- Best Practices for Equipment O&M
-
O&M Best Practice Issue Discussions
- Advanced Maintenance Approach: Reliability Centered Maintenance
- Applying Key Performance Indicators
- Comprehensive O&M Program
- Contract Challenges and Improvements
- Cybersecurity for O&M Systems
- Existing Building Commissioning Procurement
- Healthy Building O&M
- Integrating and Analyzing Building Information to Support O&M
- Maintenance Approaches
- OMETA: An Integrated Approach to Operations, Maintenance, Engineering, Training, and Administration
- Prioritizing O&M Actions
- Re-tuning Buildings
- Tools
- Glossary
Solar Water Heating Systems
Table of Contents
- Introduction
- Description of Technology
- Key Components
- Safety Issues
- Maintenance of Technology
- Maintenance Checklist
- Performance Monitoring
- O&M Cost
- Additional Support
- Definitions
- Sources of Information
Introduction
Solar water heating (SWH) systems use energy from the sun to generate heat that can then be used to heat water for domestic hot water needs, space heating, industrial processes, or pool heating. They are a reliable and cost-effective technology that can help reduce utility bills for homes and businesses.
The operation and maintenance (O&M) of SWH systems is almost identical to those for other types of hydronic heating systems and involve the same types of components. The systems are designed with automatic controls to operate without intervention, but it is important to keep an eye on their performance, provide preventive maintenance, and quickly repair failures to avoid lost production.
The purpose of this Best Practice is to provide an overview of the system components and the requirements for maintaining SWH systems to keep them operating safely and efficiently. Small SWH systems do not include performance-monitoring equipment (typical of solar photovoltaic systems), which means that the energy production and system operation are often not tracked. Regular O&M of SWH systems ensures that issues are identified early and systems continue to operate effectively. Organizations should budget and plan for regular maintenance to ensure continuous operation.
Description of Technology
SWH systems harvest solar radiation to heat water. The most common SWH applications are for domestic water heating (the focus of this document), pool heating, and heating for high-temperature applications. There are two types of SWH systems:
- Active systems – use circulating pumps to pump either water or a heat transfer fluid through the collectors. Although more expensive than passive systems, they are typically more efficient.
- Passive systems – do not use a pump to circulate water from the collector to the storage tank or other locations. Instead, they rely on gravity and/or the thermosiphon properties of fluids to circulate the water. These systems are less expensive than an active system but not as effective and not suitable in climates where temperatures fall below freezing.
The most common type of system for use in commercial and residential buildings is an active system. SWH for domestic applications typically uses roof-mounted collectors that harvest the sun’s energy to either directly or indirectly heat potable water. The heat transfer fluid (potable water in direct systems or an antifreeze solution in indirect systems) is piped to a storage tank, which in indirect systems contains a heat exchanger. As the temperature in the storage tank decreases, the heat transfer fluid is recirculated through the warm collectors. However, SWH systems usually cannot produce 100% of the water heating needed at the time of demand, so a backup heat source is also required. Finally, potable water in the SWH storage tank and the backup water heater is piped to domestic end uses.
Key Components
The key elements of SWH systems include solar collectors, a storage tank, heat transfer fluid, a backup water heater, pipes, controls, and valves. Pressure relief valves are on any tanks or solar collectors that can be valved off; and air vents at high points in the piping allow air to escape. Additional components can include a heat exchanger, pump, and/or expansion tank. These are briefly summarized below and are also shown in Figure 1.
