nose cones on the leading edge that provide additional weather protection.
- Gearbox – A gearbox is used in some wind turbines to increase rotational speed from the low-speed rotor to the higher speed electrical generator. Not all wind turbines have gearboxes; some are gearless direct-drive machines.
- Generator (also called alternator) – Converts the rotational energy of the rotor into electricity. Some generators use permanent magnets and have an inverted configuration in that the outside housing rotates while the internal windings are stationary, known as direct drive systems. Generators in this configuration produce power at low rotational speeds, eliminating the need for speed-increasing gearboxes.
- Yaw system – The yaw drive rotates the nacelle to keep the wind turbine oriented with the wind.
- Collector ring assembly (also called slip-rings and brushes) – The collector ring assembly is located inside the generator. Slip-rings and brushes conduct electricity generated in the generator from the moving wind turbine (Bergey Windpower 2018). In double-fed induction generators, power is normally transferred to and from the wound rotor using rotating collectors and brush assemblies. These are high-wear items and their regular replacement should be included as a component of the turbine’s O&M agreement (AWEA 2013).
- Bearings – Most wind turbines use grease-lubricated, anti-friction ball bearings that require regular replenishment on both the drive and non-drive ends of the machine. Often, lubrication supply devices are used to partially automate the process, but manual monitoring and adjustments are still required.
- Anemometer – An anemometer on the wind turbine measures the wind speed the turbine rotor is experiencing, and the measurement supports the control operations of the wind turbine (e.g., it determines when the wind speed reaches the turbine’s cut-out [shut-down] speed).
- Tower – Wind turbine towers are either lattice or monopole. Typically, larger wind turbines use freestanding monopoles, while smaller wind turbines can have lattice towers or guyed towers.
- Foundation or footing – The foundation fixes the wind turbine tower to the ground. Foundation design is dependent on soil conditions and size of turbine.
- Inverter – An inverter converts variable electrical energy from the turbine into utility-compatible electricity. Inverters often have digital displays that provide information on system status, such as current output power and cumulative energy production. For a small turbine, the inverter is typically placed in an indoor location, near the main breaker to which it is connected.
- Transformer – Some wind turbines require transformers, while others do not. Small wind turbines with output voltages of 240 V AC can be integrated directly into a breaker box via an inverter, where the distribution grid power is converted to consumer-level power.
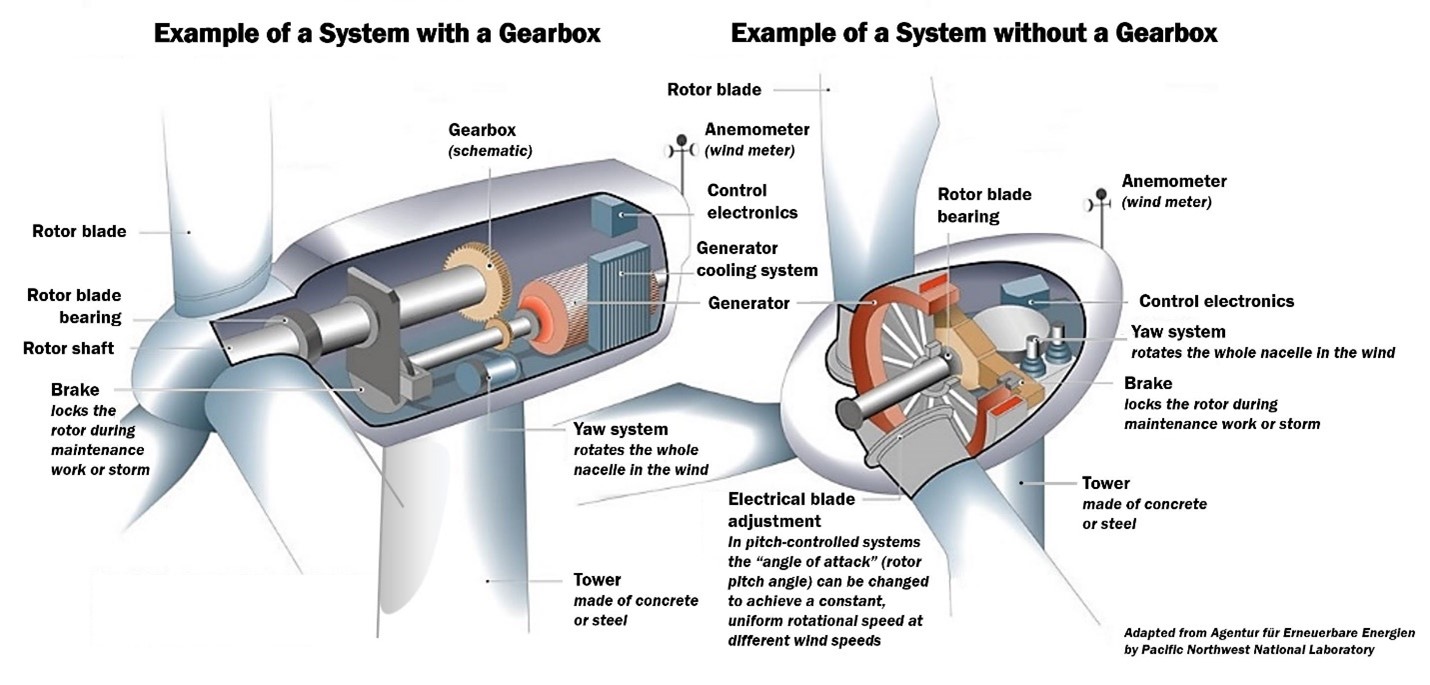
Safety Issues
Servicing a wind turbine can be dangerous and potentially lethal without the correct knowledge and training, because of high voltage, the risk of falling, and proximity to moving parts. Only trained and authorized maintenance providers with approved safety gear should climb to the turbine, open the nacelle, or provide service in a nacelle. The tower should never be climbed while the rotor is running as the output wiring of the generator presents a shock hazard whenever the rotor is turning. Unauthorized personnel should not adjust the turbine in any way or make any design changes.
