- Best Practices for Equipment O&M
-
O&M Best Practice Issue Discussions
- Advanced Maintenance Approach: Reliability Centered Maintenance
- Applying Key Performance Indicators
- Comprehensive O&M Program
- Contract Challenges and Improvements
- Cybersecurity for O&M Systems
- Existing Building Commissioning Procurement
- Healthy Building O&M
- Integrating and Analyzing Building Information to Support O&M
- Maintenance Approaches
- OMETA: An Integrated Approach to Operations, Maintenance, Engineering, Training, and Administration
- Prioritizing O&M Actions
- Re-tuning Buildings
- Tools
- Glossary
Best Practices for Standby Generator Operations and Maintenance
Table of Contents
- Introduction
- Description of Technology
- Key Components
- Safety Issues
- Maintenance of Technology
- Maintenance Checklist
- Performance Monitoring
- O&M Cost
- Additional Support
- Sources of Information
Introduction
Standby generators are self-contained systems that provide electricity when power from the primary source, usually the local electric grid, is unavailable. When the grid experiences an outage, an automatic transfer switch (ATS) signals the standby generator to start and begin providing power. When the grid is again available, the load and power are transferred back to the grid, and the ATS signals the generator to stop.
Standby generators are usually internal combustion engines coupled with an electric generator and can be powered by diesel fuel, propane, natural gas, or other liquid fuels. These generators typically operate for a limited amount of time and are not meant for extended use. Executing the necessary operations and maintenance (O&M) on this system is crucial for optimized efficiency and preparation for power outages.
The purpose of this equipment O&M Best Practice is to provide an overview of system components, maintenance requirements, and best practices to assure the safe and efficient operation of standby generators. Neglecting proper maintenance of standby generators could result in premature system failure and lack of power during an outage. Support organizations should budget and plan for routine maintenance of standby generators to assure reliable operation.
Description of Technology
Standby generators are sized according to their electrical output (expressed in kilowatts [kW]) and are classified in one of three categories: residential, commercial, or industrial. Residential generators are typically operated on a single electric phase, while commercial and industrial generators are usually three-phase devices. Standby generators are considered distinct from emergency generators in that the latter typically serve very specific loads and are usually required by code for life-health-safety reasons.
According to the NFPA 110 Standard for Emergency and Standby Power Systems (NFPA 2019) developed by the National Fire Protection Association (NFPA), there are two levels of emergency power supply systems.
- Level 1 – where failure of the equipment to perform could result in loss of human life or serious injuries.
- Level 2 – where failure of the emergency power supply system to perform is less critical to human life and safety.
The balance of this guide will focus on commercial standby generators (Level 2 systems, according to the NFPA 110 Standard) because they are most commonly used for building-level standby generation.
Standby generators can be mobile (on wheels/skid-mounted), or they can be stationary with fixed mountings. According to the National Electrical Code (NFPA 2020), all stationary generators that are integrated into a building’s electrical system are required to be hardwired and contain an ATS for safety purposes.
Standby generators can operate on a variety of fuels and some on multiple fuels. The most common fuels are diesel, natural gas, gasoline, and propane. There are some generators capable of burning jet fuel, dual fuels (diesel and natural gas/propane), as well as different chemistries of biofuels. Figure 1 shows a typical standby generator installation housed in its own containment area.

Key Components
The main components of a typical engine-driven standby generator are described below and are shown in Figure 2. Each of these components or systems must be maintained for basic operation and for the larger system to function efficiently.
- Engine—provides mechanical energy that gets converted to electrical energy. The engine’s type and size determine the generator’s fuel use and power output.
- Generator—converts mechanical energy into electricity.
- Fuel supply system—consists of a fuel tank and associated delivery piping and components (e.g., diesel fuel pump, fuel filter, and a nozzle or injectors).
- Lubrication—assures smooth operation and protects against wear; typically housed in a sump or reservoir.
- Cooling System—consists of a cooling pump, coolant fluid, and a radiator (heat exchanger) with a fan to dissipate the heat.
- Starting System—switches the engine and generator on (larger standby generators use compressed air injected into the cylinders to provide starting power).
- Exhaust System—captures and directs exhaust gases to an appropriate location for potential treatment (i.e., emission control) and ultimate dissipation.
- Control Panel—contains devices, including the system controller, to manage and monitor generator operation from initial start to steady-state operation to shut-off. Monitored generator functions include oil pressure and coolant temperatures as well as current, voltage, and frequency.
- Air Intake System—directs and filters combustion air entering the engine.
- Batteries—provides generator power for start-up during a power outage.
- Battery Charger—typically connected to utility power and keeps batteries charged.
All of the above components function with a system controller that monitors and controls operation from initial start to steady-state operation to shut-off. Depending on the generator type, location, and configuration, the entire assembly may be housed in a factory-built enclosure, a small building, or be built into a larger facility. Figure 2 highlights a typical standby generator, with the major components identified.
