- Best Practices for Equipment O&M
-
O&M Best Practice Issue Discussions
- Advanced Maintenance Approach: Reliability Centered Maintenance
- Applying Key Performance Indicators
- Comprehensive O&M Program
- Contract Challenges and Improvements
- Cybersecurity for O&M Systems
- Existing Building Commissioning Procurement
- Healthy Building O&M
- Integrating and Analyzing Building Information to Support O&M
- Maintenance Approaches
- OMETA: An Integrated Approach to Operations, Maintenance, Engineering, Training, and Administration
- Prioritizing O&M Actions
- Re-tuning Buildings
- Tools
- Glossary
Comprehensive O&M Program
Table of Contents
- Introduction
- Definitions
- Discussion
- Solutions and Actions
- Conclusion and Next Steps
- Additional Resources
- References
Introduction
Operations and maintenance (O&M) is often thought of as an individual action, such as replacing an air filter or adjusting equipment schedules. However, to be effective, O&M needs to be addressed in a comprehensive and integrated manner that completes a series of functions and activities with the primary purposes of:
- Operating all systems in a safe and efficient manner,
- Achieving/extending the system and equipment’s expected life, and
- Providing equipment and system availability and operability to meet user needs.
We recognize many of the actions and outcomes associated with O&M that are being performed in our buildings to meet our needs, including (but not limited to) heating and cooling building spaces during working hours; replacing burned-out lamps to restore lighting levels; addressing water leaks and clogs to keep restrooms operational; testing standby generators regularly to ensure an ongoing supply of electricity during electrical outages; and continually operating renewable energy systems in a transparent manner to provide clean and sustainable energy to our sites.
In the bigger picture, a comprehensive O&M program works to support successful, broader operational target outcomes at the site and agency levels. These often include:
- Meeting mission requirements,
- Preserving asset value (and reducing capital investment requirements),
- Realizing energy and water efficiency,
- Improving resilience,
- Achieving safe operations, and
- Operating healthy buildings.
Behind these outcomes, both visible and strategic, is a comprehensive O&M program. This O&M Best Practice identifies and describes the key components of such a program. In general, O&M requirements vary by site depending on factors such as the building square footage, mission, and criticality of the buildings and systems, age of the buildings and systems, and complexity of energy and water generation, distribution, and end-use equipment and systems. This means the level of effort and investment required to provide comprehensive O&M will vary by site and even by building. Identifying and executing the appropriate level of O&M approaches and strategies is needed to align the O&M program with the site or agency’s operational target outcomes.
Definitions
- 50001 Ready. Self-guided approach for facilities to establish an energy management system and self-attest to the structure of ISO 50001, a voluntary global standard for energy management systems in industrial, commercial, and institutional facilities. https://www.energy.gov/eere/amo/50001-ready-program
- Asset. A maintenance term commonly taken to mean any item of the physical plant or equipment.
- Computerized Maintenance Management System. While the functionality of Computerized Maintenance Management Systems varies across the industry, these products typically include a system for tracking work orders, scheduling maintenance tasks, and analyzing maintenance activities to better understand failure rates and maintenance costs. [FEMP KPI]
- Corrective Maintenance. Any maintenance activity that is needed to correct a failure that has occurred or is in the process of occurring. This activity may consist of repair, restoration, or replacement of components. (NE SpinTech 2018)
- Existing Building Commissioning (EBCx). Commissioning of an existing building (typically) using a recognized approach such as recommissioning, retro-commissioning, ongoing commissioning (i.e., monitoring-based commissioning), re-tuning, and more.
- Healthy Buildings. There is no consensus on the definition of a healthy building. In general, a healthy building is one that does not inflict or provoke medical issues such as sick building syndrome, allergies, asthma, or heat exhaustion and goes beyond that to promote and optimize occupants’ productivity, performance, and satisfaction. [FEMP Healthy Buildings]
- Key Performance Indicators (KPIs). A select number of key measures that enable performance against targets to be monitored. (NE SpinTech 2018)
- Predictive Maintenance. An equipment maintenance strategy based on measuring the condition of equipment in order to assess whether it will fail during some future period and then taking appropriate action to avoid the consequences of that failure. (NE SpinTech 2018)
- Preventive Maintenance. An equipment maintenance strategy based on replacing, overhauling, or remanufacturing an item at a fixed interval, regardless of its condition at the time; also known as scheduled maintenance. (NE SpinTech 2018)
- Proactive Maintenance. Any tasks used to predict or prevent equipment failures. (NE SpinTech 2018)
- Reactive Maintenance. The work required to restore a component to a condition substantially equivalent to its originally intended and designed capacity, efficiency, or capability (NASA 2000). Reactive maintenance is also known as corrective maintenance, and a reactive maintenance strategy is also known as run-to-failure. No actions or efforts are taken to maintain the equipment as the designer originally intended to make sure design life is reached. (NASA 2000)
- Reliability-centered Maintenance. The process used to determine the most effective approach to maintenance. (FEMP 2010)
- Resilience. Energy and water resilience is the ability of optimized operations to withstand, adapt, and recover from disruption as required. (FEMP n.d.)