Each on-site wind turbine installation should have an emergency and safety plan. The plan should include procedures to follow in the event of high wind speeds, thunderstorms, ice shedding, fire, turbine rotation overspeed, visible loose parts, high vibrations, or unusual noise. The emergency and safety plan should also follow the turbine manufacturer’s owner’s manual, which provides details on how to stop the turbine if necessary. In general, the options may include stopping the turbine remotely through the turbine operation software, turning off the circuit breaker, or using the main disconnect switch. This document should be clear, concise, and easily accessible, recognizing the need for knowledge to be passed on when ownership or personnel changes occur or in the event of an emergency.
Maintenance of Technology
Preventive maintenance is maintenance that is scheduled in advance at regular intervals and typically follows a standard checklist (like the example shown below). Preventive maintenance will help keep wind turbines in good working order. Preventive maintenance is typically performed by a contracted maintenance provider but can be done in-house if on-site staff have the proper training. What training would be required for on-site staff to service a wind turbine would be dictated by the original equipment manufacturer (OEM) and the agency’s safety policies.
Predictive maintenance can also be called conditions-based maintenance and is the practice of evaluating the wind turbine through periodic or continuous condition monitoring to estimate the best time to perform maintenance to prevent a failure or performance degradation. With a continuous condition-monitoring system installed on the turbine, operating data is continuously collected and can be reviewed for potential problems, potentially saving large sums of money by avoiding unexpected failure. This approach means the maintenance performed addresses just the actual condition of the wind turbine, and can therefore be more cost-effective than a scheduled, preventive maintenance approach that addresses a comprehensive checklist for each visit. While the maintenance may be more cost-effective, a predictive maintenance approach requires an upfront investment in the monitoring system.
Keeping the wind turbine properly maintained, through preventive and/or conditions-based maintenance, will minimize overall O&M costs, improve turbine performance, and protect the asset. Manufacturer warranties typically cover the first 2 to 5 years of operation. Often, these warranties can be extended to 5 or 10 years. Warranties go into effect upon installation (or within a specified date after shipment) and typically cover the wind turbine, blades, electronic components, and tower (if supplied by the manufacturer) against defects in design, material, and workmanship under normal operating conditions.
An O&M agreement with a professional wind turbine maintenance contractor is recommended for both the warranty period, so that the manufacturer’s recommended maintenance schedule can be adhered to, and after the manufacturer’s warranty period has ended (NREL 2015). An O&M agreement can be performed by an OEM, a third-party service provider, or in-house by the project owner’s staff. O&M could also be performed using a combination of these options. For example, in-house personnel could perform scheduled preventive maintenance and an agreement with OEM could be cover larger-scale, unexpected repairs.
As wind turbines age, maintenance costs may increase as some parts may need to be replaced. Inverters for small wind turbines may need to be replaced after 10 years of operation. Gearboxes in larger turbines, which experience a high degree of operational strain, may also need more frequent repair and eventual replacement.
Key considerations for an O&M agreement include the following (NREL 2015):
- Cost, frequency of, and time involved for scheduled maintenance
- Emergency and safety plans
- Maintenance checklist
- Recommended spare parts inventory list
- How unscheduled maintenance will be addressed
- Desired response time for unscheduled maintenance visit
- Any special skills or training required for monitoring by on-site personnel
- All costs and fees
- Discussion of controls and remote monitoring
- List and costs of components that are expected to need refurbishment or replacement during the system life
For more details on what to include in an O&M Agreement, visit Operations & Maintenance Agreement Considerations for Federal Agency On-Site Wind Energy Projects.
