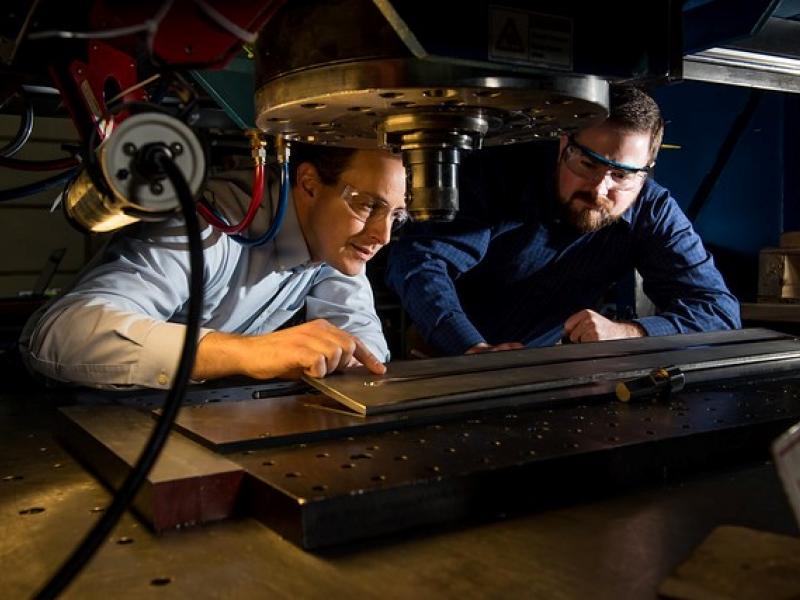
Materials Science
for Hydropower
Materials Science
for Hydropower
Providing innovative technologies
to improve hydropower performance
Providing innovative technologies
to improve hydropower performance
At hydropower plants, large turbines made of steel weigh as much as 172 tons and turn at a rate of 90 revolutions per minute.
These metal giants are designed to operate for decades, but the stainless-steel alloys of turbine runners often become corroded or cavitated from being submerged in water. Corrosion and cavitation affect other metal components of both small and large hydropower facilities, such as intakes, wicket gates, and spillways. The hydropower industry is also impacted by biofouling—the growth of invasive species like zebra mussels on turbines and other structures from accumulated bacteria.
Materials science can play an important role in hydropower by improving overall system performance and lowering costs associated with turbine repairs. Innovative technologies enhance hydropower’s capability to provide efficient grid services to the nation.
PNNL has led research for the U.S. Department of Energy’s Water Power Technologies Office to explore the potential of Solid Phase Processing (SPP) to enhance the performance and life of new and repaired hydropower components. SPP can improve hydropower capabilities, resilience, and efficiency, benefiting hydropower owners and operators, power regulators, and the economy.
PNNL also has developed materials to deter zebra mussels from attaching to hydropower structures, which causes operational interferences at facilities. These mussels create biofouling challenges at hydropower facilities, specifically related to maintenance and operations. Biofouling is the multi-phase process where collections of microorganisms grow on a surface and create bacteria.
