- Best Practices for Equipment O&M
-
O&M Best Practice Issue Discussions
- Advanced Maintenance Approach: Reliability Centered Maintenance
- Applying Key Performance Indicators
- Comprehensive O&M Program
- Contract Challenges and Improvements
- Cybersecurity for O&M Systems
- Existing Building Commissioning Procurement
- Healthy Building O&M
- Integrating and Analyzing Building Information to Support O&M
- Maintenance Approaches
- OMETA: An Integrated Approach to Operations, Maintenance, Engineering, Training, and Administration
- Prioritizing O&M Actions
- Re-tuning Buildings
- Tools
- Glossary
Existing Building Commissioning Procurement
Table of Contents
- Introduction
- Discussion
- The EBCx Process in Six Phases
- EBCx Qualifications, Skills, Roles, and Responsibilities
- Contracting Elements of an EBCx Effort
- Conclusion
- Additional Resources
- Definitions
- References
Introduction
This Best Practice provides information on existing building commissioning (EBCx) and options for procuring EBCx services. EBCx is a systematic process for investigating, analyzing, and optimizing the performance of building systems by identifying and implementing low-cost/no-cost measures to ensure systems are fully functional in accordance with the building owner’s project requirements. EBCx ensures that building systems perform interactively to meet current facility requirements and provide tools to support the continuous improvement of system performance over time. According to the Energy Independence and Security Act of 2007 (EISA 2007, 42 U.S.C. 17001) and the Energy Act of 2020 (EA 2020, 42 U.S.C. 8253), there are three distinct approaches to EBCx compliance:
- Retrocommissioning (RCx)
- Recommissioning (ReCx)
- On-going commissioning (OCx, also known as monitoring-based commissioning, MCx).
EBCx is a comprehensive term defining a process that encompasses the more narrowly focused variations (e.g., RCx, ReCx, OCx/MCx) commonly used in the industry (BCA 2008). This Best Practice focuses on the heating, ventilation, and air conditioning (HVAC) and HVAC controls systems that drive the energy and water use at the facility. It is important to note that while EISA 2007 and other requirements can distinguish between RCx and ReCx based on whether initial commissioning was performed, this Best Practice considers the associated approaches and practices of existing building commissioning as effectively identical and instead uses the general term EBCx to apply to all cases.
Discussion
Relevant History
The EBCx process is designed to reduce reactive repairs, improve building system performance, and maintain energy and water efficiency in existing buildings. In addition to these practical benefits, this process is highlighted in requirements found in EA 2020 and is mandated under Section 432 of EISA 2007. Under that section, agencies are required to implement measures identified in the comprehensive energy and water evaluations and ReCx or RCx for approximately 25 percent of “covered facilities not less than every four years.” This 4-year cycle is intended to make sure savings for implemented energy and water efficiency projects are persistent.
Interested Parties
The key individuals responsible for EBCx activities include but are not limited to operations and maintenance (O&M) staff, energy managers, building information managers, and other personnel required to comply with requirements for building decarbonization and energy and water savings enacted into law by EA 2020.
Existing Standards and Policy
Agency energy projects will enable progress toward several administration and congressional priorities focused on energy and water efficiency, decarbonization, investment, jobs, and American manufacturing. The acts and statutory requirements related to EBCx are described below. Figure 1, while not comprehensive, illustrates the relevant requirements.
Statutory Requirements
The EA 2020 focuses on energy retrofits and overall energy and water efficiency in federal buildings. The act touches on all aspects of optimal system energy and operational performance.
EISA 2007 established the mandate for EBCx to be competed for approximately 25 percent of covered federal facilities not less than every 4 years.
Executive Orders
The Executive Order (EO) 14057 (signed 2021), Catalyzing Clean Energy Industries and Jobs Through Federal Sustainability, which established requirements to reduce scope-1 and scope-2 greenhouse gas emissions to achieve net-zero emissions buildings. Under this EO, agencies shall pursue building electrification strategies in conjunction with carbon pollution-free energy use, deep-energy retrofits, whole-building commissioning, energy and water conservation measures, and space reduction and consolidation.
Other Guidelines
Updated High Performance and Sustainable Building Guidance was issued by the Office of Management and Budget (signed in December of 2008). This update offers revised guidance and a new set of Guiding Principles for Sustainable Federal Buildings. Section 548(a) of the National Energy Conservation Policy Act (NEPCA, 42 U.S.C. 8258(a)) requires each federal agency to submit to the U.S. Department of Energy (DOE) an annual report describing activities to meet the energy management requirements of Section 543 of NECPA (42 U.S.C. 8253).
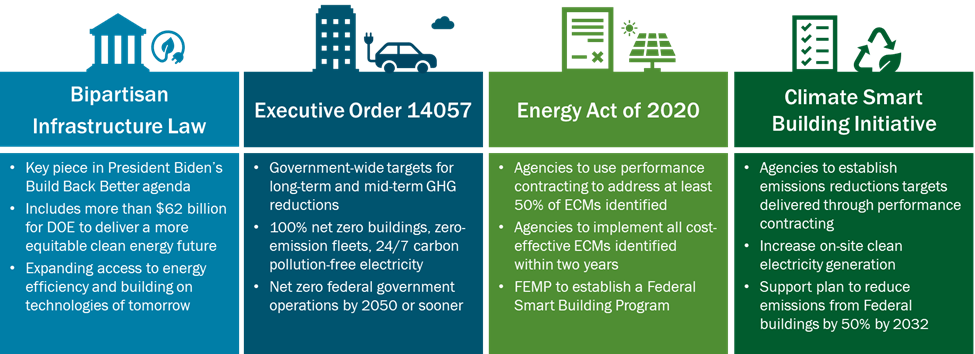
The EBCx Process in Six Phases
This document adapts the phased approach to the EBCx process introduced in American Society of Heating, Refrigerating and Air-Conditioning Engineers (ASHRAE) Guideline 0.2-2015, Commissioning Process for Existing Systems and Assemblies. Other organizations such as the Building Commissioning Association and the Construction Engineering Research Laboratory also use the six-phase process in their EBCx guidance documents. These six phases, highlighted in Figure 2, serve as the foundation for this Best Practice.
