- Best Practices for Equipment O&M
-
O&M Best Practice Issue Discussions
- Advanced Maintenance Approach: Reliability Centered Maintenance
- Applying Key Performance Indicators
- Comprehensive O&M Program
- Contract Challenges and Improvements
- Cybersecurity for O&M Systems
- Existing Building Commissioning Procurement
- Healthy Building O&M
- Integrating and Analyzing Building Information to Support O&M
- Maintenance Approaches
- OMETA: An Integrated Approach to Operations, Maintenance, Engineering, Training, and Administration
- Prioritizing O&M Actions
- Re-tuning Buildings
- Tools
- Glossary
Best Practices for Ground Source Heat Pump Operation and Maintenance
Table of Contents
- Introduction
- Description of Technology
- Key Components
- Safety Issues
- Maintenance of Technology
- Maintenance Checklist
- Performance Monitoring
- O&M Cost
- Additional Support
- Sources of Information
Introduction
Ground source heat pumps (GSHPs) can significantly improve the efficiency of heating and cooling systems and are considered a renewable energy technology. Regular operations and maintenance (O&M) of GSHP systems will make sure they continue operating effectively. In addition, tracking performance will help identify potential issues with the system and achieve maximum savings. Unfortunately, most GSHP systems do not include performance monitoring equipment. In this case, energy production must be estimated using system modeling, and regular O&M becomes even more important to identify issues early.
The purpose of this Best Practice is to provide general information about the key components of GSHP systems and to familiarize the designated staff member with the types and frequency of maintenance typically performed to keep a GSHP system in good working order.
Description of Technology
A GSHP system is a heating, ventilation, and air conditioning (HVAC) technology that can provide space and/or water conditioning (heating and/or cooling) for buildings. Heat pump systems do not create energy. They just move it around. What differentiates GSHPs from air-source heat pumps is how these systems use either the earth (ground) or water—either groundwater or open bodies of water—as a heat source and sink for heat transfer. In contrast, air-source heat pumps use the air as their heat source and sink.
In cooling mode, the GSHP system removes heat from the building and transfers it into the ground (or another heat sink such as a pond). In heating mode, the GSHP system reverses this process, removing heat from the ground (or another heat source) and transferring it into the building.
GSHP systems are classified as renewable energy technologies because the resource being used is the constant temperature of the heat sink and source. GSHPs are also known as geo-exchange heat pumps, ground coupled heat pumps, geothermal heat pumps, earth coupled heat pumps, ground source systems, groundwater source heat pumps, well water heat pumps, and solar energy heat pumps, among other variations (FEMP 2001).
GSHP systems are composed of indoor units, a ground coupled heat exchanger (GCHX), and water circulation systems. There are two types of indoor heat transfer units designated by the primary method of heat transfer. Water-to-air units condition air and water-to-water units condition water. The conditioned air or water is then circulated to condition the building. Figure 1 is a diagram of a GSHP system with water-to-air units.
Outdoor GCHX Indoor Equipment including
(Open-Loop Wells) Pumps and Indoor Units
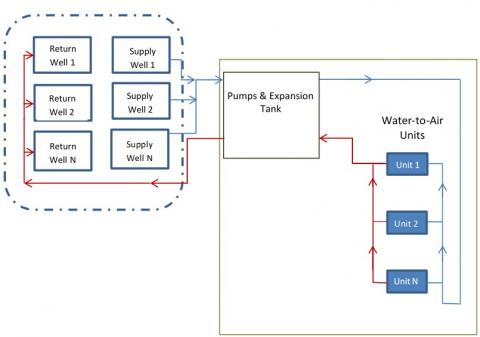
There are three primary categories of GSHP systems, which are based on the type of GCHX used:
- Open-loop systems use wells or open bodies of water as direct heat transfer mediums. Groundwater is pumped to the GSHP unit’s heat exchanger, where heat is transferred directly from the water loop to the GSHP. Groundwater must be filtered to remove sediment, minerals, and other corrosive agents. To reduce this impact, open-loop systems can include a plate-and-frame heat exchanger for the whole system. This allows heat exchange between the well water and the indoor building loop while separating the two. Open-loop wells generally depend on groundwater flow to continually renew the groundwater resource at the desired temperature. Open-loop systems appear in Figure 2 as “wells to groundwater” and a “standing column well.”