Discussion
While overall O&M needs vary by site and system, a general representation of a comprehensive O&M program as envisioned by the United States Department of Energy’s Federal Energy Management Program (FEMP) is shown in Figure 1. This program is multifaceted, as shown by the green-shaded functional component areas and the blue-shaded strategic component areas. Both are designed and integrated such that they can support the overall delivery and effectiveness of a comprehensive O&M program and facilitate the identified core outcomes that are shown radiating outward.
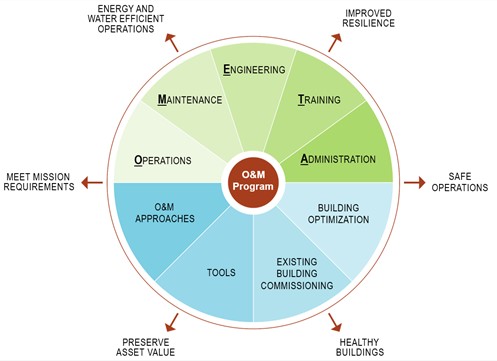
Comprehensive O&M Program Components
The functional component areas of a comprehensive O&M program (green slices) should be present in all O&M programs. The degree of their respective scopes will vary based on several factors, such as the size of the site, importance of the missions supported by the site, complexity of systems and equipment, age of the buildings and systems, and O&M delivery method (in-house, contracted, energy savings performance contract-provided, other, or a combination). All of the functional components shown should be present to the appropriate degree in each site’s O&M program. These functional components are presented in more detail below.
The strategic component areas (blue slices) are based on strategic areas identified by FEMP as complementing the overall delivery of O&M to achieve the expanded outcomes of energy and water efficiency, improved resilience, and healthy buildings. The strategic components are also presented below in more detail.
Funding (resources) to address these functional and strategic component areas is also addressed.
Functional Components
The functional components are based on the operations, maintenance, engineering, training, and administration (OMETA) concept described in the O&M Best Practice OMETA: An Integrated Approach to Operations, Maintenance, Engineering, Training, and Administration. The OMETA concept identifies key functional areas and their corresponding responsibilities and actions, as well as the interdependencies of these functional areas for comprehensive O&M delivery. From an O&M perspective, most facilities, plants, and systems that require operational actions and infrastructure upkeep will have some representation of the following five functional areas (Meador 1995):
- Operations—functional procedures and actions to enable a facility, process, or system.
- Maintenance—necessary upkeep and repair of a system and its components.
- Engineering—activities related to the design, monitoring, and improvement of a system and its components.
- Training—providing the necessary information and education for system operation, maintenance, and improvement.
- Administration—functional area that provides control of goals and resource needs.
Strategic Components
There are numerous programs, approaches, and tools that can be applied at a given site to enhance O&M delivery and outcomes. The selection of programs, approaches, and tools will vary based on site needs and capabilities. A summary of options and opportunities, as promoted by FEMP, is provided below by strategic component. Please note that while the approach presented below was developed with the federal government and its agencies in mind, there are other programs, approaches, and tools available from a variety of sources.
- O&M Approaches—maintenance approaches include some combination of run-to-failure, reactive, preventive, and predictive/proactive maintenance. Optimizing the application of these approaches maximizes the benefits of O&M based on available resources.
- Tools—refers to the effective use of the equipment and systems that support building O&M and energy and water use monitoring, such as computerized maintenance management systems, building automation systems, and building energy and water meters and submeters. Tools also include predictive maintenance technologies, such as infrared thermometers, ultrasonic detection devices, and vibration analyzers.
- EBCx—application of the building commissioning process throughout the building’s life. The commissioning of an existing building uses recognized approaches such as recommissioning, retrocommissioning, ongoing commissioning (monitoring-based commissioning and real-time commissioning), and re-tuning. The selection of an EBCx is based on the needs of a given building.