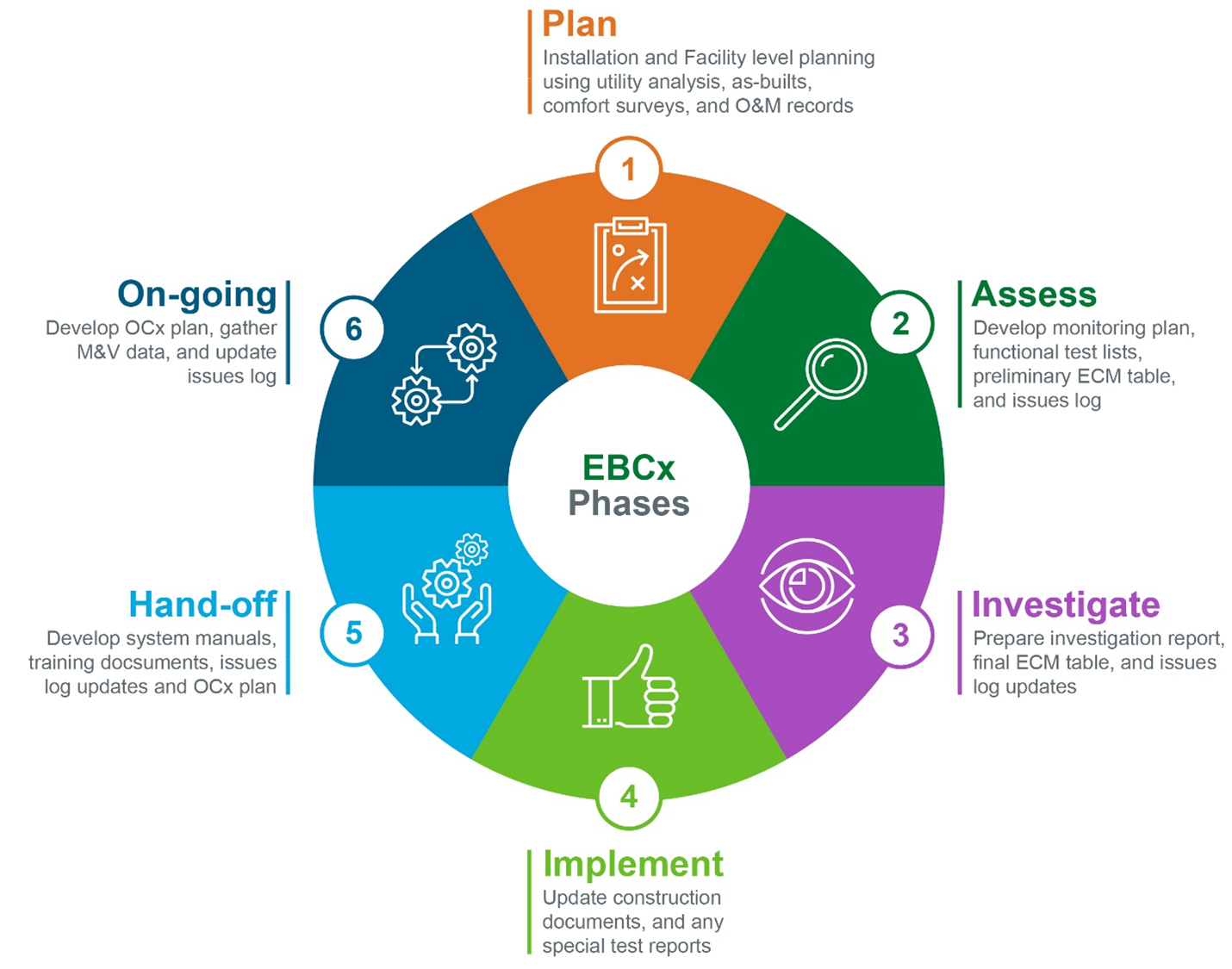
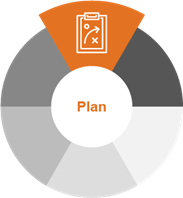
Planning Phase
The Planning Phase consists of a combination of efforts focused on planning at both the installation level and the facility level. The goal of installation-level planning is to establish and prioritize a set of candidate buildings for the EBCx Assessment Phase. The goal of facility-specific planning is to compile and evaluate facility documentation in preparation for an EBCx assessment.
An important outcome of the Planning Phase is determining which of the subsequent phases will likely be contracted and which will remain as in-house activities. This decision will be made during the planning process, carefully noting at each step whether in-house capability (and capacity) exists to complete the activity.
In-house completion of the Planning Phase tasks is preferable; however, if site/facility staff is limited, it may be necessary to rely on external support or to focus on key planning steps only (refer to Figure 3). Regardless, some in-house planning must occur to ensure the EBCx assessment process is strategically executed and yields valuable results. Answers to the following questions will assist in planning for in-house or contracted EBCx efforts:
- What facilities should be assessed and in what priority?
- Which systemic issues or pervasive opportunities specific to your installation should be included in the Assessment Phase?
- Are there clues about potential energy drivers derived from utility data, as-built documents, climate trends, or occupant usage?
Installation-Level Planning
Because of their detailed nature, EBCx assessments should be limited to facilities that meet specific size or operational criteria. Following DOE guidelines on EISA 2007 compliance, the initial EBCx candidate pool should be established from designated covered facilities that are greater than 50,000 square feet (50 KSF [thousand square feet]) and facilities greater than 25 KSF that house energy-intensive operations (DOE 2008).
Further assistance with EBCx planning is available via the Federal Energy Management Program (FEMP) EBCx Decision Tool. This tool guides users through the process of identifying the requirements for EBCx and determining whether a facility meets the exceptions, and if not, which EBCx approaches to consider.
An EBCx Plan documents the approach taken to install EBCx. At a minimum, it should record the EBCx building candidates identified and indicate which EBCx assessments will be performed when and by whom. While a spreadsheet of buildings could constitute an installation’s EBCx Plan, a best practice is to develop a more comprehensive report that specifies installation-tailored strategies.
The following should be considered and documented as part of the installation-level EBCx Planning Phase:
- Develop a list of EBCx candidates by selecting buildings greater than 50 KSF (or greater than 25 KSF if energy-intensive) from the installation’s top 75 percent of covered facilities. See page 8, Section B. Commissioning Component of Evaluations (DOE 2008).
- Prioritize EBCx candidates based on energy intensity, size, building automation system (BAS) capabilities, known comfort, O&M or efficiency issues, and energy costs.
- Establish target years for performing EBCx assessments of each facility (or a representative facility for groups of identical facilities) such that all EBCx candidates will be assessed in a 4-year cycle.
- Determine the degree to which EBCx assessments (or follow-on investigations) will be done in-house, contracted, or through some other means of government support.
- Specify roles, responsibilities, and staffing/competency gaps for tasks such as EBCx reporting, BAS operation, O&M coordination, and EBCx tool utilization.
- Outline additional EBCx approaches that may include standardized benchmarking, energy conservation measure (ECM) lists, occupant/O&M surveys, and/or measurement and verification (M&V) processes.
Facility-Level Planning
In preparation for an EBCx assessment at a specific facility, the most important step is to employ some level of utility data evaluation. A recommended best practice is to review impactful information, such as as-built construction documents, climate data, interval meter data, O&M records, occupant surveys, and/or previous audits or assessments.
As part of the impactful data review, the following should be considered for facility-specific planning prior to starting the EBCx Assessment Phase:
- Evaluate utility billing information and perform some form of benchmarking to establish facility energy use intensity (EUI), comparable facility EUI, and changes in EUI over time.
- Use as-built documentation to determine likely energy drivers and possible ECMs to assess.
- Recognize how specific climate factors may drive performance in your systems.
- Review interval energy metering data, if available, to determine how base loads vary at startup, during peak periods, during off-hours, and over time to identify any potential ECMs that may require further evaluation. If desired, strategize on how to improve energy metering and/or building automation infrastructure.
- Use O&M records or occupant thermal comfort surveys, if available, to establish additional EBCx assessment criteria and goals.
One additional best practice is the development of a Current Facilities Requirement (CFR). Similar to an Owner’s Project Requirement in new construction projects, the CFR is intended to capture overall facility management goals of existing facilities (ASHRAE 2014). For EBCx purposes, this may include any of the following:
- Building schedules: Daily occupied and unoccupied schedules as well as exception days (e.g., federal holidays) for the building and/or individual spaces
- Operational setpoints: Occupied and unoccupied (or standby) space temperature, humidity, or carbon dioxide setpoints, and ranges
- Goals: Readiness or sustainability goals associated with the facility (e.g., target EUIs, redundancy, O&M trouble calls)
- Controls needs: References or constraints related to specific sequence of operation (e.g., support for or avoidance of certain setpoint reset strategies)
- Space modifications: Any space configuration or criteria changes since design.
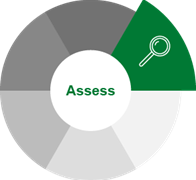
Assessment Phase
The goal of the on-site EBCx Assessment Phase is to record facility system conditions, identify obvious performance issues, and flag potential opportunities for more in-depth analysis. For each potential opportunity identified, the energy calculations, performance data, or functional tests that would help qualify or quantify opportunities need to be considered and documented.
There are several techniques, resources, and on-site staff that can help with this assessment; however, it starts with looking for obvious clues reflecting the underperformance of systems, mapping how key systems are configured and operating, and developing specific requirements to strategically guide follow-on investigation tasks where required.
