- Best Practices for Equipment O&M
-
O&M Best Practice Issue Discussions
- Advanced Maintenance Approach: Reliability Centered Maintenance
- Applying Key Performance Indicators
- Comprehensive O&M Program
- Contract Challenges and Improvements
- Cybersecurity for O&M Systems
- Existing Building Commissioning Procurement
- Healthy Building O&M
- Integrating and Analyzing Building Information to Support O&M
- Maintenance Approaches
- OMETA: An Integrated Approach to Operations, Maintenance, Engineering, Training, and Administration
- Prioritizing O&M Actions
- Re-tuning Buildings
- Tools
- Glossary
Best Practices for Modular Boilers Operations and Maintenance
Table of Contents
- Introduction
- Description of Technology
- Key Components
- Safety Issues
- Maintenance of Technology
- Maintenance Checklist
- Performance Monitoring
- O&M Cost
- Additional Support
- Sources of Information
Introduction
Modular boilers can improve the efficiency of heating and steam systems compared to large conventional boilers sized to meet large loads. Regular operations and maintenance (O&M) of modular boiler systems will assure that they continue to operate effectively. In addition, performance monitoring will help identify potential issues with the system and achieve maximum savings. Fortunately, most modular boiler systems include performance monitoring information in the system controllers that can facilitate system diagnostics. Energy production can typically be reviewed from system controllers, therefore assuring that proper programming and continued function of the system controller are essential parts of O&M.
The purpose of this equipment O&M Best Practice is to provide general information about the key components of modular boiler systems and to familiarize the designated staff member with the types and frequency of maintenance typically performed to keep a modular boiler system in good working order.
Description of Technology
A modular boiler system is a water heating technology that can provide hot water or steam for space heating and/or process energy for buildings. What differentiates modular boiler systems from conventional boilers is that these systems are smaller packaged units that operate together in parallel to provide varying amounts of heat (via water or steam) to best match system load. Each modular boiler provides a percentage of the system’s heating capacity, and additional units can be added to increase capacity. A programmed controller coordinates the number of boilers needed to meet real-time facility demands. This allows each modular boiler to be cycled on (also referred to as firing) only when needed (minimizing run time) and operating most efficiently at full or near-full capacity. In contrast, conventional boilers are often sized to satisfy large loads (e.g., whole buildings in cold weather), and when facility demands do not require the full heating capacity, efficiency is sacrificed as the larger conventional boiler is throttled down.
Firing boilers independently allows a modular boiler system to efficiently satisfy the building heating load fluctuations in year-round outdoor temperatures. Conversely, a traditional boiler may typically run at near-full capacity during winter months with a large heating load requirement, but then operate at a consistently lower efficiency for the remainder of the year when operating under part-load conditions. Figure 1 is a diagram of modular boilers firing to meet different heating load requirements due to variations in ambient weather.
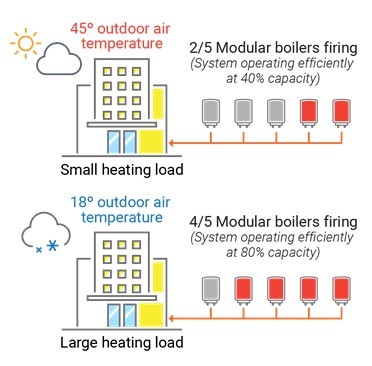
Boilers are typically classified by their intended function, the fuel source, construction, configuration, and final product (water or steam), but can more broadly be classified as conventional, condensing, and/or modular.
- Conventional boilers use fossil fuel (natural gas, oil, or coal) for combustion to heat water or create steam. They can also use wood for the combustion process. Electric boilers are also available.
- Condensing boilers are fueled by oil or gas. Condensing boilers gain their efficiency by condensing the water vapor in flue gas and recovering the associated energy that would otherwise have been exhausted. This increases system efficiency, resulting in higher-efficiency operation than conventional boilers.