- Closed-loop systems use a heat transfer fluid, such as an antifreeze solution, inside a sealed pipe to exchange heat with earth or a body of water. A heat exchange pipe is buried in the ground, either horizontally or vertically, or submerged in a body of water. In a closed-loop system, heat transfer occurs in the ground between the heat transfer fluid and the soil (or water) and again between the heat transfer fluid and the GSHP. These systems appear in Figure 2 as “surface water loops,” “ground heat exchangers in vertical bores,” and the “ground heat exchanger horizontal loop.”
- Direct-expansion systems use copper coils directly installed underground for a direct exchange of heat between the refrigerant and earth (FEMP 2001). However, because of the high costs of materials and installation, as well as durability and other possible issues, these systems are rarely installed.
Hybrid systems incorporate additional heating or cooling components into the system to reduce ground loop requirements when heating and cooling loads are unbalanced. These components may be a cooling tower or boiler. Maintenance of these components is not discussed in this Best Practice. An optional cooling tower is shown in Figure 2 with the “matrix of ground heat exchangers and vertical bores.”
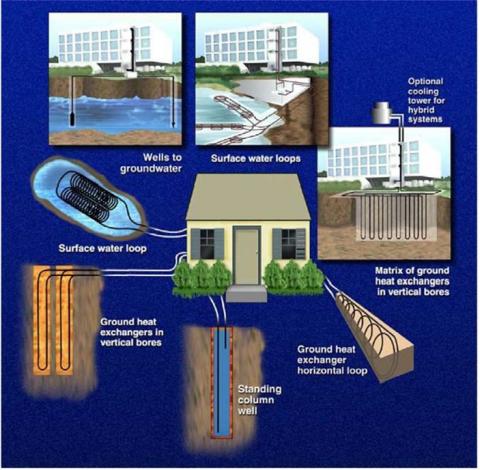
Key Components
A GSHP system is a collection of systems that work together. The indoor heat exchange equipment consists of two systems: the indoor units and the circulating equipment. This equipment can be located in a mechanical room or throughout the building. The third system is the outdoor GCHX.
Components of the three systems are addressed below.
Indoor Units
As shown in Table 1, the components in both water-to-air and water-to-water indoor units are generally the same, with a few differences.
Table 1. Components of indoor water-to-air and water-to-water units.
Component |
Water-to-Air Unit |
Water-to-Water Unit |
Blower assembly |
X |
|
Air coil |
X |
|
Thermostatic expansion valve |
X |
|
Refrigerant-to-water heat exchanger |
X |
X |
Water-to-refrigerant heat exchanger |
X |
|
Compressor |
X |
X |
Refrigerant reversing valve |
X |
X |
Air filter |
X |
|
Unit controls |
X |
X |
Water regulating valve |
Optional |
Optional |
Desuperheater |
Optional |
The indoor unit components can include the following:
- Blower assembly – fan with motor (labeled ”Supply Fan” in Figure 3)
- Air coil – refrigerant-to-air finned tube coil for heating and cooling the air (labeled “Air Coil Condenser in Heating Evaporator in Cooling” in Figure 3)
- Thermostatic expansion valve – regulates refrigerant flow into air coil
- Refrigerant-to-water heat exchanger – transfers heat between the water loop and unit compressor
- Water-to-refrigerant heat exchanger – heats and cools water in a water-to-water unit. • Compressor – converts a cool, low-pressure gas into a hot, high-pressure gas
- Refrigerant reversing valve – reverses the refrigerant flow when the mode of operation changes (e.g., from heating to cooling or from cooling to heating)
- Air filter – removes particles and dust from the air entering the unit before they reach the air coil
- Unit controls – sensor, controller, and other devices necessary to operate the unit in either heating or cooling mode
- Water regulating valve – may be installed to control the amount of loop water entering the unit if the system’s loop temperature is subject to wide fluctuations
- Desuperheater – optional device to transfer refrigerant heat to domestic hot water in a water-to-air GSHP. Figure 3 illustrates the standard components of an indoor water-to-air unit. Figure 4 is a photograph of a ceiling-mounted water-to-air indoor unit.
Figure 3 illustrates the standard components of an indoor water-to-air unit. Figure 4 is a photograph of a ceiling-mounted water-to-air indoor unit.
