- Best Practices for Equipment O&M
-
O&M Best Practice Issue Discussions
- Advanced Maintenance Approach: Reliability Centered Maintenance
- Applying Key Performance Indicators
- Comprehensive O&M Program
- Contract Challenges and Improvements
- Cybersecurity for O&M Systems
- Existing Building Commissioning Procurement
- Healthy Building O&M
- Integrating and Analyzing Building Information to Support O&M
- Maintenance Approaches
- OMETA: An Integrated Approach to Operations, Maintenance, Engineering, Training, and Administration
- Prioritizing O&M Actions
- Re-tuning Buildings
- Tools
- Glossary
Unitary HVAC Equipment
Best Practices for Unitary HVAC Equipment Operation and Maintenance
Table of Contents
- Introduction
- Description of Technology
- Key Components
- Safety Issues
- Maintenance of Technology
- Maintenance Checklist
- Performance Monitoring
- O&M Cost
- Additional Support
- Sources of Information
Introduction
Unitary heating, ventilation, and air conditioning (HVAC) systems, which combine heating and cooling in one unit (packaged) or a few sections (split), are one of the most common technologies used for space conditioning in commercial buildings. They are designed to be flexible so that the equipment can be installed indoors (in a mechanical room, attics, ceilings, etc.) or outdoors (on rooftops or on the ground). Effective operations and maintenance (O&M) of these systems is necessary to maximize efficiency and production, provide occupancy comfort, and reduce failures.
The purpose of this equipment O&M Best Practice is to provide an overview of unitary HVAC equipment, maintenance requirements, and best practices necessary to operate the systems safely and efficiently. Support organizations should budget and plan for regular maintenance to assure continuous operation.
Description of Technology
Unitary HVAC equipment can provide cooling or heating only, or both cooling and heating. Cooling is most often supplied by a direct expansion (DX) system, while heating can be provided by several system types, including gas (natural or propane), electric resistance, and heat pump (air-to-air).[1]
All components can be contained in one cabinet (e.g., rooftop unit as shown in Figure 1) or they can be housed in two cabinets (e.g., split systems as shown in Figure 2). The indoor unit of a split system contains the space conditioning and air movement components, and the outdoor unit houses the heat-rejection devices.
Some features of unitary HVAC systems include:
- Smaller equipment footprint than central air handlers, chillers, and boilers.
- Ability to locate units outdoors, which reduces indoor mechanical space requirements but introduces possible vulnerability to severe weather conditions, vandalism, and other factors that must be considered.
- Ability to locate units in smaller indoor spaces (attics, ceilings, etc.) or on rooftops; service accessibility must be considered. key Components
The key elements of unitary HVAC systems depend on whether cooling or heating only or both cooling and heating are provided. There are several types of heating systems available with unitary equipment. This section describes the key components of the most commonly used technologies. Figure 1 and Figure 2 illustrate the standard components of unitary HVAC equipment.
[1] This Best Practice does not address hydronic components in unitary systems.
Key Components
The key elements of unitary HVAC systems depend on whether cooling or heating only or both cooling and heating are provided. There are several types of heating systems available with unitary equipment. This section describes the key components of the most commonly used technologies. Figure 1 and Figure 2 illustrate the standard components of unitary HVAC equipment.