- Modular boilers are smaller units that work in tandem. Two or more modular boilers are connected to meet a fluctuating or partial heating demand. They can be either (1) conventional and used in high-temperature systems, (2) condensing and used in low-temperature systems, or (3) mixed (e.g., two conventional, two condensing) in a hybrid system, depending on design needs. A system controller monitors the temperature of the water circulating through the system, outside air temperature, and building heating demand and fires boiler modules just enough to meet the demand or turns off modules as demand decreases. An important distinction is that the controls for individual modular boilers may be on/off (cycling) or modulating (adjusting the output to match demand) controls. Either control results in higher efficiency through decreased cycling and optimized efficiency compared to single boiler applications.
An inherent benefit of modular boilers is that technicians can perform required maintenance activities at any time during the heating season on boilers not being used while keeping the larger system operating. This same feature enhances overall system resilience, allowing the building or process to continue operating despite a failure.
Key Components
A modular boiler system is a collection of boilers that work together. Each module can be a separate boiler and is capable of running independently of the others. Also, modular boilers are designed to work in conjunction with one another. The boiler modules can be installed alongside one another in a horizontal arrangement or as a vertical stack of boiler modules one above another.
The differentiating component that allows modular boilers to function properly as a collection of boilers is the system controller. The controller for a multiple-boiler system enables the modulating boilers to be operated such that they modulate together to match the load. The controller can optimize the system operation by firing the optimal number of boilers needed to match the load with each operating at or near its most efficient state.
Several types of system controllers are available. One type is a stand-alone controller that can operate the boilers using its internal program. Another type can be integrated into a building automation system (BAS). This type of controller receives the required operating temperature control point from the BAS and then operates only as a boiler sequence controller.
Modular boiler system controllers can be configured to sequence boilers in either cascade mode or unison mode. Cascade control initiates a boiler operation at its lowest heating rate, modulates it to its maximum rate, and then starts the next boiler to meet the system load. This method operates the minimum number of boilers to satisfy the load requirements. Cascade control is used for systems where there is no significant advantage to operating boilers at part load. This strategy is often applied to non-condensing boilers, providing constant-temperature hot water or constant-pressure steam.
In contrast, unison control takes advantage of the higher part-load efficiencies available at low boiler heating rates. Unison control initiates boiler operation at its lowest rate. If the load requires additional heat, the controller enables additional boilers at their lowest rate and then, if needed, modulates the boilers to higher rates to match the system requirements. The unison control strategy is well suited for operating condensing boilers in variable-temperature systems or systems with variable loads.
In both cases, boiler control can include a lead/lag control status. Lead/lag control of modular boilers involves the designation of a single boiler to serve as the starting boiler upon a call for heat—this is the lead boiler. A second (lag) boiler, as well as additional boilers, will be enabled as required. The boiler controller will then rotate the designation of lead/lag status based on operating hours. From an O&M perspective, proper lead/lag control results in not only efficient system operation, but also equal wear, less cycling, and less stress on the boiler and system components.
Figure 2 shows a simplified schematic of a hydronic modular boiler system, and Figure 3 is a picture of modular boilers in a boiler room.
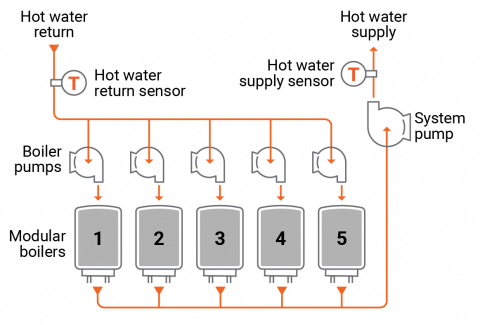
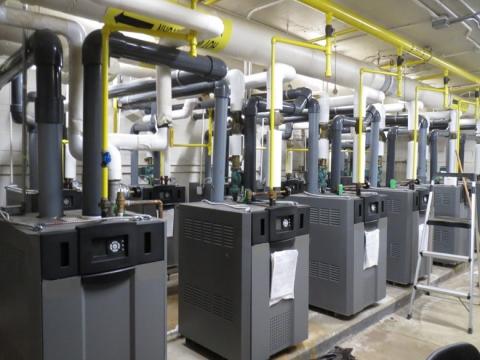
Safety Issues
Boiler systems require knowledgeable and experienced personnel for maintenance, diagnostics, and service. Standard electrical, mechanical, and other safety practices apply to these systems. High temperatures and pressures are present in all boiler systems, and high voltage is present in electric boilers.