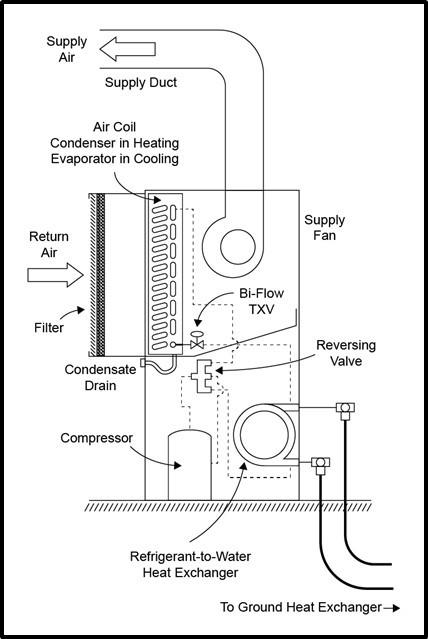
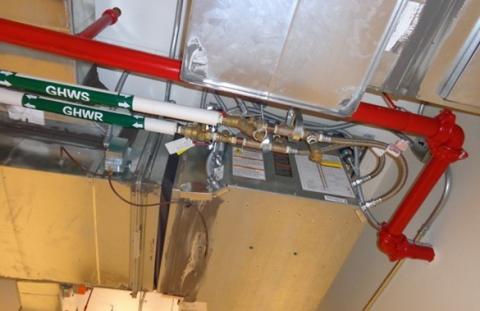
Circulating Equipment
Components of indoor circulating equipment, which is generally located in a mechanical room, can include the following:
- Pumps – circulate the loop water through the building and GCHX
- Expansion tank – handles the excess volume of water resulting from temperature changes in the building loop
- Plate-and-frame heat exchanger – generally included for open-loop systems • Water filter – may be included for open-loop systems
- Controls:
- Loop controller – monitors and controls the operation of the water loop
- Water sensors and switches – control system operation
- Pump controls – control the system circulating pump(s)
- Interface – works with other controls. such as the ventilation system, boiler, and cooling tower
The outdoor GCHX is generally located in an open area near the mechanical room to minimize piping requirements between the GCHX and the indoor equipment. The GCHX can include the following:
- Pipes – For a closed-loop system, the GCHX consists of an underground (or underwater) network of high-density polyethylene (HDPE) pipe.
- Wells – For an open-loop system, the GCHX consists of production or source wells with pumps and discharge or injection wells. In some locations, a single well can be used for both the source and discharge well.
- Auxiliary cooling and heating equipment – A cooling tower or boiler can be added to a system to reduce ground loop requirements when heating and cooling loads are unbalanced.
Safety Issues
Standard electrical and mechanical safety practices apply to these systems. Antifreeze solution, which is typically used in the ground loop as a heat transfer fluid, is toxic to humans and animals, so disposal requires compliance with local regulations.
Maintenance of Technology
Keeping GSHP systems properly maintained through preventive maintenance will minimize overall O&M requirements, improve system performance, and protect the asset. Operators show follow the guidelines in the equipment manufacturer’s maintenance manuals and check the specific warranty details for the installed system. Indoor heat pump units generally have a standard 1-year warranty with an optional 5-year refrigerant circuit warranty. Closed-loop GCHXs can have 50-year warranties and open-loop GCHXs can have 20 – 25-year warranties.
GCHXs are durable, reliable, and have few moving parts. The maintenance of the fluid loop primarily consists of cleaning strainers and maintaining the proper pressure and correct concentration of antifreeze. Pumps for the fluid loop requires standard maintenance. (Refer to FEMP O&M Best Practices Guide, Section 9.9, Pumps, available at https://www1.eere.energy.gov/femp/pdfs/om_9.pdf.)
Maintenance of the indoor water-to-air units is similar to maintenance of air-to-air heat pumps because both units have similar components such as fans, filters, an air coil, a condensate drain, a refrigerant reversing valve, and compressors. (Refer to the U.S. Department of Energy’s Energy Saver website: http://energy.gov/energysaver/operating-and-maintaining-your-heat-pump.) Because water-to-water units have components similar to water-to-air units, the required maintenance is also similar. Heat pump equipment is not exposed to outdoor elements and as a result, the units actually require less maintenance than typical air-source heat pumps.