An example maintenance checklist is below and would typically be used on an annual basis. Corrective actions are taken when the inspection of a component reveals a problem. The OEM will recommend a routine maintenance schedule to maintain safe operation of the wind turbine. Repairs and corrective actions should be performed by the authorized maintenance provider. This checklist does not supersede maintenance recommendations from the equipment manufacturers, nor is it a replacement for contracted O&M or warranty services. Not all example checklist items will be applicable to all wind turbine models.
Component |
Action |
Inside Nacelle |
⃣ Prior to servicing, disengage electrical energy sources (e.g., grid power) and stop and secure the rotor and yaw mechanism |
⃣ Check mainframe for cracks both top and bottom |
|
⃣ Inspect alternator shaft for cracks, cracked welds, and warping |
|
⃣ Check that alternator leads are secure and free from corrosion |
|
⃣ Inspect slip rings for signs of arcing damage |
|
⃣ Test brushes and slip rings |
|
⃣ Check for worn or twisted droop cables |
|
⃣ Rotate alternator to ensure it is free from grinding and rubbing noises |
|
⃣ Clean alternator shaft bearings |
|
⃣ Check bearing for seal integrity and grease loss |
|
⃣ Grease/apply lubrication as needed to bearings and other parts |
|
⃣ Check torque on fasteners |
|
⃣ Check brake system functioning |
|
⃣ Note pad thickness and rotor condition |
|
⃣ Inspect (vacuum) brake pad for dust |
|
⃣ Inspect damper – check damper bolts and hardware |
|
⃣ Furl machine and release furling winch to test free unwinding |
|
⃣ Inspect furling cable (particularly at the ends) for corrosion |
|
⃣ Inspect furling cable conduit |
|
⃣ If furling cable is twisted, check the swivel |
|
⃣ Check for cracks and loose hardware on the tail boom and fin |
|
⃣ Inspect tail pivot pin, particularly its fasteners |
|
⃣ Check oil |
|
Blades |
⃣ Inspect blades for chips/cracks and clean blades |
⃣ Check condition of leading and trailing edge of blade |
|
⃣ Check torque on fasteners where blades attach to rotor |
|
Tower |
⃣ Inspect anchor points on foundation and/or guy wires |
⃣ Check torque on anchor points/base bolts to ensure they are secure |
|
⃣ Check for missing bolts |
|
⃣ Check for cracks and corrosion in welds |
|
⃣ Visually check foundation for signs of excess stress |
|
Inverter |
⃣ Power down and inspect inverter |
⃣ Check for burned/broken components |
|
⃣ Inspect connections to ensure they are tight and secure |
|
⃣ Check inverter for dust, dirt, etc. |
|
General |
⃣ Include pictures of any defects or warranty items ⃣ Document maintenance in logbook (e.g., date, time, and personnel conducting the inspection, important events/findings, corrective action taken) |
Performance Monitoring (Measurement and Verification)
Monitoring wind turbine system performance is important to ensure cost savings. Wind energy monitoring systems should be installed on any system for which it is not already standard and should be specified in the contract to ensure proper operation and energy production in out-years (NREL 2015).
Small wind turbines are generally equipped with basic remote monitoring of parameters such as power output, accumulated energy, wind speed, and turbine status. Larger turbines, 100 kW and greater, typically have a more elaborate monitoring system including parameters such as rotational speed, yaw position, component temperatures, and turbine fault codes in addition to power, energy, wind speed and direction. Utility-scale turbines are equipped with sophisticated supervisory control and data acquisition (SCADA) systems enabling both monitoring of turbine data and the issuing of commands to the turbine control system.
If a wind turbine is not producing the amount of energy estimated at the time of installation, it is likely because the site’s wind speed is higher or lower than the estimated wind speed used to predict the annual energy production. To rule out the possibility that lower energy production is the result of a turbine problem, the wind turbine’s power curve can be referenced to determine how much energy the turbine should be producing at the current, given wind speed.
O&M Costs
The term O&M costs is common; however, operation costs differ from maintenance costs and not all on-site wind energy projects experience them equally. Operation costs for wind projects may include land lease payments, remote monitoring, various operations contracts, insurance, and property taxes. Other ongoing expenses, such as general and administrative expenses, taxes, property insurance, depreciation, and workers’ compensation insurance are generally not included in O&M costs. On the other hand, all wind projects require maintenance to provide safe, cost-effective, and reliable power output over the expected equipment life, typically 20 to 25 years, as wind turbines are exposed to highly variable weather conditions and undergo constantly changing loads that lead to mechanical stress.