Maintenance of Technology
Keeping modular boiler systems properly maintained through preventive maintenance will minimize overall O&M requirements, improve system performance, and protect the asset. Follow the guidelines in the equipment manufacturer’s maintenance manuals, and check the specific warranty details for your installed system. Warranties for modular boilers in commercial applications generally have a standard limited 1-year warranty that covers defective components, and hydronic systems can include an additional 4–9 years of warranty on heat exchangers.
Modular boiler systems require standard maintenance (refer to FEMP O&M Best Practices Guide, Section 9.2, Boilers, available at https://www1.eere.energy.gov/femp/pdfs/om_9.pdf).
In addition to general boiler maintenance, maintenance specific to modular boilers includes assessing and optimizing controller sequences (e.g., lead/lag status and rotation) for fuel-firing conditions, proper cycling and cascading of modules, and optimizing temperature and/or steam pressure in boilers and piping configurations. Piping configurations can be more complex when using multiple small boilers instead of one larger boiler—maintenance must therefore include measuring pressure and temperature parameters throughout the piping system as well as assuring any pumps associated with individual modules are maintained.
It is important that all staff members assigned to managing boiler system O&M keep good maintenance records and logs of all services performed, preferably in electronic form in a Computerized Maintenance Management System (CMMS). This record should include controller alarms, corrective actions taken, equipment down time, and other relevant issues noted and resolved. This will help identify recurring warranty issues or systemic problems and assure that warranties remain valid. All work orders related to the boilers should be recorded.
Boiler components should be included under a periodic evaluation process with prioritization and consideration given to equipment life, repair and maintenance history, and criticality of system operation.
In cases where the modular boilers support critical systems or buildings, consider additional monitoring of the boiler performance to identify pending performance and condition degradation and even the onset of failure. Predictive maintenance technologies, such as infrared thermography, can be used to assess boiler and system insulation issues and identify leakage. In addition, identify and stock the site’s parts inventory with the spare parts and components necessary to assure that the modular boilers can be repaired in a timely manner.
Maintenance Checklist
For all equipment maintenance, follow the manufacturer’s instructions. Proper maintenance of these systems is extensive and should only be performed by qualified personnel with previous boiler O&M experience and training. Maintenance should address safety as well as system operation. Maintenance tasks for individual boilers should be performed (e.g., check flue temperature, inspect safety elements) to verify component conditions and operating temperatures, pressures, and flows are within manufacturer and design parameters. Additionally, maintenance for the modular configuration is required to continue safe and optimal operation.
Below is a modular boiler system sample checklist that includes general and maintenance tasks for the individual boilers. Consult the manufacturer’s information for acceptable operating parameters.
