- Best Practices for Equipment O&M
-
O&M Best Practice Issue Discussions
- Advanced Maintenance Approach: Reliability Centered Maintenance
- Applying Key Performance Indicators
- Comprehensive O&M Program
- Contract Challenges and Improvements
- Cybersecurity for O&M Systems
- Existing Building Commissioning Procurement
- Healthy Building O&M
- Integrating and Analyzing Building Information to Support O&M
- Maintenance Approaches
- OMETA: An Integrated Approach to Operations, Maintenance, Engineering, Training, and Administration
- Prioritizing O&M Actions
- Re-tuning Buildings
- Tools
- Glossary
OMETA: An Integrated Approach to Operations, Maintenance, Engineering, Training, and Administration
Table of Contents
- Introduction
- Discussion
- I. OMETA: “Operations” Functional Area Criteria
- II. OMETA: “Maintenance” Functional Area Criteria
- III. OMETA: “Engineering” Functional Area Criteria
- IV. OMETA: “Training” Functional Area Criteria
- V. OMETA: “Administration” Functional Area Criteria
- Solutions and Actions
- OMETA Application
- Conclusion and Next Steps
- Definitions (FEMP 2010; NASA 2000; NE-SpinTech 2018)
- References
Introduction
The lack of effective operations and maintenance (O&M) strategies to maintain a facility’s infrastructure leads to increased energy use, premature degradation, and less healthy and resilient buildings. The OMETA (Operations, Maintenance, Engineering, Training, and Administration) concept defines the elements of an O&M program that makes use of a holistic approach and considers all elements of supporting infrastructure as integral parts of the larger system.
A functional O&M program is one of the most cost-effective methods for assuring a facility’s reliability, safety, energy efficiency, and overall resilience. Inadequate maintenance of energy-using systems is a major cause of energy waste in both the federal government and the private sector. Energy losses from steam, water, and air leaks, un-insulated lines, maladjusted or inoperable controls, and other losses from poor maintenance are often considerable. Effective maintenance practices can generate substantial energy savings and should be considered a resource. Moreover, improvements to facility maintenance programs can often be accomplished immediately and at a relatively low cost (FEMP 2010).
Figure 1 depicts the performance of a typical facility over time (NRC 1998) where the Y-axis is relative performance and the X-axis is time. As shown, the performance of a system or facility tends to decrease over time. The slope of the decline is a function of the original design, the operating environment, and overall maintenance effectiveness.
The figure shows how, over time, the performance of a building (and its components) will eventually degrade in two scenarios—one with “normal” or effective maintenance and one without. Of interest in the figure is the prolonged service life achieved through effective O&M—the solid curve to the right.

Discussion
From an O&M perspective, most facilities, plants, and systems requiring operational actions and infrastructure upkeep will have some representation of the following five functional areas.
- Operations—functional procedures and actions to enable a facility, process, or system.
- Maintenance—necessary upkeep and repair of a system and its components.
- Engineering—activities related to the design, monitoring, and improvement of a system and its components.
- Training—providing the necessary information and education for a system’s operation and improvement.
- Administration—functional area providing control of goals and resource needs.
OMETA was developed to stem a noticeable trend in poorly developed and performing O&M programs that resulted in detrimental effects on system lifespan and efficiency. The concept acknowledges advances in data collection and availability, control system prevalence, and the continued need for the human interface to assure efficiency.
The OMETA concept becomes very useful in the characterization of an O&M program and identifying missing elements and opportunities. Within each of the five core areas, there is a set of criteria relevant to not only the topic area but also to the other four functional areas. Figure 2 highlights these areas and their relationships.
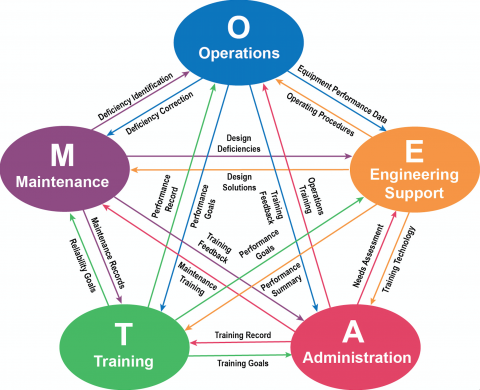
Presented below are the five OMETA functional areas. Each area is presented with the functions that represent the best-in-class criteria and actions to be practiced. In general, each of these functions can be performed in more than one way and still meet the criteria. However, when the criteria are not met, the overall operation, lifespan, and efficiency of the system can be reduced or impaired (Meador 1995).