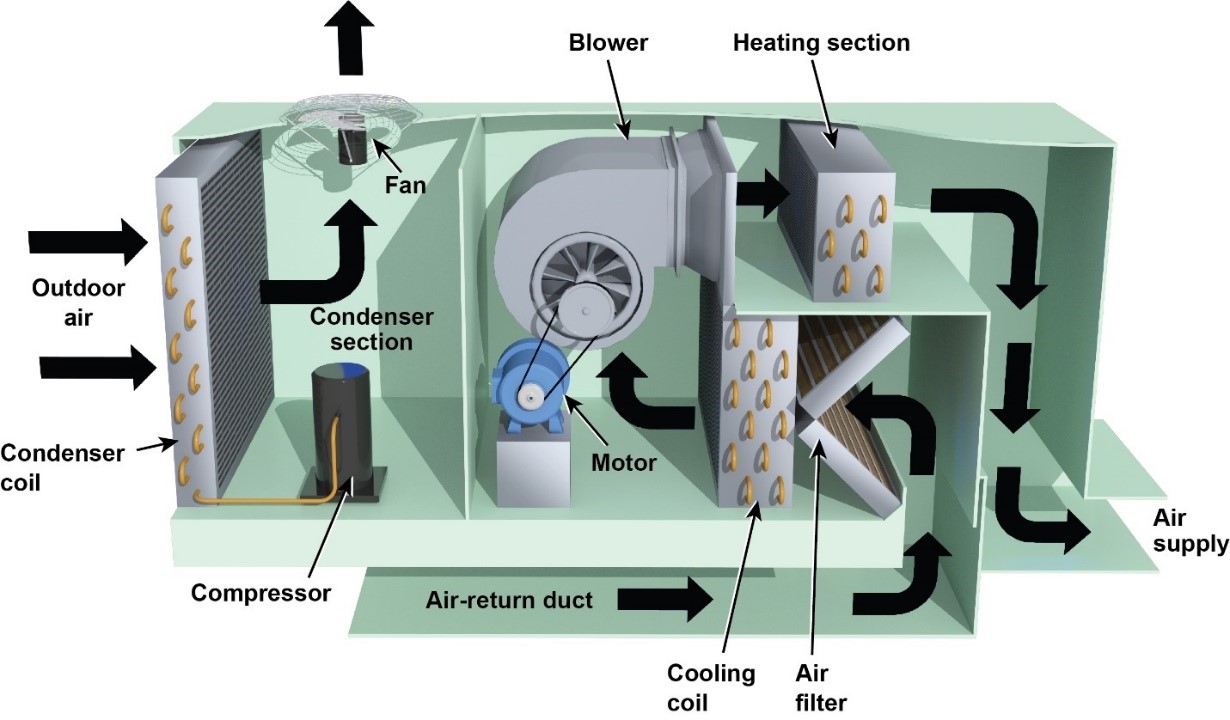
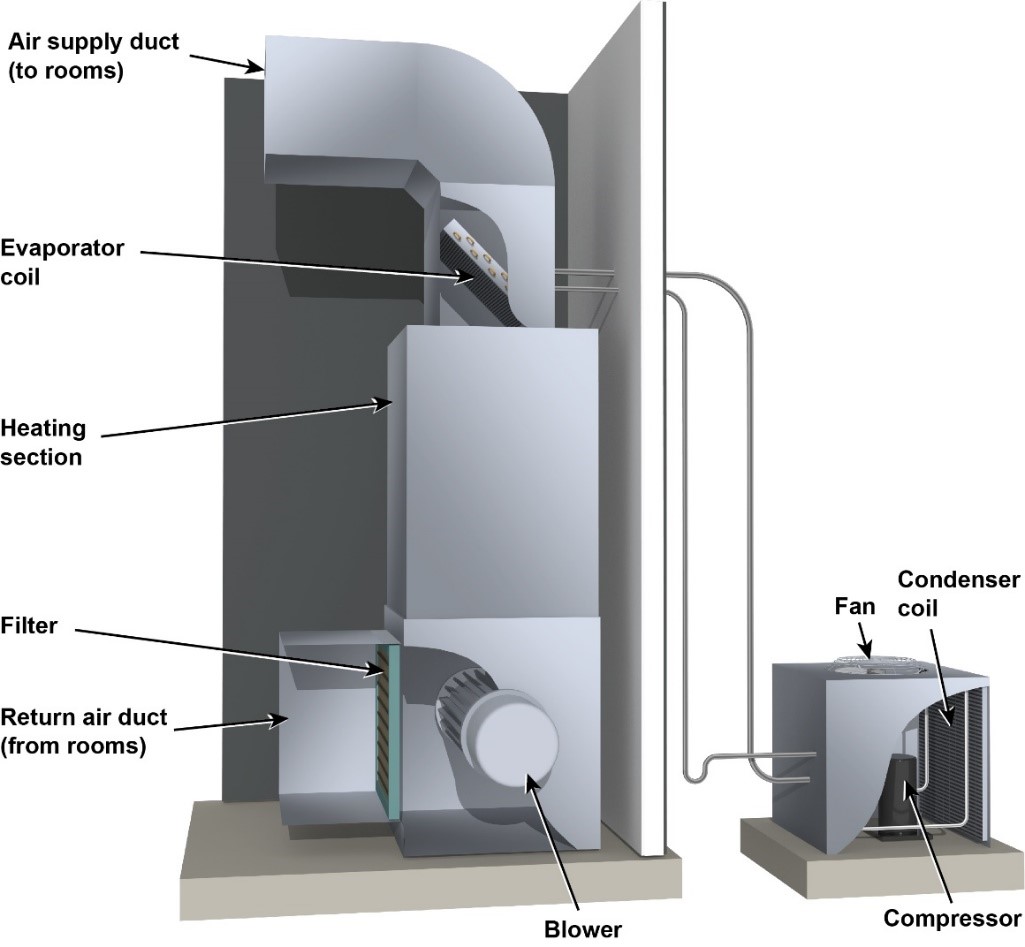
Direct Expansion Refrigerant System (DX System)
The DX system consists of the following components:
- Compressor – converts a cool, low-pressure refrigerant gas into a hot, high-pressure gas.