Description | Comments |
Maintenance Frequency |
|||
---|---|---|---|---|---|
Daily | Weekly | Monthly | Annually | ||
Boiler use/sequencing |
Verify that the central controller turns off unnecessary boilers and is enabling boilers following the desired sequence and lead/lag control. |
X | |||
Overall visual inspection |
Complete overall visual inspection to be sure all equipment is operating and safety systems are in place. Verify all systems are clean and free of debris and obstructions, especially exhaust/vent terminations. |
X |
|||
Check water temperatures |
Compare temperatures with tests performed after annual cleaning |
X |
|||
Check steam pressure (if applicable) |
Is variation in steam pressure as expected under different loads? |
X |
|||
Check air temperatures in boiler room |
Temperatures should not exceed or drop below design limits. |
X |
|||
Check boiler water treatment |
Confirm water treatment system is functioning properly. |
X |
|||
Inspect system for water/steam leaks and leakage opportunities |
Look for leaks, defective valves and traps, corroded piping, and condition of insulation |
|
X | ||
Combustion air supply (if applicable) |
Check combustion air inlet to boiler room to make sure openings are adequate and clean |
|
X | ||
Modular controller, including input and output devices |
Verify control strategies including hot water reset, if applicable. Inspect all sensors, safety devices, and other devices that provide inputs to the modular controller. If applicable, inspect all devices (other than boilers) receiving output from the modular controller (valves, pump contactors, etc.) |
|
X | ||
Perform water quality test |
Check water quality for proper chemical balance. |
|
X | ||
Electrical systems |
Clean all electrical terminals. Check electronic controls and replace any defective parts. |
|
X | ||
Other components/systems |
Perform appropriate inspections and maintenance of other components and systems, including, but not limited to, pump assemblies, variable frequency drives, fuel systems, and feedwater systems. |
|
X | ||
Document all maintenance activities in logbook or electronic CMMS. |
Upon activity completion |
Performance Monitoring
Monitoring the performance of modular boiler systems is important to assure proper operation and cost savings. Individual unit performance must be assessed to determine overall system performance. The central controller should be capable of providing general information on individual unit performance. However, the controller may not provide all information needed to monitor all the boilers. Insights from the controller should also be verified with measurements and observations of the system.
To monitor individual unit performance, the following steps are recommended:
- Controller-based
- Assess the firing rate of individual modules. If modules are meant to alternate as the lead boiler, assure that accumulated firing hours are within a reasonable consistency range across all modules.
- Physical component-based
- Physical gauges in the system should be compared to measurements taken by the controllers, and discrepancies should be investigated. Calibration may be needed.
- Water treatment
- Record water quality through the system (feed water, concentration in blowdown water, and acidity of the condensate water) and assure that the water characteristics are within operating parameters according to manufacturer specifications.
- Metering
- Fuel input should be metered for the entire boiler system and ideally for each individual module. The controller may provide trending capabilities to monitor fuel input.
- For steam systems, steam output should be metered to verify efficiencies.
- Make-up water to the system should be metered to allow for water use trending and leak detection.
- All personnel should report any noticed leaks or damaged insulation. Repairing leaks should contribute to a measurable reduction of make-up water.
O&M Cost
When considering the costs over the entire life cycle of a steam boiler, fuel accounts for roughly 96% of costs, while capital may represent roughly 3% and O&M the other 1%.[1] Given the high percentage of costs associated with fuel, proper O&M assures that system efficiency is maintained and keeps fuel consumption low.
Modular boiler systems require preventive maintenance as well as other periodic checks. The O&M costs vary significantly depending on equipment type, maintenance plan, scope of work, and geographical location.
Additional Support
The Boiler Efficiency Institute provides O&M manuals for boilers and boiler control systems. To encourage quality O&M, building engineers can also refer to ASHRAE/ACCA Standard 180, Standard Practice for Inspection and Maintenance of Commercial Building HVAC Systems. The Whole Building Design Guide provides operations checklists and design considerations specific to agencies. In addition, the FEMP O&M Best Practices Guide, Release 3.0, Chapter 9 provides valuable information on O&M of boiler systems.
Sources of Information
FEMP (Federal Energy Management Program). 2010. O&M Best Practices Guide, Release 3.0, Chapter 9, O&M Ideas for Major Equipment Types, Section 9.9, Pumps. U.S. Department of Energy, Federal Energy Management Program, Washington, D.C. https://www1.eere.energy.gov/femp/pdfs/om_9.pdf.
IEA (International Energy Agency). 2010. Energy Technology Systems Analysis Programme (ETSAP) Industrial Combustion Boilers. IEA ETSAP - Technology Brief I01 – May 2010. https://iea-etsap.org/E-TechDS/PDF/I01-ind_boilers-GS-AD-gct.pdf
[1] https://iea-etsap.org/E-TechDS/PDF/I01-ind_boilers-GS-AD-gct.pdf
Actions and activities recommended in this Best Practice should only be attempted by trained and certified personnel. If such personnel are not available, the actions recommended here should not be initiated.
Published April 2021