- Facility Optimization—wide range of offerings and activities that address facility needs such as 50001 Ready, comprehensive energy and water evaluations (as required by the Energy Independence and Security Act of 2007), and healthy buildings.
Funding
Delivering a comprehensive O&M program is resource intensive. In general, it is widely believed that federal O&M budgets do not adequately fund the completion of needed O&M. This belief is supported by the 2018 Financial Report of the United States Government, which indicates that as of September 30, 2018, deferred maintenance across the federal agencies totaled $166.6 billion, of which $147.3 billion was for property, plant, and equipment (Treasury n.d.). This report also states that “The consequences of not performing regular maintenance and repairs could include increased safety hazards, poor service to the public, higher costs in the future, and inefficient operations” (Treasury n.d.).
What is the appropriate level of funding for site O&M? The most commonly accepted guidance was developed by the National Research Council, which states “…the appropriate level of M&R [Maintenance and Repair] [annual] spending should be, on average, in the range of 2 to 4 percent of the current replacement value of this inventory” (NRC 1990).
In this report, ”maintenance” refers to planned upkeep of the property/equipment to assure proper operation over its anticipated life. “Repair” refers to the work needed to restore damaged or worn-out property/equipment to proper working condition.
Examples of when O&M budgets should be increased include:
- When the site’s deferred maintenance is determined to be unacceptably high and/or when deferred maintenance is shown to be trending upward over the last several years;
- When site operations are experiencing increasing equipment or systems failures;
- When systems or equipment required to support critical missions
- are found to have lagging O&M service completion, including operation testing,
- have noted condition deficiencies that remain uncorrected, and/or
- require O&M service providers that are not available on an emergency basis;
- When occupant satisfaction surveys indicate ongoing unresolved issues of comfort and reliability;
- There are known health and safety issues arising from poor equipment conditions; and
- Energy, water use, or both are increasing for no apparent reason beyond increasing mission requirements, occupancy, or usage profiles.
Solutions and Actions
The solutions and actions are addressed in two parts. First, the roles and responsibilities of key individuals, organizations, or both, involved in the comprehensive O&M process are identified; second, the steps that identify key activities and ideas to consider when developing your comprehensive O&M program are discussed.
Roles and Responsibilities
It is important to recognize that a comprehensive O&M program requires support and engagement from individuals and organizations across the facility.
- Facility Manager—in this Best Practice, facility manager refers to the individual that oversees the actions supporting the ongoing operation of the facility in a manner that is inclusive of O&M. The facility manager should make sure O&M resource needs meet site operational goals and monitor O&M program performance.
- O&M Manager—refers to the individual responsible for leading the O&M program by establishing the overall program philosophy, management approaches, and organizational structure needed to achieve O&M program goals. The O&M manager should work closely with the facility manager to make sure that the facility’s needs are fully met.
- Site Manager—refers to the individual responsible for overall site management. Site managers are often found at federal sites that are located on a campus and/or house multiple tenants or missions. The site manager should work with the facility manager and the O&M manager to clearly establish operational requirements, monitor O&M program performance, and support O&M resource requests.
- Tenants/Stakeholders—refers to the facility occupants. Tenants must work with the facility and O&M managers to clearly establish operational requirements while working within the site’s operating parameters (including building scheduling, equipment schedules and setpoints, energy and water efficiency goals, healthy building goals, and sustainability goals and policies). Special requirements that increase O&M service levels should be clearly identified by tenants, agreed upon by tenants, facility and O&M managers, and resourced by the facility manager with site manager and agency support.
- O&M Technicians—refers to the in-field O&M service providers. These staff possess knowledge of the facility’s equipment and systems and are resources to identify O&M delivery needs and opportunities. Technicians must operate within and support the O&M manager’s approaches and goals.
- O&M Contractors—providers of O&M services via contract. These providers must operate within and support the O&M manager's approaches and goals.
A detailed discussion on the operational actions and infrastructure across a facility is presented in the O&M Best Practice OMETA: An Integrated Approach to Operations, Maintenance, Engineering, Training, and Administration.
Steps to Include in a Comprehensive O&M Program
Step 1. Assess Your O&M Program
Identify the scope and objectives of your O&M program in terms of the following:
- Scope—what facilities are served by the O&M program?
- Objectives—does your O&M program have defined objectives that address efficiency, quality, reliability, and safety?
- Resources—what are the resources (funding, staff, tools, and equipment) available to deliver O&M?