Typical EBCx Systems to Assess
Any energy- or water-using system may be evaluated during an EBCx assessment; however, a focus on specific systems may be warranted based on the findings from the Planning Phase or the recommendations of facilities management staff. Typically, HVAC and lighting systems with either overly simplistic or overly complicated control strategies are the best candidates for assessment. Examples of types of systems worth considering include:
- BAS: Sensors, actuators, and interfaces in pneumatic, electrical, or digital control systems that could cause errors, communication issues, and improper setpoints.
- Air-side systems: Various types of air-handling units and their zone counterparts that facilitate HVAC load management and ventilation across a spectrum of operating conditions.
- Chilled water systems: Typically, vapor compression chillers (although sometimes absorption or evaporative cooling) serving hydronic coils to space or ventilation.
- Condenser water systems: Where water-cooled chillers are employed, cooling towers and water-side economizer heat exchangers connected to chiller condenser barrels for heat rejection purposes.
- Hot water or steam systems: Hydronic or steam systems serving hot water heat exchangers to offset envelope losses, tempered ventilation air, or reheat supply air typically via centralized gas-fired boilers, although possibly in cogeneration or solar hot water configurations.
- Domestic hot water systems: Electric or gas-fired water heaters or boilers directly or indirectly heating and possibly storing potable water for showers, sinks, or cooking.
- Non-potable water systems: Rainwater, greywater, or other alternative water systems used for non-potable end uses.
- Pumping systems: For all the above water-side systems, pumping systems that optimize flows, pressure losses, and runtimes.
- Lighting systems: Interior and exterior lighting systems that provide space-specific lumen levels at various efficacies through a combination of switched, scheduled, or photocell controls.
- Other systems: Plug-loads and renewable systems as desired.
General Assessment Strategies
Start the EBCx assessment process by coordinating the on-site visit. Building management, O&M, and BAS representatives should be aware of your presence and know the purpose of your visit and presence in the facility. Be clear about your needs for access to space and equipment. Ideally, you should schedule times early in the process to interview each representative to document and address any known issues, operational nuances, and/or concerns with the EBCx process. Subsequently, compile your installation-level and facility-level planning assessment documents and reconcile them with the information from the interviews with building representatives. The objective of the Assessment Phase is to identify all readily noticeable indicators of poor performance.
- Begin the assessment by walking around and through the building, stopping at each representative system type and equipment mechanical room(s).
- With permission, take pictures of major equipment (and nameplates) for selected systems.
- Record equipment nameplate data and observed system setpoints. Nameplate data may be needed to look up equipment capacities, performance curves, and other design parameters. Setpoints can be found at the BAS front end, on local BAS display panels, at some field controllers, or at equipment interfaces.
- Sketch field system diagrams or verify one-line drawings provided by building staff, to validate the existing configuration of piped or ducted central systems. These diagrams, which may also be found on BAS screens, can be critical in recognizing and communicating improper system operations, monitoring needs, and improvement opportunities.
- Note any operational issues found as well as any underlying problems or impacts to utilities, O&M, and/or occupant comfort. These observations may lead to potential ECMs.
Specific Assessment Strategies
Throughout the EBCx assessment, develop a list of potential ECMs. Although each facility will have its own energy use pattern and ECMs, it is helpful to be aware of the common EBCx measures that tend to produce the most impact in terms of energy savings.
Table 1 lists the results of a study that reviewed 122 EBCx projects with more than 950 EBCx measures (NREL 2017). Almost half of the total savings opportunities identified result from three categories of measures: (1) re-tuning™ of control sequences, (2) reduction in equipment runtime, and (3) optimization of air-side economizers. These three measures also form the core principles of PNNL’s Re-Tuning™ Program, which focuses on improving performance in existing buildings.
Table 1. Average energy savings impact of common existing building commissioning (EBCx) measures
Existing Building Commissioning (EBCx) Measure | Percentage of Study Total Savings |
---|---|
Revise control sequences |
21% |
Reduce equipment runtime |
15% |
Optimize air-side economizer |
12% |
Add/optimize supply air temperature reset |
8% |
Reduce coil leakage |
4% |
Reduce/reset duct static pressure setpoint |
4% |
Add/optimize optimum start/stop |
3% |
Add/optimize condenser water supply temperature reset |
2% |
Assessment Phase Deliverables
The EBCx Assessment Phase is completed when the appropriate documentation for selected systems has been completed. In some cases, more detailed investigation phases may not be required; however, some level of follow-on investigation can quantify potential ECMs to support effective performance of future EBCx work.
EBCx Assessment Phase Findings List
During the EBCx assessment, the growing number of possible EBCx opportunities observed or suspected should be recorded in an EBCx Findings List. Record the following information:
- Numbered findings by system
- Brief description of the nature and details of each finding
- Type of opportunity (energy/demand/gas/water savings or O&M/comfort improvement)
- Energy calculations, performance data, or functional tests that would help qualify or quantify EBCx opportunities
- Notes section for additional information or reminders
Monitoring Plan
The Monitoring Plan is intended to highlight the procedures used to capture performance data that is used to identify EBCx opportunities. Therefore, developing a Monitoring Plan is a crucial EBCx task to facilitate data logging or trending in the later stages. Whether Monitoring Plan is used to track in-house deployment and collection of portable data loggers and/or BAS trends, or instead serves as the basis for contractor bids to strategically execute the plan, organization is key. The following information should be included in the initial creation of the Monitoring Plan and updated during its execution:
- ECM, system, and location for each desired performance metric;
- source of monitoring (BAS trends versus data logger);
- identification of either BAS point name or portable logger tag information;
- trend length and interval required (specific to each metric);
- dates associated with launching loggers or configuring trends and collecting the data;
- status (launched, installed, lost, broken, collected, etc.); and
- additional notes (e.g., logger port used, location hints, references, and logger calibration dates).
EBCx Investigation Candidates
The next step is to determine whether an EBCx assessment should be followed by a more detailed investigation. In some cases, ECMs may be either limited in number or complexity, sufficiently understood, or sufficiently implemented during the EBCx assessment such that a subsequent EBCx investigation may be deemed unnecessary. Criteria for continuing to the EBCx Investigation Phase may be organization-specific; general examples of good candidates for EBCx investigation include:
- Relatively large, complex, or energy-intensive facilities where additional ECMs can be expected.
- Facilities where insufficient or outdated documentation, inoperable equipment, or faulty automation systems prevented the assessment of targeted systems.
- Instances where trending, testing, or additional use of automation systems is required to better determine the nature of issues and opportunities identified.
- Projects where performance data are needed for capital improvement scope development, utility incentive validation, or replacement equipment sizing.
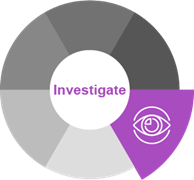
Investigation Phase
The intent of the Investigation Phase is to perform detailed testing and analysis of specific existing systems, reveal operational characteristics, verify the need for changes, and quantify the implementation needed and benefits expected. This EBCx phase is tool- and data-driven, and may be most appropriate for contracting EBCx specialists.
Ultimately, the results from the Assessment Phase drive the tasks in the Investigation Phase, which in turn drive implementation actions. Real-world applications of EBCx can be less linear than this; since new discoveries may require additional review of benchmarking, scoping, or trending steps, it is important to try to distinguish between what is interesting and what is important. With limited time and resources, the Investigation Phase should focus on correcting or improving system performance based on key energy metrics collected.
If you plan to contract for these services, consider targeting specific entities that may better address your specific ECMs. For instance, an energy services contractor may be a good fit to oversee the testing and analysis of a variety of ECMs, but for a controls-specific package of ECMs, a local vendor familiar with your system might be a better choice.
EBCx Instrumentation and Data Requirements
The on-site portion of the EBCx Investigation Phase demands adequate tools to collect the data on performance and response necessary to understand and optimize system performance. The tools and equipment necessary to perform accurate and reliable data collection are often available through local vendors, efficiency organizations, and utilities. In many cases, these devices can be rented or loaned from tool-lending libraries.