For large, distributed wind projects, O&M costs are part of the project’s total operating expenses. The Land-Based Wind Market Report reports that operating expenses for recently installed projects (i.e., 2019-2021) are anticipated to average between $33/kW/year and $59/kW/year (Wiser and Bolinger 2022).
For small wind turbines, maintenance by third-party providers includes the costs for labor, travel to the site, consumables, and possible equipment rental. Therefore, small wind turbine maintenance costs can depend on the maintenance provider’s proximity to the project site (i.e., travel costs), the availability of spare parts, and the complexity of maintenance and repairs. Scheduled annual maintenance site-visit costs for a sample of small wind turbine projects that account for labor, travel, consumables, and parts average at about $37/kW per visit (Orrell and Poehlman 2017). This is in line with other data that suggest O&M costs for all types of distributed wind projects are typically $35/kW/yr (NREL 2022).
Beyond the warranty period, O&M costs can be more variable based on actual repair costs for events outside of preventive O&M. Maintenance costs may also increase as the turbine ages.
On-site distributed wind projects, as opposed to centralized utility wind farms, tend to have higher O&M costs for two main reasons. First, with respect to project size, on-site wind energy projects often use a small number of turbines, or more typically just a single wind turbine, and thus do not benefit from the economies of scale available to larger projects. Second, on-site distributed wind projects are often installed in remote or unique locations that increase costs, such as islands (increased transportation costs) and other sites where limited site accessibility may increase labor costs.
Technical Specifications for On-site Wind Turbine Installations: https://www.energy.gov/femp/articles/technical-specifications-site-wind-turbine-installations
Selecting, Implementing, and Funding Distributed Wind Systems in Federal Facilities: https://www.wbdg.org/continuing-education/femp-courses/fempodw037
Distributed Wind for Federal Agencies: https://www.wbdg.org/continuing-education/femp-courses/fempodw111
On-site Wind Energy Project Feasibility Checklist: https://www.energy.gov/femp/articles/site-wind-energy-project-feasibility-checklist
Sources of Information
AWEA (American Wind Energy Association). 2013. AWEA Operation and Maintenance Recommended Practices. American Wind Energy Association, Washington, DC.
Bergey Windpower. 2018. Owner’s Manual: BWC EXCEL 15 Wind Turbine & Powersync III Grid-Intertie Inverter. Bergey WindPower, Norman, OK. https://bergey.com/wp-content/uploads/Excel-15S-Owners-Manual_August-2018_Rev-0.pdf.
Deign, J. 2019. “Floating Offshore Wind Holds Promise for Vertical-Axis Turbines.” Greentech Media. May 10, 2019. Accessed October 10, 2022 at https://www.greentechmedia.com/articles/read/floating-offshore-wind-holds-promise-for-vertical-axis-turbines.
Fields, J. F. Oteri, R. Preus, and I. Baring-Gould. 2016. Deployment of Wind Turbines in the Built Environment: Risks, Lessons, and Recommended Practices. National Renewable Energy Laboratory: Golden, CO. NREL/TP-5000-65622. https://www.nrel.gov/docs/fy16osti/65622.pdf.
NREL (National Renewable Energy Laboratory). 2015. Army Net Zero: Guide to Renewable Energy Conservation Investment Program (ECIP) Projects. NREL/BR-7A40-62947, National Renewable Energy Laboratory, Golden, CO. https://www.nrel.gov/docs/fy15osti/62947.pdf.
NREL (National Renewable Energy Laboratory). 2016. “NREL Distributes Wind Competitiveness Improvement Project Round Four Funding.” Accessed June 14, 2023 at https://electricenergyonline.com/article/energy/category/renewable-energy/59/579908/nrel-distributes-wind-competitiveness-improvement-project-round-four-funding.html.
NREL (National Renewable Energy Laboratory). 2022. “Annual Technology Baseline: Electricity, Distributed Wind.” Accessed on May 8, 2023 at https://atb.nrel.gov/electricity/2022/distributed_wind.
David Schlipf et al. 2018 J. Phys.: Conf. Ser. 1102 012010. Available at https://iopscience.iop.org/article/10.1088/1742-6596/1102/1/012010/pdf.
Wiser, Ryan and Mark Bolinger. 2022. Land-Based Wind Market Report: 2022 Edition. Berkeley, CA: Lawrence Berkeley National Laboratory. https://energy.gov/windreport.
World Wind Energy Association (WWEA). 2015. Wind Turbine Maintenance & Condition Monitoring. World Wind Energy Association, Bonn, Germany. http://wwindea.org/technology/ch03/en/3_4_3.html.