After each criteria is discussed, a table is presented to highlight the actions and interactions between the five functional areas. Each table presents one of the five OMETA functional areas and then breaks out how that functional area relates to and interacts with the other four OMETA functional areas.
The best application for this information is an organizational assessment of how well each of the five OMETA functional areas are represented within the organization, how well they relate, and what are the missing activities. Note: depending on the organization’s size—more than one functional area may be housed within one organization, e.g., training may be housed under administration, or engineering may be part of operations.
Whatever the configuration and organization, these functional areas should be present, represented, and interact with corresponding areas as integral parts of the whole-system sum.
I. OMETA: “Operations” Functional Area Criteria
- Administration—the goal of this function is to assure effective implementation and control of operation activities.
- Conduct of Operations—to assure efficient, safe, and reliable process operations.
- Plant Status Control—to be cognizant of the status of plant systems and equipment.
- Operator Knowledge and Performance—to assure that operator knowledge and performance will support safe and reliable plant operation.
- Operations Procedures and Documentation—to provide appropriate procedural direction that can be effectively used to support efficient, safe, and reliable operation of the plant.
Table 1. OMETA “Operations” functional disaggregation actions and process.
OMETA Functional Area: Operations |
||
Interface Functional Area |
Actions/Interactions |
Process |
Maintenance |
Deficiency identification/ Deficiency correction |
Interface to communicate issues and deficiencies with the Maintenance Function, who then facilitates correction |
Engineering |
Equipment performance data/ Operating procedures |
Provide performance data to the Engineering Function, who then supports with operating procedures |
Training |
Training feedback/ |
Offer input and feedback on training options to the Training Function, who then facilitates these actions/events |
Administration |
Performance record/ Performance goals |
Provide inputs, results, and metrics to the Administrative Function, who then documents and sets goals |
II. OMETA: “Maintenance” Functional Area Criteria
- Administration—to assure effective implementation and control of maintenance activities.
- Work Control System—to control the performance of maintenance in an efficient and safe manner such that economical, safe, and reliable plant operation is optimized.
- Facility Material Condition—to maintain the facility in a condition that supports efficient and reliable operation.
- Conduct of Maintenance—to conduct maintenance in a safe and efficient manner.
- Preventive Maintenance—to contribute to optimum performance and reliability of facility systems and equipment.
- Predictive Maintenance—to function at the highest level of maintenance with measurements that detect the onset of system degradation (lower functional state), thereby allowing causal stressors to be eliminated or controlled before any significant deterioration in the component physical state.
- Maintenance Procedures and Documentation—to provide directions when appropriate for the performance of work and to assure that maintenance is performed safely and efficiently.
- Maintenance History—to support maintenance activities, adjust maintenance programs, optimize equipment performance, and improve equipment reliability.
- Maintenance Facilities and Equipment—to effectively support the performance of maintenance by providing adequate facilities and equipment.
- Materials Management—to assure that necessary parts and materials meeting quality and design requirements are available when needed.
- Maintenance Personnel Knowledge and Performance—to keep maintenance personnel knowledge and performance at a level that effectively supports efficient, safe, and reliable operation.
Table 2. OMETA “Maintenance” functional disaggregation actions and process.
III. OMETA: “Engineering” Functional Area Criteria
- Engineering Support Organization and Administration—to assure effective implementation and control of technical support.
- Plant Modifications—to assure proper design, review, control, implementation, and documentation of plant design changes in a timely manner.
- Plant Performance Monitoring—to perform monitoring activities that optimize plant reliability and efficiency.
- Engineering Support Procedures and Documentation—to assure that engineer support procedures and documents provide appropriate direction and that they support the efficiency and safe operations of the plant.
- Document Control—document control systems should provide accurate, legible, and readily accessible information to support station requirements.
Table 3. OMETA “Engineering” functional disaggregation actions and process.
IV. OMETA: “Training” Functional Area Criteria
- Administration—to assure effective implementation and control of training activities.