It is important to keep a good log of services performed, controller alarms, equipment down time, and other relevant issues noted and resolved. This will help identify recurring warranty issues or systemic problems and make sure warranties remain valid. Work orders related to the GSHP system should be recorded.
Maintenance Checklist
For all equipment maintenance, follow the manufacturer’s instructions. Proper maintenance of these systems is extensive and should only be performed by qualified personnel with previous GSHP O&M experience. Make sure component conditions and operating temperatures, pressures, and flows are within manufacturer and design parameters.
Proper pump operation for all systems is critical, so field check of pumps should be performed frequently. At least weekly checks of the pumps are recommended, but monthly inspections are needed at a minimum. For open-loop systems, entering and leaving temperatures of the plate-and-frame heat exchanger, as well as pressure drops across the GCHX groundwater strainer, should be checked often. At least weekly checks of these items are recommended, but monthly inspections are needed at a minimum.
Below is a sample checklist. Consult the manufacturer’s information for acceptable operating parameters.
Table 2. Sample maintenance checklist of for GSHP systems.
Component |
Action |
Frequency |
Indoor Units |
||
General indoor units |
|
Quarterly |
|
Quarterly |
|
|
Quarterly |
|
|
Annually |
|
|
Annually |
|
|
Annually |
|
|
Annually |
|
|
Annually |
|
Refrigerant-to-air coil |
|
Semi-Annually |
|
Semi-Annually |
|
|
Semi-Annually |
|
Blower assembly |
|
Semi-Annually and As Needed |
|
Quarterly |
|
|
Quarterly |
|
|
Annually |
|
|
Annually |
|
Compressor |
|
Annually |
Reversing valve |
|
Quarterly |
Two-way valves (when equipped) |
|
Annually |
Filter |
|
Quarterly and As Needed |
Water-to-refrigerant heat exchanger (if open-loop system without intermediate heat exchanger) |
|
If water flow is restricted through heat exchanger |
Unit controls |
|
Annually |
|
Annually |
|
Ductwork |
|
Annually |
Circulating Equipment |
||
Pump |
|
Weekly |
|
Quarterly |
|
|
Semi-Annually |
|
|
Annually |
|
|
Semi-Annually |
|
|
Semi-Annually |
|
|
Semi-Annually |
|
|
Annually |
|
Plate-and-frame heat exchanger (open-loop) |
|
Weekly |
|
Semi-Annually |
|
System controls |
|
Annually |
GCHX |
||
GCHX loop |
|
Annually |
|
Annually |
|
|
Annually |
|
|
Quarterly |
|
Closed-loop GCHX |
|
Quarterly |
Open-loop GCHX |
|
Weekly |
|
Quarterly |
|
|
Annually |
|
|
Annually |
|
|
Quarterly |
|
|
Quarterly |
|
|
Quarterly |
|
|
Quarterly |
|
Quarterly |
||
|
Quarterly |
|
|
Whenever submersible pump or injection pipe is removed |
Performance Monitoring (Measurement and Verification)
Monitoring the performance of GSHP systems is important to make sure proper operation and cost savings as well as for reporting purposes (when required). Individual unit performance must be assessed to determine overall system performance. Unfortunately, GSHP systems do not generally have associated monitoring equipment because of the complexity, cost, and accessibility challenges of installing and monitoring sensors and thermostats on all components. Instead, complaints about discomfort from building occupants can indicate possible performance problems with a unit or the system and should be addressed immediately.
To measure individual unit performance, the following steps are required (Hamton 2011):
- To make sure proper operation, a GSHP should be checked in both heating and cooling modes of operation using appropriate tools. To check performance temperature, pressure and flow measurements are required. The resulting heat of extraction/rejection is calculated using the unit’s water flow rate, the temperature difference between the water entering and the water leaving, and the fluid factor. The resulting heat of extraction/rejection can be used to measure the performance of the heat pump by referencing the manufacturer’s specification book.
- The sensible heat/cooling of the unit can be calculated using the unit’s air flow rate and the temperature difference between the air entering the unit and the air leaving the unit. The calculated sensible heat/cooling can be compared to the manufacturer’s specification to determine unit performance.
- Electrical measurements should be taken and compared to the manufacturer’s specification to determine proper equipment operation and indicate component wear.