When the Investigation Phase is contracted, the contractor is responsible for bringing the requisite equipment (sensors, meters, data loggers, etc.) to the site and make sure they have the necessary experience in its setup, calibration, deployment, and data access. Proper data logging to support EBCx activities typically requires equipment for:
- temperature measurements of both air and water;
- humidity measurements;
- air velocity, pressure, and flow measurements;
- carbon monoxide and carbon dioxide measurements;
- light level and run-time measurements;
- electrical voltage and amperage measurements; and
- infrared and digital photography.
When the Investigation Phase is contracted, it is recommended that the contract contain a provision that requires delivery of copies of all collected data to the site.
Functional Testing
Functional testing can be inherently more intensive and obtrusive than data logging and is often necessary to determine how systems would react to key operating conditions. Regardless of the testing being conducted in-house or by a contractor, approval from site O&M management should be sought first and it is essential to inform the management about the purpose of the test, method, requirements, essential personnel, and conditions under which the effort may be aborted, if necessary. Often, temporary overrides or manipulation of BAS sequences may be necessary to support testing.
As with data logging and when the Investigation Phase is contracted, the contractor should be responsible for providing the requisite tools and ensuring they have the necessary experience for test setup, calibration, deployment, and data access.
Typical instrumentation for proper functional testing can be similar to the data logging equipment but is often used for real-time measurements and is more accurate since it is usually more focused on the specific system being tested. Typical functional testing equipment include:
- non-intrusive ultrasonic flow meter;
- portable flow hood;
- portable combustion analyzer;
- handheld flow, humidity, and temperature measurement instrument; and
- real-time energy (voltage, current, and phase) measurement instrument(s).
Data Analysis, Calculations, and Final ECM List
The next step of the Investigation Phase involves evaluating the data collected during on-site trending and functional testing to draw meaningful conclusions about existing system performance. The goal of this step is to validate the proposed ECMs and quantify the associated savings.
The energy savings calculations should be tied to actual operations by using data collected in the Investigation Phase and applied to the relevant engineering calculations.
Following data analysis and energy calculations, organize final ECM selections by viability and either utility savings or costs. Discuss ECMs with the appropriate stakeholder, such as O&M, BAS, and other relevant building staff, to determine the most appropriate execution method for each ECM and, if possible, separate ECMs by priority and their expected implementation route. The following section provides more information on implementing EBCx ECMs.
Investigation Phase Report
Where contracted or otherwise required, organize the results of the Investigation Phase into a final report. Report contents may be user-defined or project-specific; recommended sections and their contents are listed below:
- Executive summary: Provide a brief narrative on project specific EBCx work performed and final ECM table generated.
- Utilities summary: Include rate schedules used, unit cost rates, usage charts, eligible rebates, and other pertinent information.
- Site activities summary: Describe tasks performed on-site, coordination performed, and items for the Issues and Resolutions Log.
- ECM descriptions: Provide separate breakdowns for each ECM, including discovery, trend, testing, calculations, and assumption processes.
- M&V recommendations: Provide an overview of M&V strategies that can be integrated into an updated Monitoring Plan where ECM validation is required.
- Systems manual information: List any missing or outdated documentation that should be provided as digital or hard copy for O&M staff, such as as-builts; control drawings; points schedule; testing, adjusting, balancing reports; equipment manuals; warranty procedures; performance curves; and laminated system diagram sheets for mechanical rooms.
- Appendix documents: Include any referenced or updated documents, including the Monitoring Plan, functional test sheets, Issues and Resolutions Log, trend logs, meeting minutes, and any other relevant documents.
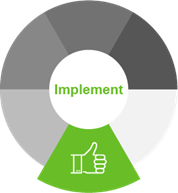
Implementation Phase
For the Implementation Phase, use the most appropriate execution options based on results of the Investigation Phase. You can use existing O&M contract resources or in-house staff or develop a contract for maintenance/repair or replacement of equipment as needed. In some cases, the work may be limited and a simple work order can be developed.
The scope of the Implementation Phase may be as simple as repairing a broken damper or reprogramming a sequence of operation, or it might be a bigger project such as replacing a chiller. Typically, the contract mechanism would be required for repair or replacement work after the Assessment and Investigation phases are completed.
Additionally, the EBCx Implementation Phase requires a verification process to confirm that the completed recommendations meet the CFR.
Verification testing should be executed by an independent contractor or knowledgeable in-house staff once implementation is complete as required in the updated EBCx Plan. Document verification tests and physical inspections are outlined in the EBCx Plan. Records shall include all tests and physical inspection data records, test data, observations, and M&V data. Data may be recorded digitally or with photographs, forms, or other means appropriate for each recommendation. Verify that the performance of the completed recommendations meets the CFR. Performance testing is used to quantify the benefits obtained from these recommendations.
ECMs may be implemented through in-house means, existing contracts, or new acquisition processes. Regardless, use the results of the Assessment or Investigation Phase to set the required tasks during implementation. In order of simplicity, typical execution routes for federal implementation ECMs include:
- O&M work order: Use existing O&M service request mechanisms and work with local O&M staff for small low-cost/no-cost changes to the facility. Examples of this kind of ECM implementation include economizer damper repairs, valve replacements, or lighting system time clock installation.
- BAS programmer: Where changes are required to existing automation system sequences or setpoints, coordinate with the in-house or contracted BAS programmer to back up files, make edits, test changes, and back up the files again.
- Locally funded project: Certain EBCx implementation efforts may be appropriate for short-term, site-discretionary, or other capital funding. These project types can be executed through the site O&M organization, a site operations contract, a job order contract, or the local contracting organization. This type of implementation could include equipment repair, replacement, or retrofit projects to be budgeted in the current or future fiscal year(s).
- Centrally funded project: Where additional funds or end-of-year unobligated money is available through the central agency organization, be prepared with an implementation package that includes the scope of work, government estimates, work request number, and lifecycle cost estimate information to justify the EBCx implementation requested.
- Third-party financing: FEMP provides federal agencies with assistance, resources, and training to use utility energy services contracts (UESCs) or energy savings performance contracts (ESPCs) to implement projects. UESCs are contracts with utility companies, while ESPCs are contracts with energy services contractors. These contract mechanisms are innovative arrangements for designing, installing, and financing energy improvement projects in which the savings achieved by the project are guaranteed to amortize the cost of the project over the term of the agreement. UESCs and ESPCs are typically long-term agreements (more than 10 years) and are adaptable to site-specific needs. For more information and support services for these contracting mechanisms, contact your local contracting office or visit FEMP’s project financing webpage (FEMP 2022).
- Utility rebate: Numerous utility and state-sponsored programs offer technical assistance, energy-efficiency equipment, and/or financial rebates for energy-efficiency projects. Additionally, sometimes there are state and federal grants, tax deductions, and tax credits for select energy-efficiency projects. Funding and program requirements vary widely, but in some instances, funding has covered the total cost of efficiency projects. For information on these programs by state, see the Database of State Incentives for Renewables and Efficiency.
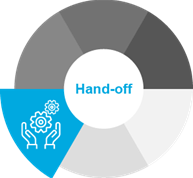
Hand-Off Phase
As with any facilities management implementation work, there is an appropriate way to hand-off system operations to O&M staff. The objective of a hand-off is to fully equip facility staff with the information, insights, and procedures needed to successfully operate and sustain the modified facility. Some tasks for the hand-off transition include:
- Review of special performance testing: Verify that post-installation performance testing demonstrates desired outcomes and that any impacts to the CFR are understood and agreed upon.
- System manuals: Update and augment systems documentation with an implementation and verification report that explains the changes made and the methods followed, and includes inspection and test reports, construction documents, updated Issues and Resolutions Log, operational setpoints, schedules and control sequences, on-going maintenance requirements, calibration procedures, lessons learned, and any other pertinent documentation. Provide information to support maintenance activities, which may include contact information for vendors or potential mechanical servicing, equipment vendor hot lines for operational support, zone maps, and troubleshooting guidelines. Establish that the necessary documentation is complete and has been gathered and deposited in an appropriate location that is accessible to those who need it.