- General Employee Training—to assure that plant personnel have a basic understanding of their responsibilities and safe work practices and have the knowledge and practical abilities necessary to operate the plant safely and reliably.
- Training Facilities and Equipment—the training facilities, equipment, and materials effectively support training activities.
- Operator Training—to develop and improve the knowledge and skills necessary to perform assigned job functions.
- Maintenance Training—to develop and improve the knowledge and skills necessary to perform assigned job functions.
- Emergency Response Training—to develop and improve the emergency mitigation knowledge and skills of emergency response personnel.
Table 4. OMETA “Training” functional disaggregation actions and process.
OMETA Functional Area: Training |
||
Interface Functional Area |
Actions/Interactions |
Process |
Operations |
Operations training options/ Training feedback |
With interaction and feedback from the Operations Function, develop and/or facilitate appropriate training activities |
Maintenance training options/ Training feedback |
With interaction and feedback from the Maintenance Function, develop and/or facilitate appropriate training activities |
|
Engineering |
Needs assessment/ Training technology options |
Develop needs assessment specific to the Engineering Function offering specifics on relevant technologies |
Administration |
Training record/ Training goals |
Interaction with the Administration Function to document all training events and records while assessing current/future goals |
V. OMETA: “Administration” Functional Area Criteria
- Organization and Administration—to establish and assure effective implementation of policies and the planning and control of O&M activities.
- Management Objectives—to formulate and utilize formal management objectives to improve O&M performance.
- Management Assessment—to monitor and assess O&M activities to improve all aspects of O&M performance.
- Personnel Planning and Qualification—to assure that O&M positions are filled with highly qualified individuals.
- Industrial Safety—to achieve a high degree of personnel and public safety.
Table 5. OMETA “Administration" function disaggregation actions and process.
OMETA Functional Area: Administration |
||
Interface Functional Area |
Actions/Interactions |
Process |
Operations |
Performance goals/ Performance record |
Assess and develop performance goals for the Operations Function, who then provides a performance record |
Maintenance |
Reliability goals/ Reliability record |
Assess and develop reliability goals for the Maintenance Function, who then provides a reliability record |
Engineering |
Performance goals/ |
Assess and develop performance goals for the Engineering Function, who then provides a performance record |
Training |
Training goals/ |
Assess and develop training goals for the Engineering Function, who then provides a training record |
Solutions and Actions
OMETA Application
The OMETA criteria are best applied as a site characterization protocol leading to an integrated facilities strategy. This protocol can be implemented using the following step-wise process.
1. OMETA Team Development
- Each of the five areas has its own team lead who coordinates and organizes the information from all team members for that area.
- After a review of the facility and its operation, a discussion of any available facility information (prior reports, audits, utility bills, etc.) will prepare the team for the site visit.
2. Site Visit
- At the site, the team uses the criteria protocol and systematically gathers information on each of the functional areas.
- The OMETA criteria are designed as topical areas of conversation and guidance to facilitate the sharing of information.
- These criteria should be discussed in real terms with examples of compliance and non-compliance requested whenever possible.
- The team also establishes an efficiency baseline at both the component and facility performance levels, making use of any available metrics or key performance indicators (KPIs).
- The efficiency baseline should quantify, where possible, actual operational metrics (KPIs) of the facility. Relevant KPIs could include:
- downtime percentage
- rework percentage
- resource use intensity
- preventive/predictive maintenance efficacy.
- The efficiency baseline should quantify, where possible, actual operational metrics (KPIs) of the facility. Relevant KPIs could include:
3. Observations Compiled
- A master list of observations, metrics, and KPIs is developed and used to derive the full set of improvement opportunities for the facility.
- A critical systems analysis is performed to narrow the list to the critical improvement opportunity areas that are truly necessary for the safety, reliability, and efficiency of the facility.
4. Opportunity Evaluation
- Within each of the OMETA areas, operational efficiency improvements are to be ranked by a “value-impact” ratio.
- The ratio will be developed with assistance from site staff and may be developed as a traditional benefit-to-cost ratio (when cost data are available) or may relate to other metrics or KPIs such as downtime, work order completion, safety, security, or resilience.
5. Implementation
- The final rankings of opportunities are sorted by value-impact ratio but maintain their functional OMETA area identity.
- O&M managers can now sort and review opportunities and their relative impact across the organization and look for those opportunities that have the best cross-organizational impacts.