- Condenser coil – finned tube coil cools the refrigerant by transferring heat from the refrigerant to the outside air.
- Evaporator coil – finned tube coil provides space cooling and dehumidification by transferring heat from the air to the refrigerant.
- Thermostatic expansion valve – regulates the flow of refrigerant into the evaporator coil.
- Refrigerant – a chemical compound heat transfer medium that absorbs, transports, and releases the heat energy in the DX system.
-
Refrigerant lines – the copper piping that carries refrigerant to the various components of the DX system.
Heating System
The furnace section is the housing that contains the heating equipment.
A gas-fired heating system generally consists of the following components:
- Burner – uses a small flame to create a heat source by mixing gas and air in the combustion chamber.
- Heat exchanger – transfers heat from the combustion chamber to the unit’s airstream, providing heat to the supply air.
- Gas valve – controls the flow of gas to the heat exchanger.
- Ignition – modern furnaces use a hot surface ignitor (HSI) that glows red and ignites the gas when it comes on.
- Flame sensor – a safety device that is used to detect when HSI is used; shuts off the gas if heat is not detected.
- Flue/vent pipe – metal pipe for removal of the byproducts produced during the combustion process.
An electric heating system generally consists of the following components:
- Electric heater elements – resistance wire open-coil construction heat source.
- Heater controls – energize the elements to provide heat.
- Safety devices – including airflow switch and over-temperature protection to de-energize the heater when unsafe operating conditions are detected.
Air-to-air heat pumps have the same components as a DX system with the addition of the following devices:
- Reversing valve – changes the refrigerant flow direction to provide heating; as a result, the condenser coil acquires heat from outside air, and heat is provided to the interior space using the evaporator coil.
- Accumulator – a reservoir that prevents liquid refrigerant from entering the compressor.
Air Distribution
The following key components play an important role in providing conditioned air to the building (some of these components are shown in Figure 1 and Figure 2):
- Blower assembly – a fan with motor that supplies conditioned air. (Note: fan can be constant speed or variable speed.)
- Variable speed drive (if applicable) – a controller that varies the speed of an electric motor by varying the frequency and voltage supplied.
- Damper – controls the flow of air.
- Ductwork – conduit used to move air throughout the facility; it is typically composed of sheet metal. (Note: Ductless unitary HVAC systems are used for certain applications.)
- Air filter – removes particulate matter from an airstream.
Control System
The control system provides the ability to operate the equipment to maintain desired setpoints. Three common systems are:
- Space thermostat – a stand-alone or integrated device that can be either programmed or set manually to keep the space at a desired temperature; the thermostat triggers a unit to begin circulating heated or cooled air as needed.
- Unit controller – a device that is used to operate a unit as specified and that can provide diagnostic information. A unit controller can either be stand-alone or integrated with a building automation system (BAS).
- BAS – a direct digital control system that can be used to monitor and control multiple HVAC units; the system is accessible locally and/or remotely.
Safety Issues
HVAC equipment requires knowledgeable and experienced personnel for maintenance, diagnostics, and any additional troubleshooting work. Standard electrical, mechanical, and other safety practices apply to these systems.
Refrigerant must be handled properly and in compliance with regulations, and agency policies should be consulted for refrigerant management requirements. Proper handling includes recovery, recycling, and reclaiming. Refrigerant oils are to be treated as hazardous waste. Follow all safety procedures described in the Material Safety Data Sheet for the refrigerant and all labels on refrigerant containers. If materials containing refrigerants are discarded, disposal requires compliance with regulations.
For units with gas heating, assure that all safety procedures are followed. Fire or explosion may be caused by undetected gas leaks that can pose grave danger. Confirm that gas is shut off before doing any maintenance or troubleshooting work.