- Operator training: Provide a formal training workshop for building O&M staff that reviews changes made, expected benefits, and lesson learned from the EBCx effort as well as recommendations for on-going operational indicators, troubleshooting, and periodic functional testing procedures. Be sure to include a field-based show-and-tell and ample time for questions and answers. Provide training documentation for future reference.
- OCx Plan: In collaboration with operational staff, develop an OCx Plan that seeks to reduce barriers to sustained idealized operations. Common hurdles include missing documentation, incorrect documentation, lack of contacts for assistance, lack of adequate training, lack of familiarity with equipment or insufficient comfort level with new control schemes, lack of sufficiently distilled operator instructions (cheat sheets) to perform complex procedures, either insufficient or too much utility monitoring and control system alarming, lack of timely feedback on operational changes, insufficient time or funds to address operations, and lack of institutional policies to govern operations. The OCx Plan will include some identification of performance indicators for on-going monitoring, tracking, and reporting of measure persistence.
- Acceptance: Final acceptance and beneficial use of EBCx implementation and hand-off efforts when the above criteria and other project specifics have been met will trigger any warranty start periods and the beginning of the OCx Phase. If project scope calls for post-project return testing, balancing, or verification, make sure contractors and contracts staff are aware of how future scheduling, invoicing, and reporting should be structured.
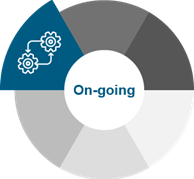
On-Going Commissioning Phase
OCx is a mix of technology, operational, and culture changes intended to improve building energy consumption and continuously optimize building performance during the entire lifecycle. OCx is the process of regularly making sure that building operations continue to be optimized beyond the EBCx Implementation and Hand-Off phases.
Working hand-in-hand with OCx are the techniques and procedures related to monitoring-based commissioning (MBCx) and building re-tuning™. MBCx is the continuous application of the commissioning process to a building or energy system and is an effective method to keep energy costs low and minimize system problems that may be caused over time by building performance deterioration and changes to building operations (NREL 2022). Building Re-Tuning™ is a systematic process aimed at minimizing building energy consumption by identifying and correcting operational problems that plague buildings at no cost or low cost. Re-tuning™ relies on BAS data to identify and implement control improvements at no cost other than the time needed to program the changes (PNNL 2016).
When possible and related to new construction or existing buildings, MBCx and re-tuning should be implemented as early as possible to analyze how the facility is operated and to identify additional EBCx measures and other ECMs. This also provides an opportunity to include MBCx and re-tuning™ in an O&M and/or performance contract, such as an ESPC or a UESC. In case of ESPCs or UESCs, the contract may be modified to include the costs and associated savings of additional measures selected by the customer. As defined within an O&M contract or ESPC/UESC, MBCx could be used to (NREL 2022):
- Generate automated reports and performance verification of each ECM.
- Make sure facility staff are operating equipment according to the project’s contractual requirements.
- Provide remote analysis of system performance.
- Diagnose O&M problems.
- Compare whole facility energy use to expectations.
As a functional output of OCx and by continuously reviewing the selected data, performance patterns will emerge. Deviations from “normal” trends require investigation and action, which can identify out-of-tolerance equipment or variances between expected and actual parameters so equipment and/or systems can be proactively repaired or re-tuned to avoid further unnecessary energy use and cost. Benchmarking also can be used to compare the project to industry standards, such as EnergyStar scores or Commercial Building Energy Consumption Survey (CBECS) data, and/or to compare the data to the expected building operations (as designed) and previous operational data.
On-Going Commissioning Processes
- Benchmarking: Benchmark the building's actual performance through utility bill analysis or an energy management system.
- Develop objectives: Establish a first set of objectives and pick the key performance indicators (KPIs) to monitor. Identify how often you plan to monitor the KPIs.
- Consider options/actions: Review detailed information about daily energy consumption. Track selected performance indicators. If faults are detected, take local action to improve mechanical system performance and to begin generating savings.
- Continuous improvement cycle: Continuous improvement of maintenance activities prevents breakdowns or malfunctions due to excessive wear of equipment. Implementing a robust preventive maintenance process saves energy.
As a final element of this phase, an OCx Plan should be developed to identify all relevant aspects of facility operations and the performance metrics to be tracked. This plan can be developed at any time but is particularly valuable following the EBCx Implementation Phase. The plan should include the following:
- An introduction that includes a discussion of building systems.
- A discussion that provides an understanding of the EBCx implemented measures.
- A discussion of O&M persistence activities.
- A discussion of building energy tracking performed over time (benchmarking, energy-use analysis, and functional testing.)
- A review of training needs.
- Appendices (consider including EBCx reports, CFRs, sequence of operations, a sensor recalibration plan, issues and resolutions list, and other relevant information).
OCx is typically a mix of technological, operational, and cultural changes intended to improve building energy consumption and continuously optimize building performance during its entire lifecycle. It is the process of regularly making sure that building operations continue to be optimized beyond the EBCx Implementation and Hand-Off phases.
By continuously reviewing the selected data, performance patterns will emerge. Deviations from the “normal” trends require investigation and action, which can identify out-of-tolerance equipment so it can be repaired or re-tuned to avoid further energy use and associated costs.
Benchmarking is used to compare the facility to industry standards, such as EnergyStar scores or CBECS data, or to compare the data to expected building operations (as designed) and previously collected operational data. The data comparison is used to find variances from normal operations and identify maintenance problems in order to identify proactive preventative maintenance.
EBCx Qualifications, Skills, Roles, and Responsibilities
Commissioning providers require a unique combination of knowledge on engineering fundamentals and building operations including energy systems design, installation and operation, commissioning planning and process management, hands-on field experience with energy systems performance, system interaction, startup, balancing, testing, troubleshooting, O&M procedures, and BAS controls.
Certification, education, and, most importantly, experience are indicators of qualified providers. Certification as a commissioning provider is one indicator of proficiency. However, depending on the size and complexity of a project, a certification may not be a mandatory requirement. More than likely, an EBCx project will be completed by a combination of in-house staff, O&M contractor, and hired consultants. For smaller or less-complex projects, at least one team member from the facility (in-house), the O&M contractor, or the proposed commissioning provider should have an appropriate certification. For larger or more complex projects, the statement of work (SOW) should specify the expectations for certification or experience on similar projects.
Certified or not, education, professional experience, and examples of past work are key indicators of an individual’s commissioning skills and ability, as well as their appropriateness for a particular commissioning project. Certifications are available from a variety of industry organizations. Relevant to staff selection, either in-house or contracted, it is prudent to request and understand the relevant certifications for all individuals involved. Table 2 highlights some of the more prominent commissioning-related certification organizations. Consider developing an in-house EBCx education and certification training program that includes recommended EBCx skills as illustrated in Table 3.
Table 2. Building commissioning certification organizations.
Commissioning Related Certification | Issuing Organization |
---|---|
Certified Commissioning Authority (CxA) |
AABC Commissioning Group |
Certified Building Commissioning Professional (CBCP) |
Association of Energy Engineers |
Building Commissioning Professional (BCxP) |
American Society of Heating, Refrigerating and Air-Conditioning Engineers (ASHRAE) |
Certified Commissioning Professional (CCP) |
Building Commissioning Association |
Commissioning Process Professional (CxPP) |
National Environmental Balancing Bureau |
EBCx Skills
The skills needed to effectively perform EBCx rely heavily on the disciplines of facility design, O&M, data collection and analysis, economics, and project implementation. Training and a working knowledge in each of these areas are key to a well-rounded EBCx team. Regardless of the team being in-house or contracted, having an ability to require (and verify) certain skill sets are important to an effective EBCx. Table 3 highlights typical skills necessary for operational EBCx (CERL 2018).
Table 3. Typical staff skills for effective EBCx.