- Performance—how well is your O&M program delivering services in terms of meeting the program’s stated and understood objectives across the facilities with the available resources? See the O&M Best Practice, Key Performance Indicators, for ideas about developing and applying KPIs to measure O&M performance and identify areas in need of improvement.
- Functionality—does your O&M program actively and successfully apply the identified OMETA functional areas?
- Strategies—what programs, approaches, and tools are currently being applied to improve O&M delivery and outcomes?
When addressed site-wide, completing this type of assessment may appear daunting, especially when reviewing performance. Consider concentrating on KPIs to measure performance to date.
Step 2. Determine Overall Goals for Your O&M Program
While the O&M program may already have defined objectives and goals, the information compiled in Step 1 can be used to inform the development of goals that address site-specific needs. Goals should be reasonably attainable. For example, during the performance assessment, it was found that reactive maintenance accounts for 50 percent of the maintenance costs. Because reactive maintenance is the costliest of the standard maintenance approaches, a goal for your program could be to reduce reactive maintenance costs by 10 percent. There are cases in which such a reduction in reactive maintenance has been achieved by instituting a reliability-centered maintenance program.
Step 3. Develop Potential Approaches to Improve Program Performance
Based on the findings of the site O&M assessment (Step 1) and your O&M program goals (Step 2), identify the actions needed to achieve targeted improvements. In cases where the O&M program has already achieved high performance levels, identify ways to assure program persistence and look to expand to other systems, buildings, or sites. In all cases, it is important to look at the performance in terms of the various functional program components (i.e., OMETA) to make sure that cross-functional area support needs are identified. Strategic approaches should be considered in terms of (1) functional component support needs or impacts and (2) the potential for interactive effects, synergistic effects, or both.
Step 4. Obtain Site Management Support
Obtaining site management support can be a difficult task that requires making sure that the benefits resulting from the proposed actions will appreciably exceed the (perceived) effort and investment required to implement them (benefits >> effort + cost).
The improvement opportunities identified in Step 3 are meant to improve the overall delivery of O&M at the site and result in improved safety and efficiency, extended equipment life (leading to reduced capital expenditures), and upgraded equipment and systems availability and operability. Identification and some level of quantification of these benefits should be included in the request for support.
Required resources can take several forms. A list of potential resources is provided below as an example. Please note that this list is not all inclusive.
- Supportive and adaptable organizational culture that accommodates new priorities and approaches such as
- Establishing O&M program goals,
- Development and use of KPIs,
- Progress tracking and reporting based on KPIs on a regular basis,
- Regularly (monthly, quarterly, and annually) reporting O&M program performance to the facility and site managers, and
- Ongoing support from the facility and site managers through tenant engagement and meeting resource (i.e., funding and staffing) needs.
- Funding budgets and allocations
- Staffing budgets and allocations
- Staff skills to complete new activities
- New testing or monitoring equipment, or both.
One item to highlight regarding the above list is the importance of progress reporting to the facility and site managers. These updates provide ongoing communication about the progress and outcomes of the new approaches being implemented. Approaches that underperform can be reviewed for refinement opportunities or possibly even cancellation, while approaches that are performing successfully can be highlighted to build visibility, trust, and additional support.
Step 5. Implement
Listed below are some recommendations to consider when implementing new O&M approaches or procedures. This list is not all inclusive, and additional steps may be required for cases such as site policies or contract requirements.
- Identify and request needed resources—funding, training, equipment, and staff.
- Develop implementation milestones.
- Meet with affected staff and departments to inform them of changes and impacts. Solicit input on the proposed implementation path and consider and incorporate the input.
- Implement the new O&M approach.
- Monitor and track outcomes. Apply accepted benchmarks and KPIs where possible and practical. In cases where outcomes are not in-line with the projected outcomes, benchmarks, or KPIs being applied, identify potential modifications and apply them.
- Report progress and outcomes as discussed in Step 4.
- Continue to monitor, evaluate, troubleshoot, and report progress until the implementation period is complete. Consider the ongoing use of benchmarks and KPIs for new applications that are adopted as part of the site’s O&M program procedures.
In cases where there are multiple applications or measures to implement, consider using a phased approach in the implementation process. This means starting with smaller, less-complicated measures that are more likely to succeed. Implementation of the subsequent measures will then build off of the initial success.
Conclusion and Next Steps
A comprehensive O&M program is essential for the successful operation and maintenance of the equipment and systems that support a facility. An O&M program is all inclusive and incorporates all the efforts needed to meet its objectives. Five steps have been provided for guidance in developing and implementing a comprehensive O&M program. Although the framework and components of such a program are often similar for a variety of facilities, each facility’s program is based on the specific mission needs as well as the distinctive characteristics of the building, equipment, and systems.