Maintenance of Technology
Adopting a preventive maintenance program is critical to assuring that the system functions properly and efficiently. Keeping the HVAC equipment properly maintained through preventive maintenance will minimize overall O&M costs by reducing costly repairs and unexpected downtime, improve system performance, increase the operating life, and protect the asset.
Typically, a trained and authorized HVAC professional performs the required equipment repairs. However, facility maintenance personnel and other approved on-site representatives can perform visual inspections and other routine checks, as well as document system issues. It is important to keep a written log, preferably in electronic form in a Computer Maintenance Management System, of all services performed. This record should include findings from functions and diagnostics performed, corrective actions taken, equipment downtime, and other relevant issues noted. This will help identify recurring issues or systemic problems.
Equipment should be included under a periodic evaluation process with prioritization and consideration given to equipment life, repair and maintenance history, and criticality of system operation.
In cases where the unitary HVAC equipment supports critical systems or buildings, consider additional monitoring of the equipment performance to identify pending performance and condition degradation and even the onset of failure. Also, identify and stock the site’s parts inventory with the spare parts and components necessary to assure this equipment can be repaired in a timely manner when needed.
Maintenance Checklist
For all equipment maintenance, follow the manufacturer’s instructions. A sample maintenance checklist is below. A site staff member or contractor can be designated to perform the following tasks, but repairs should be performed by a trained and authorized HVAC maintenance provider. This checklist does not supersede maintenance recommendations from the equipment manufacturers, nor is it a replacement for contracted O&M or warranty services.
Below is a sample checklist (Table 1). Consult the manufacturer’s information for acceptable operating parameters.
Table 1. Sample maintenance checklist for unitary HVAC equipment.
Description |
Action |
Maintenance Frequency |
|||
Daily |
Weekly |
Quarterly |
Annually |
||
Inspection |
Perform overall visual inspection to be sure all equipment is operating and safety systems are in place |
X |
|
|
|
Inspect all units for excessive vibration and noise |
X |
|
|
|
|
Inspect outdoor air intakes and other exterior openings for possible obstructions |
|
X |
|
|
|
Inspect equipment installed outdoors for possible damage from weather conditions, vandalism, etc. |
|
X |
|
|
|
Inspect all roof and wall penetrations for integrity |
|
|
X |
|
|
Air Supply and Quality |
Check supply air temperature to assure proper operation |
|
|
X |
|
Inspect for moisture and mold growth; check for musty smells and listen to complaints |
|
|
X |
|
|
Equipment Controls |
Check and adjust thermostat; recalibrate if needed |
|
|
X |
|
Check unit controller; adjust setpoints if needed and address any issues |
|
|
X |
|
|
Check building control system for monitoring and control; adjust setpoints if needed (applicable to sites with a BAS) |
|
|
X |
|
|
Filters |
Check filter condition according to system type and manufacturer’s recommendations; replace (or clean if re-usable type) dirty filter as needed |
|
|
X |
|
Dampers and Actuators |
Check dampers; clean if required |
|
|
X |
|
Inspect damper actuators and linkages for proper operation by cycling from fully opened to fully closed; adjust linkages as necessary |
|
|
X |
|
|
Clean, lubricate, and adjust as needed |
|
|
X |
|
|
Ductwork |
Inspect ductwork for integrity; check for leakage due to major connections and access doors not being properly closed |
|
|
X |
|
Inspect, repair, and replace all compromised duct insulation |
|
|
X |
|
|
Fans and Motors (Evaporator and Condenser) |
Check fans and cabinet interiors; clean if required |
|
|
X |
|
If belt-driven, check for wear, tension, and misalignment. Adjust and replace as necessary |
|
|
X |
|
|
Lubricate fans and motor bearings, if provided, and only as required |
|
|
X |
|
|
Check variable speed drives for proper operation (if applicable) |
|
|
X |
|
|
Check fans for bent blades or imbalance; correct as required |
|
|
|
X |
|
Check motor condition and verify proper operation |
|
|
|
X |
|
Coils |
Inspect coil, straighten fins, and clean as needed |
|
|
X |
|
Condensate |
Check the drain and pan; flush and treat with anti-algae as needed |
|
|
X |