Skill Topic | Description | Challenge with Acquisition |
---|---|---|
Heating, ventilation, and air conditioning (HVAC) fundamentals |
Familiarity with how HVAC loads, equipment, and controls operate |
High: This is the broadest skill and requires both physics and field knowledge |
Benchmarking and utility analysis |
Ability to interpret patterns in overall facility performance |
Low: Interval data can be harder to interpret but overall the difficulty is low |
Existing building commissioning (EBCx) scoping |
Ability to identify systems, performance indicators, and opportunities |
Moderate: This is essentially an enhanced energy and water evaluation |
System diagraming |
Comprehensive understanding of system concepts and system configurations diagrams |
Moderate: Field-charting complex piping or air-side networks can be difficult |
Trending |
Understanding facility trend features, supplementing with portable loggers |
Moderate: Launching and reading portable data loggers requires practice |
Functional testing |
Familiarity with testing techniques to quantify or qualify system response |
High: It can be difficult to draft, perform, and manage safe and effective field tests |
Data analysis |
Knowing how to manipulate collected data to interpret facility operation |
High: Can require advanced use of Excel and other data analysis tools |
Energy calculations |
Familiarity with basic HVAC and energy formulas to model system changes |
Moderate: Requires the use of standard techniques and equations of HVAC fundamentals |
Return on investment calculations |
Understanding how to estimate implementation costs and payback |
Low: This should be an established skill for facility and energy management staff |
Implementation |
Knowing execution strategies, coordination, and retesting needed |
Moderate: This is the most critical skill and perhaps hardest to do well |
In an ideal world, all EBCx activities could be performed by in-house staff who hold all relevant certifications and skills needed for the different EBCx phases and tasks. In practice, however, most government agencies, installations, and facilities do not have properly trained staff and/or the capacity to functionally manage all required EBCx activities. When contracting for any phase in the EBCx process, a thorough review of contractor certifications, skills, and past performance is warranted.
EBCx Roles and Responsibilities
The roles and responsibilities (R&Rs) of any EBCx activity will depend on the project’s size, level of complexity, duration, and staffing mix assignments (in house versus contracted). Each EBCx project is different, and the R&Rs should be defined at the outset commensurate with the project delivery activity. As a function of the six EBCx phases, Table 4 and Table 5 provide sample roles for n-house facility staff and contracted staff, respectively.
Table 4. Sample site (in-house) staff existing building commissioning roles and responsibilities.
Site Role | Phase 1: Plan |
Phase 2: Assess |
Phase 3: Investigate |
Phase 4: Implement |
Phase 5: Hand-Off |
Phase 6: On-Going |
---|---|---|---|---|---|---|
Site Energy Manager |
Lead/ |
Lead/ |
Consult |
Consult |
Participate |
Lead |
Site Facility Manager |
Support |
Support |
Lead/ |
Lead/ |
Participate |
Support |
Site Lead Engineer/ |
Support |
Support |
Support |
Lead/ |
Lead/ |
Lead |
Site Building Automation System (BAS) Operator |
Support |
Facilitate |
Support |
Support |
Participate |
Support |
Site Information Technology (IT) Support |
Support |
Consult |
Support |
Support |
Support |
Consult |
Site Safety and Security |
Support |
Support |
Support |
Consult |
Support |
Support |
Table 5. Sample contracted staff existing building commissioning roles and responsibilities.
Site Role |
Phase 1: Planning |
Phase 2: Assess |
Phase 3: Investigate |
Phase 4: Implement |
Phase 5: Handoff |
Phase 6: On-Going |
---|---|---|---|---|---|---|
Contract Existing Building Commissioning (EBCx) Provider |
Lead |
Lead |
Oversee |
Oversee |
Oversee |
Support |
Contract Operations and Maintenance (O&M) Tech/ |
Consult |
Consult |
Consult |
Lead/Consult |
Participate |
Support |
Mech./Elec. Contractor |
Support |
Support |
Lead |
Lead |
Lead |
Support |
Testing, Adjusting, Balancing Contractor |
Support |
Lead |
Support |
Support |
Support |
Support |
Contract Building Automation System (BAS) Programmer |
Support |
Support |
Support |
Support |
Support |
Support |
Equipment Vendors |
Support |
Support |
Support |
Support |
Support |
Support |
Contracting Elements of an EBCx Effort
Developing a request for proposal for EBCx contracted services should incorporate the identified phased tasks in a SOW as one element that meets agency, site, or facility requirements and templates. In some cases, a comprehensive contract that includes all phases may offer advantages (e.g., for a site or agency with little or no in-house personnel). In other cases, it can lead to a disconnect between the owner and contractor resulting in limited oversight. When the EBCx services are predominantly contracted, the contractor takes the lead on most activities and oversees those that they are not directly leading.
As discussed in the Planning Phase section, careful evaluation of in-house staff capabilities and capacity will serve as a guide for determining which subsequent phased tasks will be good candidates to retain in-house or to be contracted out. Refer to the EBCx Qualifications, Skills, Roles and Responsibilities section for information on which criteria to consider and evaluate.
Consideration should be given to performing the Assessment Phase with in-house staff to better meet the intent of EISA 2007 and to drive scope development in subsequent phases, some of which may be contracted. Other phases described as part of the EBCx program, such as Planning and On-Going Commissioning, include tasks that are best practices but are less essential to the success of the overall EBCx effort. When staffing or budget is limited, it is pertinent to focus on the critical tasks in each phase as applicable or desired.
A typical practice is to develop a site-based hybridized approach to maximizes the use of in-house skills to the extent practicable and supplements them with contracted services. One such configuration may have the structure as illustrated in Figure 3 (USACE 2018).
