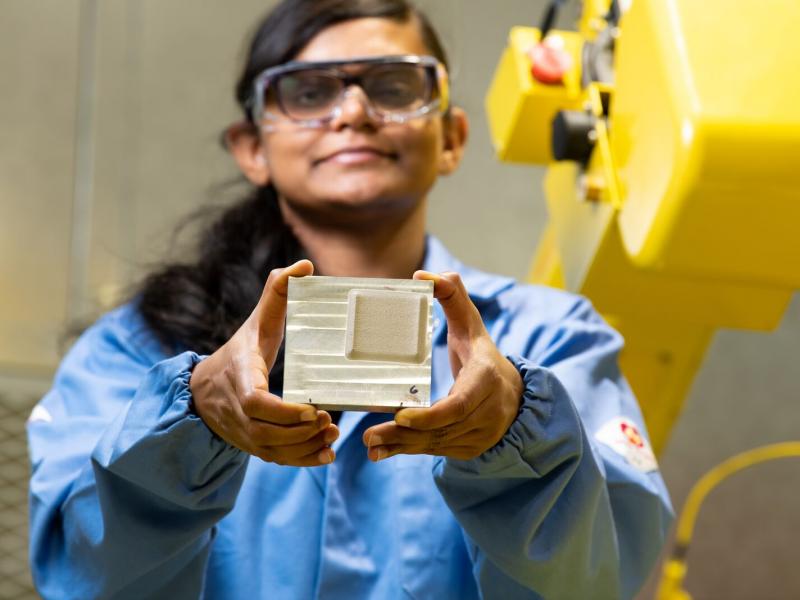
Cold Spray
Cold Spray
Supersonic metal
deposition to the rescue
Supersonic metal
deposition to the rescue
PNNL is working on a new spray coating to repair dam turbines. The coating, called cold spray, is more effective than the current practice of welding damaged turbines.
(Photo by Andrea Starr | Pacific Northwest National Laboratory)
Cold spray is a method of depositing powder particles onto a component—most commonly metallic—at supersonic speeds. A compressed and heated gas jet propels the particles at speeds from Mach 1 to Mach 3. The resulting high-speed impact causes the powder particles to deform and adhere, building up on the component and forming strong metallurgical bonds. This solid-phase additive manufacturing process can result in high-density and high-rate depositions with superior material properties than those attained with other metal and additive deposition technologies.
The Smart Advanced Manufacturing (SAM) program at Pacific Northwest National Laboratory (PNNL) is using its cold spray capabilities to research alternative approaches for repairing hydropower turbines and nuclear waste tanks. With cold spray, neither melting nor material degradation occurs, and in the case of hydroelectric turbines, the blades remain in their original shape. The technology facilitates in-field repairs to large, high-value structures.
Cold spray can deposit materials that have hardness, corrosion resistance, and/or wear resistance properties that exceed those of the base metal to provide superior equipment performance while reducing costs of repair. The technology also allows for custom materials alloying and tailoring of the resulting mechanical and physical properties.
The cold spray team has demonstrated a process that delivers material with cavitation erosion resistance that is three times higher than that of stainless steel plate or filler metal and about eight times higher than that of the heat-affected zone carbon steels commonly used to repair hydropower turbines.
Beyond repair
Because cold spray deposits do not undergo melting during processing, the technique holds promise for additive manufacturing. Research shows the potential to create entirely new alloy systems that are otherwise incompatible in melt-based or casting processes. In addition, cold spray allows materials to be deposited and bonded to existing components for added functions. The deposited materials can be selected to provide protection from harsh environmental conditions or, in the case of ceramics, create materials that are usable at higher temperatures than originally intended and extend part service life.
Research advances
PNNL research is demonstrating the potential of cold spray to reduce the cost and improve the performance of new and existing components throughout the energy sector. This new, high-pressure cold spray capability will support the development of processes ranging from high-volume automated factory production to manual field repair.