Conclusion and Next Steps
The OMETA approach to O&M program characterization and evaluation allows for a holistic methodology that considers all aspects of the five functional areas as integral parts of the system. By looking at the entire system, including how functional areas interact, the opportunities for improvement, and the outcomes across multiple organizations, there will be a greater potential for significant and lasting impact.
The process begins with the development of an OMETA team composed of members from the five functional areas. These members work to develop and implement the OMETA strategy by completing site and organizational audits, compiling these into a central database of findings, assessing these findings to convert them to opportunities, and finally prioritizing these into an implementation plan.
Definitions (FEMP 2010; NASA 2000; NE-SpinTech 2018)
- Asset. Maintenance term commonly taken to be any item of physical plant or equipment.
- Backlog. Work that has not been completed by the nominated required-by date. The period for which each work order is overdue is defined as the difference between the current date and the required-by date.
- Benchmarking. The process of comparing performance with other metrics or organizations.
- Downtime. The time that an item of equipment is out of service as a result of equipment failure.
- Failure. An item of equipment has suffered a failure when it is no longer capable of fulfilling one or more of its intended functions.
- Key Performance Indicators. A select number of key measures that enable performance against targets to be monitored.
- Maintenance. Any activity carried out on an asset to assure that the asset continues to perform its intended functions or to repair the equipment.
- Mean Time Between Failures (MTBF). A measure of equipment reliability equal to the number of failures in a given time period, divided by the total equipment uptime in that period.
- Operational Efficiency. The actual output produced from an asset in a given time period divided by the output that would have been produced from that asset in that period had it produced at its rated capacity. Normally expressed as a percentage.
- Reliability. The ability of an asset to continue performing its intended functions. Normally measured by mean time between failures.
- Repair. Any activity that returns the capability of an asset that has failed to a level of performance equal to or greater than that specified by its functions, but not greater than its original maximum capability. An activity that increases the maximum capability of an asset is a modification.
- Risk. The potential for the realization of the unwanted, negative consequences of an event.
- Shutdown. That period of time when equipment is out of service.
- Unscheduled Maintenance. Any maintenance work that has not been included on an approved maintenance schedule before its commencement.
- Uptime. The time that an item of equipment is in service and operating.
- Useful Life. The maximum length of time that a component can be left in service before it will start to experience a rapidly increasing probability of failure.
- Work Order. The prime document used by the maintenance function to manage maintenance tasks. It may include such information as a description of the work required; the task priority; the job procedure to be followed; the parts, materials, tools, and equipment required to complete the job; the labor hours, costs, and materials consumed in completing the task; and key information on failure causes, what work was performed, etc.
References
FEMP ─ Federal Energy Management Program. 2010. Operations & Maintenance Best Practices: A Guide to Achieving Operational Efficiency. Release 3.0. Prepared by Pacific Northwest National Laboratory for FEMP, Richland, WA. https://www.wbdg.org/FFC/DOE/DOECRIT/femp_omguide.pdf
Meador, Richard J. 1995. Maintaining the Solution to Operations and Maintenance Efficiency Improvement. Pacific Northwest National Laboratory, Richland, Washington. https://www.pnnl.gov/dsom/publications/26005.pdf
NASA – National Aeronautics and Space Administration. 2000. Reliability Centered Maintenance Guide for Facilities and Collateral Equipment. National Aeronautics and Space Administration, Washington, D.C. https://www.hq.nasa.gov/office/codej/codejx/Assets/Docs/RCMGuideMar2000.pdf
NE-SpinTech 2018. Glossary of Maintenance Terms. New England SpinTech: Reliability and Maintenance Solutions. Spencer, MA. Accessed at https://www.ne-spintech.com/wp-content/uploads/2018/04/Glossary-of-Maintenance-Terms.pdf
NRC – National Research Council. 1998. Stewardship of Federal Facilities: A Proactive Strategy for Managing the Nation’s Public Assets. The National Academies Press, Washington, D.C. https://www.nap.edu/catalog/6266/stewardship-of-federal-facilities-a-proactive-strategy-for-managing-the
Actions and activities recommended in this Best Practice should only be attempted by trained and certified personnel. If such personnel are not available, the actions recommended here should not be initiated.
Published July 2021