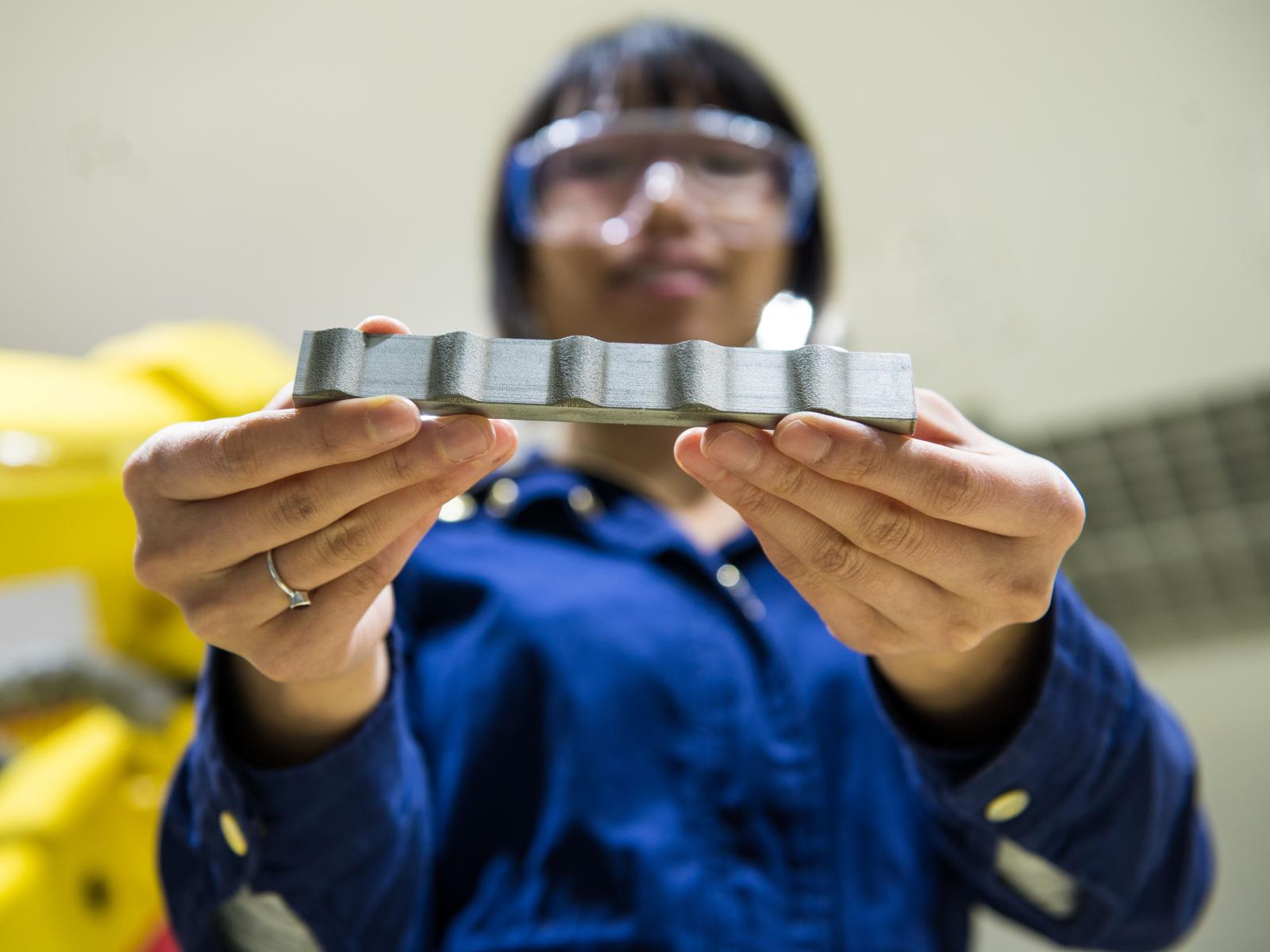
Cold spray and friction stir processing
PNNL has two SPP capabilities to help address these hydropower needs: cold spray and friction stir processing. PNNL’s SPP technologies pair next-generation materials with efficient manufacturing approaches to lower the operation and maintenance costs of dams, reduce the duration and frequency of outages, and extend the life of hydraulic structures.
The goal of the cold spray technique—a research project which is currently underway—is to tackle cavitation damage to turbine blades and improve the performance and service life of repaired turbines. Cold spray techniques may dramatically reduce the frequency of dam outages and costs associated with dam maintenance.
The portable system works by shooting metal particles at high speeds into damaged areas. The result is a solid-state weld between the particle and the turbine surface. And unlike other welding repair techniques that cause material degradation, cold spray keeps turbine blades in their original shape. The repaired metal can exceed the strength of the original metal.
Friction stir processing is another type of welding technology that eliminates the use of adhesives, bolts, and rivets. The PNNL-developed technology enables welding of materials that are generally unweldable. Friction stir processes allow metals with different melting temperatures and chemically different materials to be joined.
The technology may be used to embed sensors into turbines to monitor difficult to observe environments. Additionally, the life of hydropower components could be extended with the use of less expensive base materials and could be welded onto harder materials in damaged or high wear areas.
SPP research is conducted at the Applied Process Engineering Laboratory.
