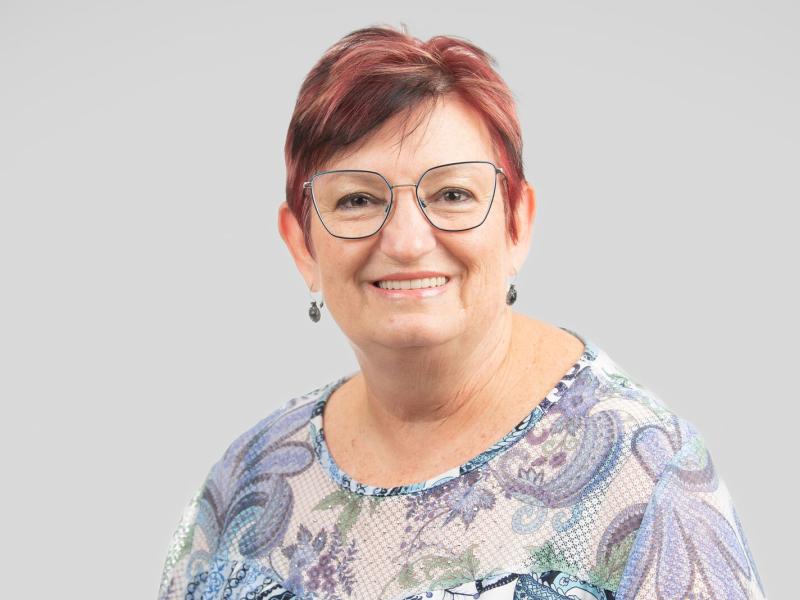
Friction Stir
Welding & Processing
Friction Stir
Welding & Processing
Improved approaches for
joining and manufacturing
Improved approaches for
joining and manufacturing
A researcher with PNNL's friction stir welding machine.
(Photo by Andrea Starr | Pacific Northwest National Laboratory)
Friction stir welding (FSW) is a group of solid phase processing (SPP) techniques that make it possible to join materials that are difficult or impossible to be welded together by conventional means. Friction stir processing is a technique that locally changes the metal properties for improved performance.
Researchers at Pacific Northwest National Laboratory (PNNL) have improved various stir processing methods by adding tools or inventing new ways to ‘stir’ the materials involved to provide improved manufacturing processes or improved products.
Friction Stir Welding
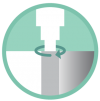
FSW is a joining technique in which a rotating tool plunges into the material, creating “friction” between the tool and the metal that results in localized heating as the tool moves along a path across the material. PNNL has transformed FSW to make it faster and allow it to join metal sheets of varying thickness. Among other things, this means FSW can create all-aluminum parts without rivets and fasteners that increase cost and weight. A commercial production company built around the PNNL process has produced material for full-sized automotive inner door panels.
Friction Stir Dovetail
Friction stir dovetailing allows heavy steel to be joined with thick plates of aluminum—something not possible using conventional welding because the materials have different melting points.
Friction stir dovetailing provides solutions for lighter-weight materials for targeted uses. It’s valuable for manufacturing military combat vehicles, for instance, to lower fuel expenses and increase agility, strength, and operational effectiveness. Applying the same concept as a woodworker’s dovetail joint, researchers form metallic interlocks by using a specially designed tool and precise control of pressure and temperature to deform aluminum into a dovetail groove in the steel.
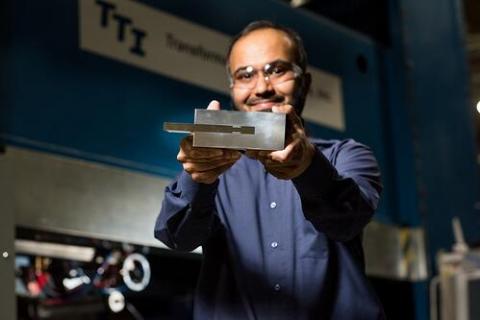
Simultaneously, the tool rubs along the bottom of the dovetail, forming an ultra-thin, iron-silicon layer chemical bond that acts like glue. The resulting joints are lighter and stronger than all-steel components, thereby increasing the efficiency and maneuverability of military vehicles.
Friction Stir Scribe
PNNL's award-winning friction stir scribe process makes it possible to join materials with drastically different melting points with no need for additional adhesives, bolts, and rivets. Using this tool, which is available for licensing, manufacturers can now incorporate new and different materials into a variety of lightweight parts without sacrificing strength or durability.
Joining dissimilar materials—steel and aluminum—through this specialized, award-winning FSW process can produce lighter-weight components for multi-material vehicles, providing greater fuel efficiency and reducing carbon emissions.
Friction Stir Interlocking of Dissimilar (Non-Metal) Materials
Two new SPP techniques have been developed at PNNL to join lightweight materials to composites, plastics, ceramics, or other non-metallic materials in a single pass. This technology can be used to reduce the weight of automotive components, or any application—for example bridges—where robust joints between magnesium or aluminum and non-metals are required.
The first approach involves embedding metal inserts within the non-metal, and subsequently friction stir welding the metal sheet or plate directly to the metal insert. The second involves inserting metal pins through the non-metal, much like a rivet, and then friction stir welding the metal sheet or plate directly to the metal insert to form a mechanical fastener. Friction stir interlocking also reduces the galvanic and pitting corrosion that can occur between metal fasteners and carbon fibers within composite materials.
Rotational Hammer Riveting
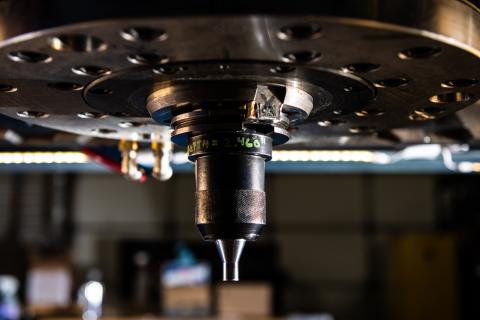
Rotational hammer riveting was developed by PNNL to join dissimilar materials quickly without preheating rivets.
This friction-based riveting enables use of lightweight magnesium rivets but also works on aluminum. It is extremely fast, reducing the time needed to rivet from one – two seconds per rivet to just a quarter of a second—saving time and cost of manufacturing. It is available for licensing.
Friction Stir Processing
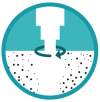
Friction stir processing (FSP) is a variation on FSW. A spinning, non-consumable tool is translated along the surface of a material to form a modified region with improved properties compared to the base material. The approach is used to selectively modify alloys such that the resulting components and assemblies exhibit locally enhanced properties and deliver high materials performance in the locations most needed. This allows for significant improvements in manufacturability, structural efficiency, and weight savings of next-generation vehicles. Furthermore, FSP enables the right properties, in the right locations, and provides the opportunity to decrease the number of metal alloys required for new vehicle manufacture—reducing the challenges that automakers face today in managing supply chains, assuring materials sustainability, and efficiently recycling scrap metal.
Robust Temperature Control for FSW
PNNL researchers have developed robust temperature control methods with unprecedented thermal control accuracy across the length of a friction stir weld. Important weld properties, such as fracture toughness and corrosion resistance, vary with weld temperature. This temperature can be adjusted during the weld for quality and creation of specified properties. Precise control of temperature has enabled PNNL to achieve unprecedentedly low-temperature welds and superior properties in steels. This is more energy efficient and requires less processing. Temperature control can drive higher speeds and accommodate lower part tolerances, increasing the value proposition of friction stir processing for high volume manufacturers.