The next steps for sites looking to improve their O&M program performance are as follows:
- Review their O&M program performance data to determine if the program is performing as needed or if improvement is in order. If the site is already using benchmarks and KPIs to measure O&M program performance, they should have some valid measurements of performance on which to base a conclusion. Not having benchmarks or KPIs may be a cause for concern.
- Determine if the site’s O&M performance is in-line with the site’s expectations for safety, efficiency, availability, and reliability. Possible outcomes include
- Data (as determined by outcomes of benchmarks/KPIs and feedback from the site manager, O&M manager, and tenants) shows that all O&M objectives and targets are being met. In this case, the next step is to make sure that the O&M program remains fully resourced and that management oversight is used to assure continued high performance.
- Data shows that the O&M program is not meeting its performance objectives and targets. In this case, the next step is to initiate a site O&M program assessment as discussed in Step 1, proceed to work with the findings to identify opportunities for improvement, and implement new approaches and measures.
- Sufficient data is not available; the site should immediately proceed with a full O&M program assessment (Step 1) to determine areas of need and develop an implementation plan.
Additional Resources
FEMP O&M Best Practices Website
FEMP O&M Best Practices have been developed for a variety of topics. The Best Practices listed below have been cited in this document, and additional documents are available on the FEMP O&M Best Practices website.
- “O&M Best Practices Issues Discussion: Healthy Building O&M in Existing Buildings"
- “Existing Building Commissioning Approaches Summary”
- “Applying Key Performance Indicators”
- “OMETA: An Integrated Approach to Operations, Maintenance, Engineering, Training, and Administration”
- “Re-tuning Buildings.”
ANSI/ASHRAE ACCA Standard 180-2018: Standard Practice for Inspection and Maintenance of Commercial Building HVAC Systems
This American Society of Heating, Refrigerating, and Air-Conditioning Engineers (ASHRAE) standard provides a standardized approach to inspecting and maintaining heating, ventilation, and air conditioning (HVAC) systems. This standard focuses on “the impacts of maintenance on occupant thermal comfort, energy efficiency, and indoor air quality.” Included in the standard are definitions and guidance on the concepts and implementation of maintenance plans, maintenance programs, maintenance program objectives, and more. The standard may be purchased through ASHRAE.
References
FEMP ─ Federal Energy Management Program. 2010. Operations & Maintenance Best Practices: A Guide to Achieving Operational Efficiency. Release 3.0. Prepared by Pacific Northwest National Laboratory for FEMP, Richland, WA. https://www.wbdg.org/FFC/DOE/DOECRIT/femp_omguide.pdf.
FEMP – Federal Energy Management Program. n.d. Technical Resource Navigator Glossary. https://femp.energy.gov/resilience/technical-resilience-navigator-glossary.
Hunt WM. 2019. Operations and Maintenance Strategies and Approaches. PNNL-SA-146418. 2019 Energy Exchange. Accessed at https://www.energy-exchange.com/wp-content/uploads/T7S7-Hunt-Masters.pdf.
Meador RJ. 1995. Maintaining the Solution to Operations and Maintenance Efficiency Improvement. Pacific Northwest National Laboratory, Richland, WA. https://www.pnnl.gov/dsom/publications/26005.pdf.
NASA – National Aeronautics and Space Administration. 2000. Reliability Centered Maintenance Guide for Facilities and Collateral Equipment. National Aeronautics and Space Administration, Washington, D.C. https://www.hq.nasa.gov/office/codej/codejx/Assets/Docs/RCMGuideMar2000.pdf.
NE SpinTech. 2018. Glossary of Maintenance Terms. New England SpinTech: Reliability and Maintenance Solutions. Spencer, MA. Accessed at https://www.ne-spintech.com/wp-content/uploads/2018/04/Glossary-of-Maintenance-Terms.pdf.
NRC – National Research Council. 1990. Committing to the Cost of Ownership: Maintenance and Repair of Public Buildings. National Research Council, Washington, D.C. National Academy Press. https://www.nap.edu/catalog/9807/committing-to-the-cost-of-ownership-maintenance-and-repair-of.
Treasury – U.S. Department of the Treasury. n.d. 2018 Financial Report of the United States Government. Washington, D.C. Accessed at https://www.fiscal.treasury.gov/files/reports-statements/financial-report/2018/03282019-FR(Final).pdf.
Published May 2022