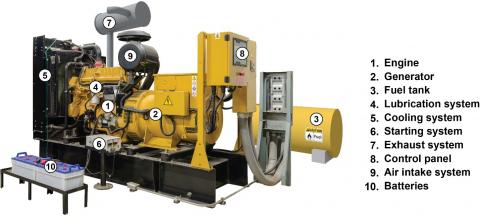
Safety Issues
Federal, state, and local regulations will require permitting before standby generator installation and/or operation. These permits may include emissions certification and renewal requirements. The permitting process will require that specific safety and environmental actions be completed before operation. The standby generator and associated safety and environmental actions will be subject to periodic inspection.
Whether required by local code or not, safety and environmental stewardship must be treated with the utmost importance. An excellent reference for standby generator operation and safety is the NFPA 110 Standard for Emergency and Standby Power Systems (NFPA 2019).
General guidelines for safety and usage that are provided by the engine manufacturer and the installing contractor should be followed. Installation, repair, and maintenance should always be in accordance with the applicable building codes and manufacturer’s instructions and recommendations. The following guidelines are presented only as supplemental material.
- Exhaust systems must be properly installed, adequate ventilation must be provided to assure unobstructed flow of cooling/ventilating air, and emissions must be directed away from building air intakes as well as areas where people may pass or gather.
- The area around the generator should be clean and free of any combustible material that can be hazardous.
- All power supplies should be turned off/disconnected at the source before servicing the generator, including the batteries.
- The frame of the generator should have proper grounding (earthen ground).
- All fuel sources should be kept cool and dry. Most fuels have a resident design life and should be monitored for degradation and actively treated according to the supplier’s specifications.
Maintenance of Technology
Adopting a preventive and predictive maintenance program is critical to assuring that the generator system functions properly and efficiently. Keeping the standby generator properly maintained through active maintenance will improve system performance, increase the operating life, and protect the asset.
Maintenance of standby generators should be conducted by qualified personnel. Maintenance activity should be logged to confirm and document completion and provide a foundation for trend analysis.
Maintenance Checklist
For all standby generator maintenance, it is important to follow the manufacturer’s recommendations. Proper maintenance should only be performed by trained and qualified personnel. The example diesel generator checklist in Table 1 below provides recommended actions and associated frequencies by standby generator component type. This checklist does not supersede maintenance recommendations from the generator manufacturer, nor is it a replacement for contracted O&M or warranty services. For maintenance related to additional auxiliary components such as built-in engine heaters, please refer to the equipment’s owner’s manual.
Table 1. Standby generator maintenance checklist.
Component |
Action |
Maintenance Frequency |
|||
Weekly |
Monthly |
Bi-Annually |
Annually |
||
Electric Generator |
Run generator with no load for several minutes until operating temperature is achieved; verify control function and look for alarms, warnings, or indicator lights. |
X |
|||
Inspect engine, radiator, and generator for debris, as well as for loose or broken fittings, hoses, wires, and guards. |
X |
||||
Run the system for 1 hour under a full building load initiated by ATS. Record the system operating parameters (e.g., coolant temperature, oil pressure, battery voltage, and generator alternating current voltage). |
X |
||||
Perform load bank test. |
X |
||||
Fuel System |
Check fuel tank to assure levels are adequate and, if present, drain water from filter bowl. |
X |
|||
Assure there are no fuel or other fluid leaks. |
X |
|
|
|
|
Inspect accessible areas of fuel tank for damage and corrosion. Verify that emergency vent components move freely and are not obstructed (all tanks). |
X |
||||
Replace fuel filter(s). |
|
|
|
X |
|
Inspect fuel hose, replace if necessary. |
|
|
|
X |
|
Lubrication System |
Check oil level and inspect system components for leakage. |
X |
|||
Sample oil. |
|
|
X |
|
|
Grease generator bearing (if applicable). |
X |
||||
Replace oil and oil filter (based on oil sample results) and inspect system components. |
|
|
|
X |
|
Replace engine oil hoses if necessary. |
|
|
|
X |
|
Cooling System |
Inspect hoses and belts, replacing if needed, and verify that the engine block heater is operating properly. |
X |
|||
Check engine coolant level. |
|
X |
|
|
|
Check coolant lines and connections. |
|
|
X |
|
|
Check coolant condition with kit/test strip, replace if needed. |
|
|
|
X |
|
Inspect and adjust belts, verify engine block heater is operating, check radiator cap (replace cap if gasket is cracked or damaged), clean exterior of radiator, inspect fan shroud, and inspect system components. |
|
|
|
X |
|
Starting System |
Assure that the generator is in “Auto” mode for automatic start-up. |
X |
|||
Clean battery connections and apply corrosion inhibitor. Check starter motor and charger connections and inspect system components. |
X |
||||
Check battery electrolyte level and specific gravity. |
|
|
X |
|
|
Inspect and clean engine speed timing sensor. |
|
|
|
X |
|
Exhaust System |
Perform visible emissions observation. |
X |
|
|
|
Clean crankcase breather and inspect system components. |
X |
||||
Inspect exhaust system, muffler, and exhaust pipe. |
X |
||||
Electrical System |
Check that the generator’s circuit breaker is closed. |
X |
|
|
|
Clean out electrical boxes, panels, and alarm boxes. Inspect wiring. |
|
|
X |
|
|
Inspect and clean ATS contacts and wiring. |
X |
||||
Inspect air intake system. Replace filter if needed. |
X |
||||
System Documentation |
Record all run hours. |
Upon activity completion |
|||
Document all maintenance activities in log book or electronic computerized maintenance management system. |
Upon activity completion |
Performance Monitoring
Depending on the age and type of the available control system, a standby generator can be monitored via a building automation system (BAS) whereby critical parameters are captured, tracked, and trended. These metrics may include run hours, exhaust temperature and composition, and fuel rate. Without a BAS-enabled generator, the performance should be monitored each week, month, and year by operating the generator, recording system operating parameters, and performing visual emissions observations. Any differences in system operating parameters should be trended, noted, and acted upon if out of compliance or specification.