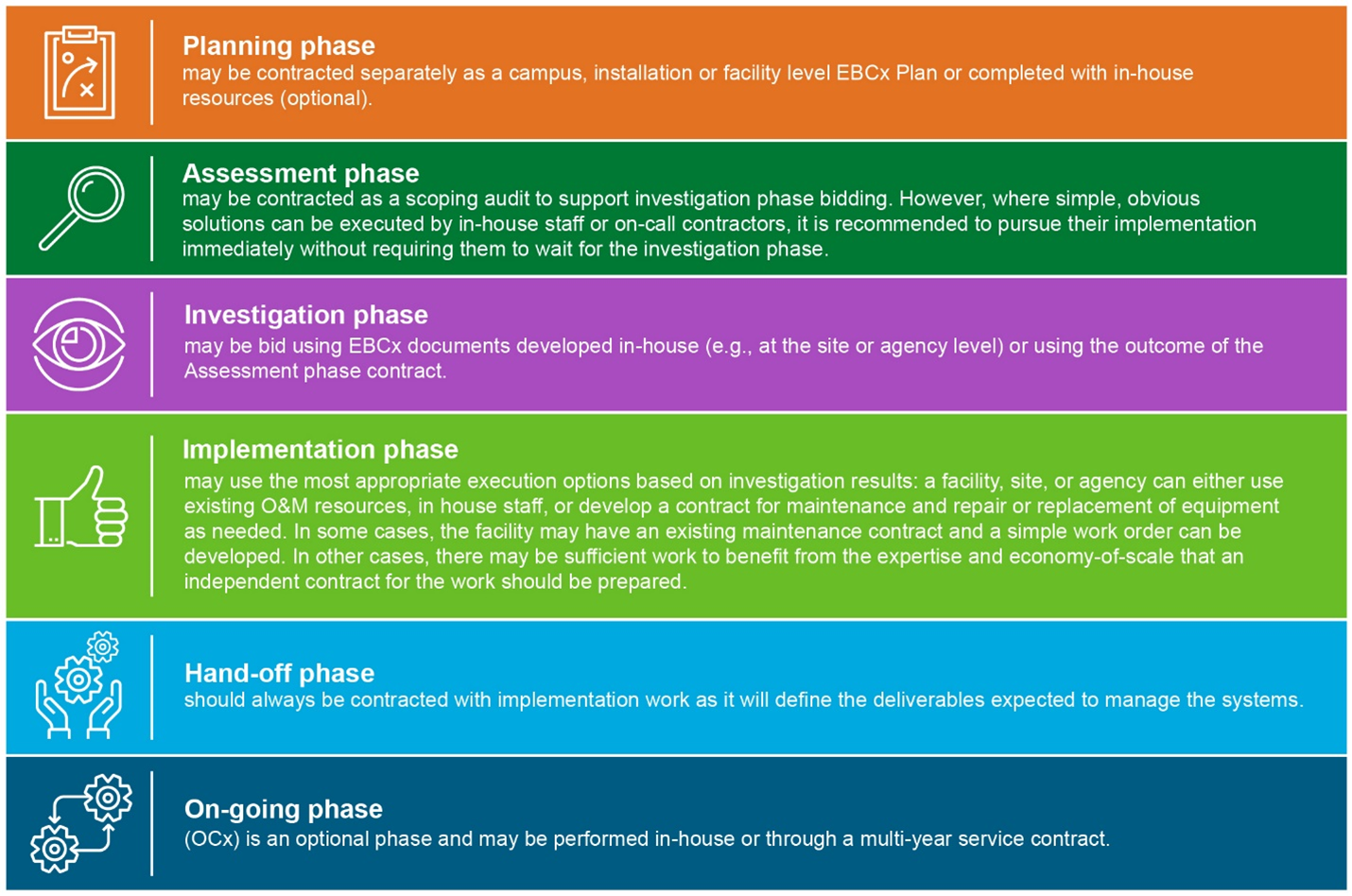
The objective of a phased EBCx process is to capture initial information in each phase as input for the next phase. Adjustments and potential contract modifications may occur as successive phases are executed, and more detailed information is obtained. Regardless of the path chosen (in-house, fully contracted, or a hybrid), a number of factors are critical to the success of EBCx efforts (USACE 2018):
- Clarity. Clearly explain the tasks by phase, systems, and deliverables that are included in your project. Even when working with certified providers, EBCx can mean different things to different individuals and organizations. Spend the time up-front to explain your project, set expectations, answer questions, and gain concurrence on all phases. Use Tables 4 and 5 to delineate R&Rs of each team member. Consider developing regularly scheduled meetings to revisit overall phases, tasks, and deliverables.
- Priority. Focus time and efforts on a predetermined set of priorities. Use energy benchmarking, utility data analysis, and engineering analysis to focus attention on energy, cost, O&M, and comfort drivers. Try not to go into a building blind or to needlessly expand testing and analysis scope to all systems without assessing them first. Consider how these priorities may evolve over the course of the process, allowing opportunity to revisit priorities throughout each phase.
- Comprehensiveness. For facility and systems selected, make sure the level of detail in your EBCx plan is commensurate with the scope and complexity of your goals. Conditions that will affect the comprehensiveness of an EBCx effort include availability of metering or automation data, facility documentation, in-house staffing, and budget. Making sure that the program priorities and comprehensiveness are in alignment will afford a higher probability of success.
- Systems thinking. The facilities and equipment included in the EBCx are connected systems that rely on each other for proper and efficient operation. As such, in the development of the EBCx activities, consider these systems and their interactive effects when planning, analyzing, and implementing ECMs. Develop the metrics, trends, and tests that will deliver the critical data required to make decisions. Consider how ECMs reverberate across systems.
- Coordination. It takes a team of dedicated individuals to prep, access, control, test, analyze, document, perform systems M&V, and track performance during the various phases of any EBCx effort. Coordinate early and keep key stakeholders like O&M technicians, BAS operators, occupant representatives, and information technology personnel informed.
Develop Statement of Work
The SOW development process should include a combination of the logistical and technical materials coupled with the agency, site, or facility standard formats. Highlight contracting element expectations in the areas of contract clarity, priority, comprehensiveness, and coordination. The logistical and technical materials would likely include:
- Project description with detailed technical specifications categorized by EBCx phase, including identified equipment and systems to assess or inspect.
- Expectations of the EBCx team’s qualifications and R&Rs.
- Coordination processes with in-house staff to assist the contractor to be successful through clear communications for each EBCx phase.
- Site or installation furnished information should include utility data, as-builts, CFRs, and previously completed plans or EBCx phases.
- Submissions and reporting requirements categorized by EBCx phase.
- Schedule as detailed as practicable, including major meetings, activities, and milestone deliverables of draft and final plans, submissions, and reports.
- Project completion and Hand-Off plan.
Conclusion
While the process of procuring EBCx services can involve well-defined steps, a practical facility-level implementation will often follow a hybrid system involving the relevant site-specific steps. Important in this implementation is the characterization of existing facilities and an honest assessment of in-house capabilities and capacity. Once a facility’s systems are characterized and in-house skills and availability are determined, a well-defined EBCx procurement path can be initiated.
Additional Resources
Please note that official Energy Act (EA) 2020 guidance is in progress and these recommendations and resources are intended to serve as starting point for compliance with documentation requirements.
Much of the information provided in this Best Practice is based on work done by the U.S. Army Corps of Engineers (USACE) and ASHRAE. Refer to the following documents for more detailed and complete understanding of the EBCx topic:
- Army RCx Technical Guide: A Phased Approach for In-House or Contracted Existing Building Commissioning. https://usace.contentdm.oclc.org/digital/api/collection/p266001coll1/id/6626/download
- Recommissioning (ReCx) Process for EISA Compliance: Guidance and Instructions for Recommissioning Statements of Work Templates. https://www.wbdg.org/files/pdfs/rcx_sow_templates.pdf
- ASHRAE Guideline 0.2-2015, Commissioning Process for Existing Building Systems and Assemblies. https://webstore.ansi.org/standards/ashrae/ashraeguideline2015
Federal Energy Management Program Commissioning Guidance
Commissioning is a quality assurance process used to verify that a building performs according to the original design and intent and meets the needs of the owners and occupants. Federal agencies are required to make sure building systems and equipment are commissioned in new construction and existing buildings.
The Federal Energy Management Program (FEMP) EBCx Decision Tool (PNNL 2022) guides users through the process of identifying the existing building commissioning (EBCx) exceptions, requirements, and approaches to consider for their facilities. https://www.energy.gov/eere/femp/articles/femp-existing-building-commissioning-decision-tool
The following links provide more FEMP developed information on commissioning (Cx), recommissioning (ReCx), retrocommissioning (RCx) and on-going commissioning (OCx)/ monitoring-based commissioning (MBCx):
- https://www.energy.gov/eere/femp/commissioning-federal-buildings
- https://www.energy.gov/eere/femp/articles/commissioning-federal-facilities
- https://www.energy.gov/eere/femp/commissioning-process-federal-facilities
- https://www.wbdg.org/continuing-education/femp-courses/femp01https://www.wbdg.org/continuing-education/femp-courses/femp01
- https://www.energy.gov/sites/default/files/2014/07/f17/commissioning_fed_facilities.pdf
FEMP Re-tuning™
Our researchers have developed a building Re-tuning™ approach to detect energy savings opportunities and implement improvements. To put this methodology into practice, we offer resources for both large (more than 100 KSF) and small (less than 100 KSF) buildings as well as an online interactive training curriculum. The training provides building operators and managers, as well as energy service providers, with the necessary skills to identify and correct no- and low-cost operational problems that plague commercial buildings. The FEMP developed the Re-tuning Candidate Checklist to help agencies screen and prioritize buildings for re-tuning suitability (FEMP 2022).
Find out more at the Building Re-tuning™ Portal: https://buildingretuning.pnnl.gov/
50001 Ready Program
The U.S. Department of Energy (DOE) 50001 Ready Program recognizes facilities and organizations that attest to the implementation of an International Organization for Standardization (ISO) 50001-based energy management system. The program is a self-paced, no-cost plan for organizations to build a culture of structured energy improvement that leads to deeper and sustained savings and does not require any external audits or certifications. The 50001 Ready partners with utilities and other organizations support and facilitate the implementation of 50001 Ready energy management systems. Find out more about the 50001 Ready program at the Better Buildings Solution Center.