- To make sure appropriate freeze protection and correct evaluation of the system performance, the concentration of antifreeze in the system should be checked. O&M Cost Generally, GSHP systems have lower O&M costs than conventional (chiller, boiler, and air handling) systems. The indoor units are similar in complexity to split systems (air handling units with condensing units) or package rooftop units. The more complex maintenance necessary for a chiller or boiler is not required unless a boiler or cooling tower is included as a component of a hybrid system. The National Renewable Energy Lab (NREL) found that O&M costs for GSHP are $109 +/- $94 per ton (NREL, 2016).
O&M Cost
Generally, GSHP systems have lower O&M costs than conventional (chiller, boiler, and air handling) systems. The indoor units are similar in complexity to split systems (air handling units with condensing units) or package rooftop units. The more complex maintenance necessary for a chiller or boiler is not required unless a boiler or cooling tower is included as a component of a hybrid system. The National Renewable Energy Lab (NREL) found that O&M costs for GSHP are $109 +/- $94 per ton (NREL, 2016).
Additional Support
FEMP28 Renewable Energy Technologies Applications – Geothermal Energy Technologies is a one hour online course that addressing how geothermal energy technologies (including GSHPs) can help federal sites meet agency goals and legislative mandates, improve energy security, and reduce environmental impact while efficiently providing electricity, heating, cooling, and other applications (WBDG, 2016). This includes an overview of how a heat pump system transfers heat, system benefits, system limitations, and a section on system maintenance. The webinar is available at http://www.wbdg.org/education/femp28.php.
Sources of Information
ANSI/ASHRAE/ACCA Standard 180-2012. Standard Practice for Inspection and Maintenance of Commercial Building HVAC Systems. American National Standards Institute, New York, NY. https://www.ashrae.org/technical-resources/bookstore/standards-180-and-211
EERE – Office of Energy Efficiency and Renewable Energy. 2010. Analysis of Energy, Environmental and Life Cycle Cost Reduction Potential of Ground Source Heat Pump (GSHP) in Hot and Humid Climate. Principal Investigator: Y.-X. Tao, Florida International University. Presented at USDOE Geothermal Technologies Program 2010 Peer Review. U.S. Department of Energy, Office of Energy Efficiency and Renewable Energy, Washington, DC https://www1.eere.energy.gov/geothermal/pdfs/peer_review_2010/gshp_tao_cost_reduction.pdf
EERE – Office of Energy Efficiency and Renewable Energy. (n.d.). Operating and Maintaining Your Heat Pump. U.S. Department of Energy, Office of Energy Efficiency and Renewable Energy, Washington, DC. http://energy.gov/energysaver/operating-and-maintaining-your-heat-pump.
FEMP – Federal Energy Management Program. 2001. Ground-Source Heat Pumps Applied to Federal Facilities–Second Edition. DOE/EE-0245, PNNL-13534, U.S. Department of Energy, Federal Energy Management Program, Washington, D.C. https://www.pnnl.gov/main/publications/external/technical_reports/pnnl-13534.pdf FEMP – Federal Energy Management Program. 2010. O&M Best Practices Guide, Release 3.0, Chapter 9, O&M Ideas for Major Equipment Types, section 9.9, Pumps. U.S. Department of Energy, Federal Energy Management Program, Washington, D.C. https://www1.eere.energy.gov/femp/pdfs/om_9.pdf
Hamton, Sonny. 2011. 10 Steps to Servicing a Geothermal Heat Pump. Contracting Business.com. https://www.contractingbusiness.com/service/article/20865480/10-steps-to-servicing-a-geothermal-heat-pump
International Ground Source Heat Pump Association. https://igshpa.org/. NREL – National Renewable Energy Lab. 2016. Distributed Generation Renewable Energy Estimate of Costs. Accessed January 2020 at https://www.nrel.gov/analysis/tech-lcoe-re-cost-est.html
WBDG – Whole Building Design Guide. 2010. Ground Source Heat Pumps. National Institute of Building Sciences, Washington, DC. https://www.wbdg.org/FFC/ARMYCOE/TECHNOTE/technote18.pdf .
WBDG – Whole Building Design Guide. 2016. FEMP28 Renewable Energy Technologies Applications – Geothermal Energy Technologies. National Institute of Building Sciences, Washington, DC. http://www.wbdg.org/education/femp28.php.
Actions and activities recommended in this Best Practice should only be attempted by trained and certified personnel. If such personnel are not available, the actions recommended here should not be initiated.
Published May 2021