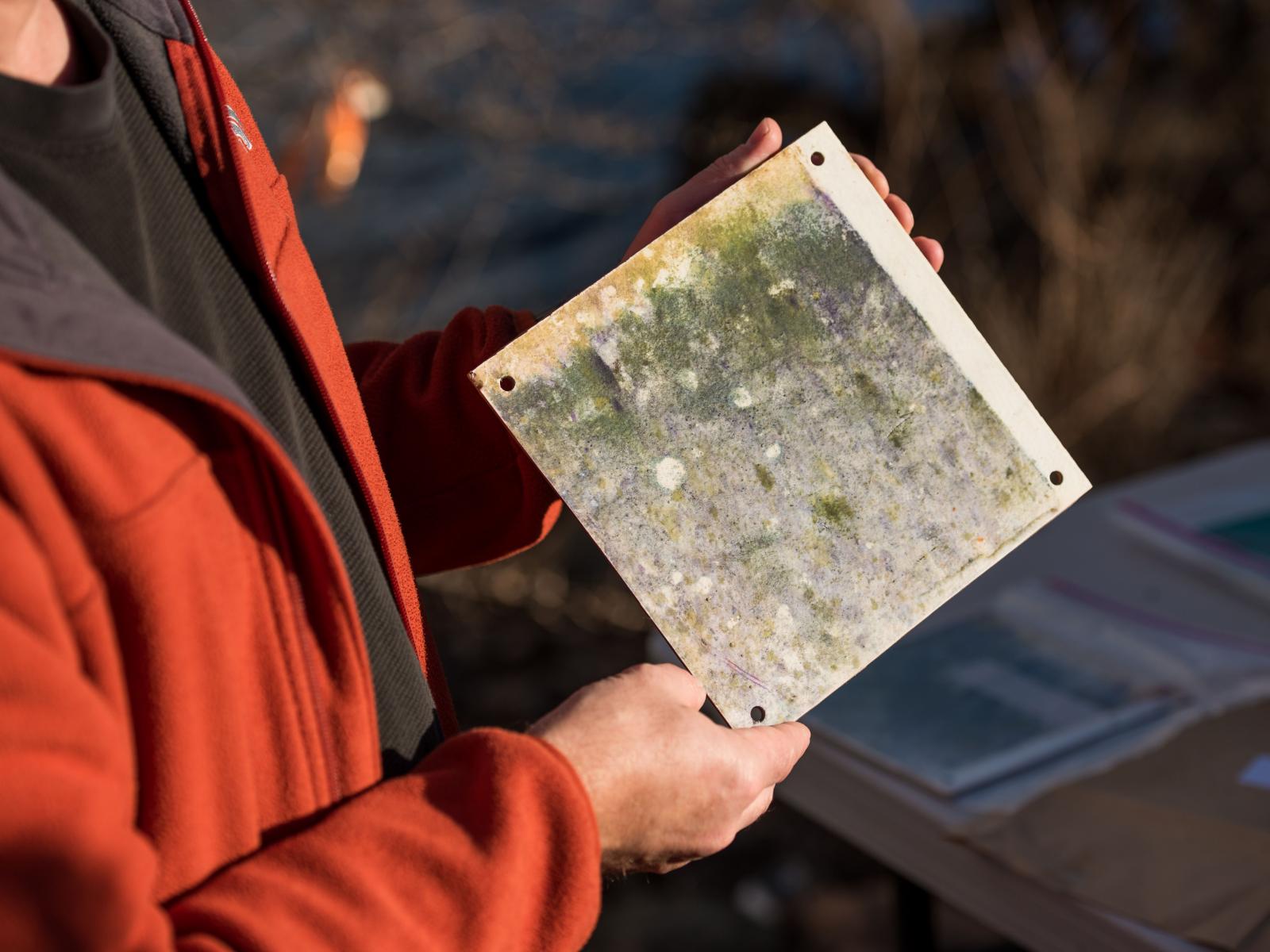
Biofouling prevention
Scientists at PNNL developed an innovative coating that improves hydropower operations and can reduce plant shutdowns to remove zebra mussels. Superhydrophobic Lubricant Infused Composite (SLIC) prevents mussels from attaching to hydropower structures. SLIC is an environmentally friendly coating that can be adjusted to the water conditions commonly found at hydropower facilities. SLIC was developed in support of the Water Power Technologies Office and in partnership with the U.S. Bureau of Reclamation, U.S. Army Corps of Engineers, and BioBlend Renewable Resources.