Find out more at the 50001 Portal: https://betterbuildingssolutioncenter.energy.gov/iso-50001/50001Ready
FEMP Metering Guidance
The Energy Policy Act of 2005 requires DOE to establish guidelines for agencies to meter their federal buildings for energy (electricity, natural gas, and steam) and water use. To help agencies meet their metering requirements, FEMP provides guidance, templates, best practices, and more.
https://www.energy.gov/eere/femp/metering-federal-buildings
Definitions
- 50001 Ready. Self-guided approach for facilities to establish an energy management system and self-attest to the structure of ISO 50001, a voluntary global standard for energy management systems in industrial, commercial, and institutional facilities. https://www.energy.gov/eere/amo/50001-ready-program
- Current Facility Requirements (CFR). A written document that details the current functional requirements of an existing facility and the expectations of how it should be used and operated. This includes goals, measurable performance criteria, cost considerations, benchmarks, success criteria, and supporting information to meet the requirements of occupants, users, and owners of the facility. https://codes.iccsafe.org/s/ICCG42018/chapter-2-definitions/ICCG42018-Ch02-Sec2.3
- Existing Building Commissioning (EBCx). Commissioning of an existing building (typically) using a recognized approach such as recommissioning, retro-commissioning, on-going commissioning (i.e., monitoring-based commissioning), Re-tuning™, and more. Refer to FEMP’s EBCx Decision Tool (PNNL 2002) guides agencies through the process of identifying the EBCx requirements, exceptions, and approaches to consider for their facilities. https://www.energy.gov/eere/femp/articles/femp-existing-building-commissioning-decision-tool
- Re-tuning™. A systematic process to minimize energy consumption by identifying and correcting operational no-cost or low-cost measures. Re-tuning™ relies on building automation system (BAS) data to identify and implement control improvements at no cost other than the time to program the changes. These low/no-cost operational measures ultimately improve the buildings’ energy efficiency, reduce operating costs, and improve occupant comfort. The Re-tuning™ methodology is based on two basic principles: (1) if equipment is not needed, turn it off; (2) if equipment is not needed at full power, turn it down. Re-tuning™ can be applied to any building size, with the data-driven approach applying to larger buildings with a BAS (e.g., greater than 50 [thousand square feet] KSF). The Re-tuning™ methodology can also be applied to small buildings (less than 50 KSF) that lack a BAS; however, the process becomes more prescriptive. https://www.energy.gov/eere/femp/re-tuning-federal-buildings
The following definitions are taken directly from EA 2020, Section 42 U.S.C 8253(f)(3)(A)
- Commissioning (Cx). (A) The term “commissioning”, with respect to a facility, means a systematic process —
- ii. of ensuring, using appropriate verification and documentation, during the period beginning on the initial day of the design phase of the facility and ending not earlier than 1 year after the date of completion of construction of the facility, that all facility systems perform interactively in accordance with - the design documentation and intent of the facility; and the operational needs of the owner of the facility, including preparation of operation personnel; and
- iii. the primary goal of which is to ensure fully functional systems that can be properly operated and maintained during the useful life of the facility.
- Ongoing Commissioning (OCx).(E) The term “Ongoing Commissioning” means an ongoing process of commissioning using monitored data, the primary goal of which is to ensure continuous optimum performance of a facility, in accordance with design or operating needs, over the useful life of the facility, while meeting facility occupancy requirements.
- Recommissioning (ReCx): (G) Recommissioning means a process —
- i. of commissioning a facility or system beyond the project development and warranty phases of the facility or system; and
- ii. the primary goal of which is to ensure optimum performance of a facility, in accordance with design or current operating needs, over the useful life of the facility, while meeting building occupancy requirements.
- Retrocommissioning (RCx): (H) Retrocommissioning means
- … a process of commissioning a facility or system that was not commissioned at the time of construction of the facility or system.
References
42 U.S.C. 8201 et seq. National Energy Conservation Policy Act. Public Law 95-619, as amended. https://www.govinfo.gov/content/pkg/COMPS-10424/pdf/COMPS-10424.pdf
42 U.S.C. 17001 et seq. 2007. Energy Independence and Security Act. Public Law 110-140, as amended. https://www.govinfo.gov/content/pkg/PLAW-110publ140/pdf/PLAW-110publ140.pdf
42 U.S.C. 8253 et seq. Energy Act of 2020. U.S. Code, as amended.
ASHRAE. 2014. The Strategic Guide to Commissioning. Report from the ASHRAE Presidential Ad-Hoc Committee Building Performance Alliance on Commissioning. American Society of Heating, Refrigerating, and Air-Conditioning Engineers, Peachtree Corners, GA. https://www.ashrae.org/File%20Library/Technical%20Resources/Bookstore/ENGLISH-ASHRAE_BPA-Brochure_FNL_6-24-14.pdf
ASHRAE Guideline 0.2-2015. The Commissioning Process for Existing Systems and Assemblies. American Society of Heating, Refrigerating, and Air-Conditioning Engineers, Peachtree Corners, GA. https://webstore.ansi.org/standards/ashrae/ashraeguideline2015
BCA. 2008. Best Practices in Commissioning Existing Buildings. Building Commissioning Association, Beaverton, OR. https://cdn2.hubspot.net/hubfs/416421/pdf/bca-ebcx-best-practices.pdf
CERL. 2008. Army RCx Technical Guide. Construction Engineering Research Laboratory, Champaign, IL. https://usace.contentdm.oclc.org/digital/api/collection/p266001coll1/id/6626/download
DOE. 2008. Facility Energy Management Guidelines and Criteria for Energy and Water Evaluations in Covered Facilities (42 U.S.C. 8253 Subsection (f), Use of Energy and Water Efficiency Measures in Federal Buildings). Department of Energy, Washington, D.C. https://www.energy.gov/sites/default/files/2013/10/f3/eisa_s432_guidelines.pdf
EO 14057. “Catalyzing Clean Energy Industries and Jobs Through Federal Sustainability.” 86 FR 70935, Federal Register, Vol. 86, No. 236, December 13, 2021. https://www.govinfo.gov/content/pkg/FR-2021-12-13/pdf/2021-27114.pdf
FEMP. 2022. Energy and Project Procurement Development Services. Federal Energy Management Program, Washington, D.C. https://www.energy.gov/eere/femp/energy-and-project-procurement-development-services
NREL. 2017. Retrocommissioning Evaluation Protocol — The Uniform Methods Project: Methods for Determining Energy Efficiency Savings for Specific Measures. National Renewable Energy Laboratory, Golden, CO. https://www.nrel.gov/docs/fy17osti/68572.pdf
NREL. 2022. Best Practices for Enhancing Performance Contracts with Monitoring-Based Commissioning. National Renewable Energy Laboratory, Golden, CO. https://www.nrel.gov/docs/fy22osti/81742.pdf
PNNL. 2016. Building Re-Tuning Training: Providing Energy Saving Solutions through Interactive e-Learning. Pacific Northwest National Laboratory, Richland, WA. https://buildingretuning.pnnl.gov/documents/pnnl_sa_83943.pdf
PNNL. 2022. Re-tuning Candidate Checklist. Federal Energy Management Program, Washington, D.C. https://www.energy.gov/eere/femp/articles/re-tuning-candidate-checklist
PNNL. 2022. Existing Building Commissioning Decision Tool. PNNL-SA-167772. Federal Energy Management Program, Washington, D.C. https://www.energy.gov/eere/femp/articles/femp-existing-building-commissioning-decision-tool
USACE. 2018. Army RCx Technical Guide. U.S. Army Corps of Engineers, Washington, D.C. https://usace.contentdm.oclc.org/digital/api/collection/p266001coll1/id/6626/download