O&M Cost
Standby generators require preventive and predictive maintenance and regular testing to assure the highest reliability. The cost of O&M for standby generators varies depending on the size of the generator, the operating profile, the type of fuel used, and the maintenance plan. A survey of reported maintenance costs found significant variability. In recent documents (NREL 2014, 2019), the National Renewable Energy Laboratory reports maintenance costs as a function of the generator size and being composed of both fixed cost ($/kW) and variable ($/kWh) costs. Assuming a 300 kW standby generator operating under 200 hours per year, the range of O&M costs is between $8,000 and $10,500 per year.
Additional Support
Over the years, DOE has funded numerous projects, programs, and documents focused on standby and backup power systems. Much of this information is still relevant and can be accessed and linked to at: https://www.energy.gov/ceser/emergency-preparedness/community-guidelines-energy-emergencies/using-backup-generators.
More information about O&M for systems and maintaining energy resilience is discussed in the Department of Defense’s paper, Energy Resilience: Operations, Maintenance, & Testing (OM&T) Strategy and Implementation Guidance at: https://www.acq.osd.mil/eie/Downloads/IE/2%20-%20Energy%20Resilience%20-%20OM&T%20Guidance%20(v17)%20-%20PR%20Version%20-%20approved.pdf.
The U.S. Army Office of Energy Initiatives (OEI) conducted energy resilience tests at several Army installations to replicate widespread utility power loss. These exercises were an opportunity to identify infrastructure vulnerabilities that hinder mission readiness. OEI recommends that generators be tested monthly to assure enhanced energy resilience. More information can be found in the OEI News article, Securing Army Installations with Energy that is Resilient, Affordable, and Sustainable at: https://www.naesco.org/data/news/documents/Army%20OEI%20News%20-%20Summer%202019.pdf.
The Handbook of Facility Management: Tools and Techniques, Formulas and Tables provides information on how to establish a preventive maintenance program and solve problems related to mechanical, electrical, and building maintenance. This handbook can be accessed at: http://www.ncef.org/content/handbook-facility-management-tools-and-techniques-formulas-and-tables.
Sources of Information
DoD – U.S. Department of Defense. 2017. Energy Resilience: Operations, Maintenance, & Testing (OM&T) Strategy and Implementation Guidance. Department of Defense, Washington, D.C. https://www.acq.osd.mil/eie/Downloads/IE/2%20-%20Energy%20Resilience%20-%20OM&T%20Guidance%20(v17)%20-%20PR%20Version%20-%20approved.pdf.
DOE – U.S. Department of Energy. Using Backup Generators. Department of Energy Office of Cybersecurity, Energy Security, and Emergency Response, Washington, D.C. https://www.energy.gov/ceser/emergency-preparedness/community-guidelines-energy-emergencies/using-backup-generators.
McGhee, Michael F. Securing Army Installations with Energy that is Resilient, Affordable, and Sustainable. U.S. Army Office of Energy Initiatives, Washington, D.C. https://www.naesco.org/data/news/documents/Army%20OEI%20News%20-%20Summer%202019.pdf.
NFPA – National Fire Protection Association. 2019. NFPA 110 Standard for Emergency and Standby Power Systems. National Fire Protection Association, Quincy, MA. https://www.nfpa.org/codes-and-standards/all-codes-and-standards/list-of-codes-and-standards/detail?code=110.
–––. 2020. NFPA 70 National Electrical Code. National Fire Protection Association, Quincy, MA. https://www.nfpa.org/codes-and-standards/all-codes-and-standards/list-of-codes-and-standards/detail?code=70.
NREL – National Renewable Energy Laboratory. 2014. Backup Power Cost of Ownership Analysis and Incumbent Technology. National Renewable Energy Laboratory NREL/TP-5400-60732. Golden, CO. https://www.nrel.gov/docs/fy14osti/60732.pdf.
–––. 2019. A Comparison of Fuel Choice for Backup Generators. National Renewable Energy Laboratory NREL/TP-6A50-72509. Golden, CO. https://www.nrel.gov/docs/fy19osti/72509.pdf.
Piper, James. 1995. Handbook of Facility Management: Tools and Techniques, Formulas and Tables. Prentice Hall, Paramus, NJ.
Actions and activities recommended in this Best Practice should only be attempted by trained and certified personnel. If such personnel are not available, the actions recommended here should not be initiated.
Published July 2021