|
Electric Heating |
Check to make sure the electric heat only energizes when there is airflow |
|
|
X |
|
Check the temperature rise and supply air temperature |
|
|
X |
|
|
Gas Heating |
Check the flue/vent pipe for rust and corrosion |
|
|
X |
|
Inspect flue/vent pipe and draft inducer motor for proper operation |
|
|
X |
|
|
Test ignition system for safe and proper operation |
|
|
X |
|
|
Clean furnace burner and heat exchanger; brush and vacuum if necessary |
|
|
X |
|
|
Check heat exchanger for cracks, rust, and soot |
|
|
X |
|
|
Check gas manifold pressure; adjust for peak efficiency if necessary |
|
|
X |
|
|
Check gas piping and gas valve for integrity |
|
|
X |
|
|
Check draft and analyze combustion |
|
|
X |
|
|
Test safety shut-off response |
|
|
X |
|
|
Heat Pump Operation |
Confirm that the unit is properly operating in cooling and heating mode |
|
|
X |
|
Assure that the reversing valve is properly operating |
|
|
X |
|
|
Dual fuel systems: Assure that the equipment is properly programmed for optimized heating |
|
|
|
X |
|
Compressor |
Inspect compressor and check all alignments and seals |
|
|
|
X |
Check amperage draw |
|
|
|
X |
|
Check crankcase heater(s) |
|
|
|
X |
|
Refrigerant |
Inspect refrigerant lines and address leakage issues; add refrigerant as required |
|
|
|
X |
Wiring |
Verify all electrical connections are tight |
|
|
|
X |
Motor Condition |
Check the condition of the motor through temperature or vibration analysis |
|
|
|
X |
Power Balance |
Check for balanced three-phase power |
|
|
|
X |
Voltage Conditions |
Check for over-voltage or under-voltage conditions |
|
|
|
X |
BAS (if applicable) |
Perform re-tuning using BAS |
|
|
|
X |
System Documentation |
Document all maintenance activities in a logbook or electronic CMMS |
Upon activity completion |
Performance Monitoring
Monitoring unitary HVAC systems is important to assure proper operation. In other words, confirm that components are working as they should and that equipment is responding properly to controls. Note that discomfort, complaints, and noise can be indicators of performance issues. In cases where monitoring and evaluating the performance of an HVAC system is needed, collecting data typically requires measuring devices, tools, and/or BAS software.
O&M Cost
Unitary HVAC equipment requires preventive maintenance as well as other periodic checks. The O&M costs vary significantly depending on the type of equipment, maintenance plan, the scope of work involved, and geographical location. The American Society of Heating, Refrigerating and Air-Conditioning Engineers (ASHRAE) offers a web-based public database with current information on service life and maintenance costs of typical HVAC equipment. (https://xp20.ashrae.org/publicdatabase/default.asp)
Additional Support
To encourage quality O&M, building engineers can refer to ASHRAE/ACCA Standard 180: Standard Practice for Inspection and Maintenance of Commercial Building HVAC Systems. https://www.ashrae.org/technical-resources/bookstore/standards-180-and-211
Sources of Information
ASHRAE Owning and Operating Cost Database. ASHRAE: Service Life and Maintenance Cost Database. American Society of Heating, Refrigerating and Air-Conditioning Engineers, Atlanta, GA. https://xp20.ashrae.org/publicdatabase/
Better Buildings Alliance. 2014. Fact Sheet: Rooftop Unit Measurement and Verification. U.S. Department of Energy, Better Buildings, Washington, D.C. https://betterbuildingssolutioncenter.energy.gov/sites/default/files/attachments/RTU_MandV_Fact_Sheet.pdf
CERTs (Clean Energy Resource Teams). Preventative Maintenance for Heating, Cooling and Refrigeration Systems. Clean Energy Resource Teams, St. Paul, MN. https://www.cleanenergyresourceteams.org/sites/default/files/FSELP_PreventativeMaintenance.pdf
EERE (DOE Office of Energy Efficiency & Renewable Energy). Energy Saver - Central Air Conditioning. U.S. Department of Energy, Office of Energy Efficiency and Renewable Energy, Washington, D.C. https://www.energy.gov/energysaver/central-air-conditioning
FEMP (Federal Energy Management Program). 2010. Operations & Maintenance Best Practices: A Guide to Achieving Operational Efficiency. Release 3.0., Chapter 9, O&M Ideas for Major Equipment Types, section 9.7, Air Handling Systems. Prepared by Pacific Northwest National Laboratory for FEMP, Richland, WA. https://www.wbdg.org/FFC/DOE/DOECRIT/femp_omguide.pdf
Actions and activities recommended in this Best Practice should only be attempted by trained and certified personnel. If such personnel are not available, the actions recommended here should not be initiated.
Published December 2020