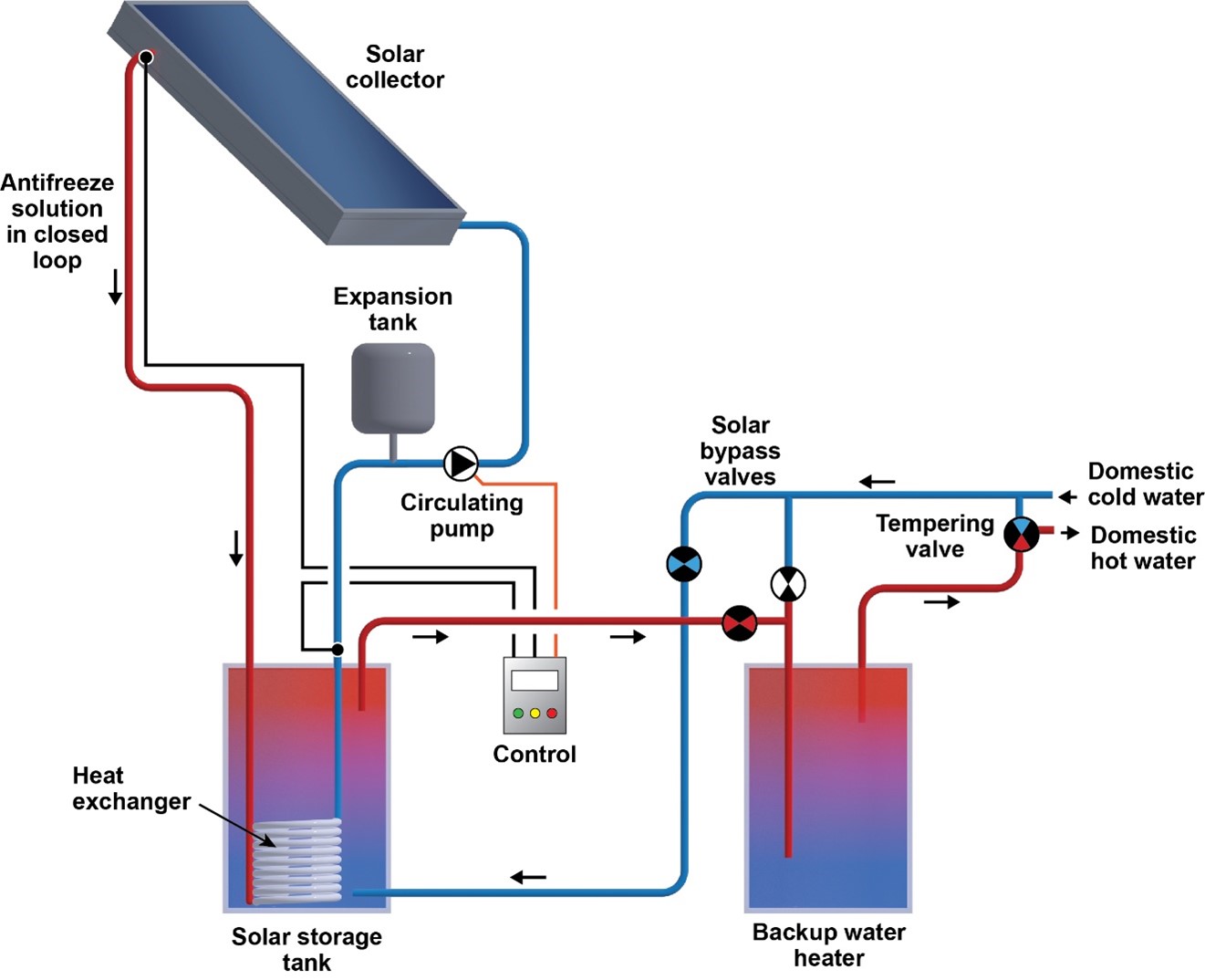
- SWH collectors – These collect and focus solar energy on tubes that contain a circulating heat transfer fluid. There are five major types of SWH collectors to serve the primary applications listed above: flat-plate collectors (glazed and unglazed), evacuated tube collectors, parabolic-trough collectors, integral collector storage systems, and thermosiphon systems.
- Flat-plate collectors convert the radiant solar energy to heat energy for hot water applications. The collectors can be either glazed or unglazed.
- Glazed, flat-plate collectors (Figure 2), for domestic water heating, consist of serpentine copper pipes encased in glass with black sunlight-absorbing material above the pipes and insulation below. A metal frame holds these layers together and adds rigidity to the collector.
- Unglazed, flat-plate collectors (Figure 3), typically used for pool heating applications, consist of serpentine polyvinyl chloride (PVC) pipes surrounded by rubber or plastic treated with ultraviolet light protection.
- Evacuated tube collectors (Figure 4), for high-temperature or cold climate applications, consist of copper pipes, usually surrounded by black sunlight absorber plates, encased in an evacuated glass tube. Several tubes are connected to a manifold to create a complete collector.
- Parabolic-trough collectors (Figure 5), for high-temperature or large applications, use curved mirrors or highly polished material to focus the sunlight on a receiver tube that runs through the focus line of the parabola. Because they use direct sunlight only, the parabolic-trough collectors require tracking systems to keep them focused toward the sun and are best suited for areas with high solar radiation.
- Integral collector storage systems (Figure 6), also called batch systems, have storage tanks or tubes inside an insulated, glazed box. The hot water from the collector flows to a backup water heater, thus preheating the domestic water. This is a passive system that cannot be used in colder climates.
- Thermosiphon systems (Figure 7), a type of passive SWH system, consist of a separate storage tank directly above the collector. The water is heated in the collector and rises to the tank, while the cool water sinks back into the collector due to a change in density.
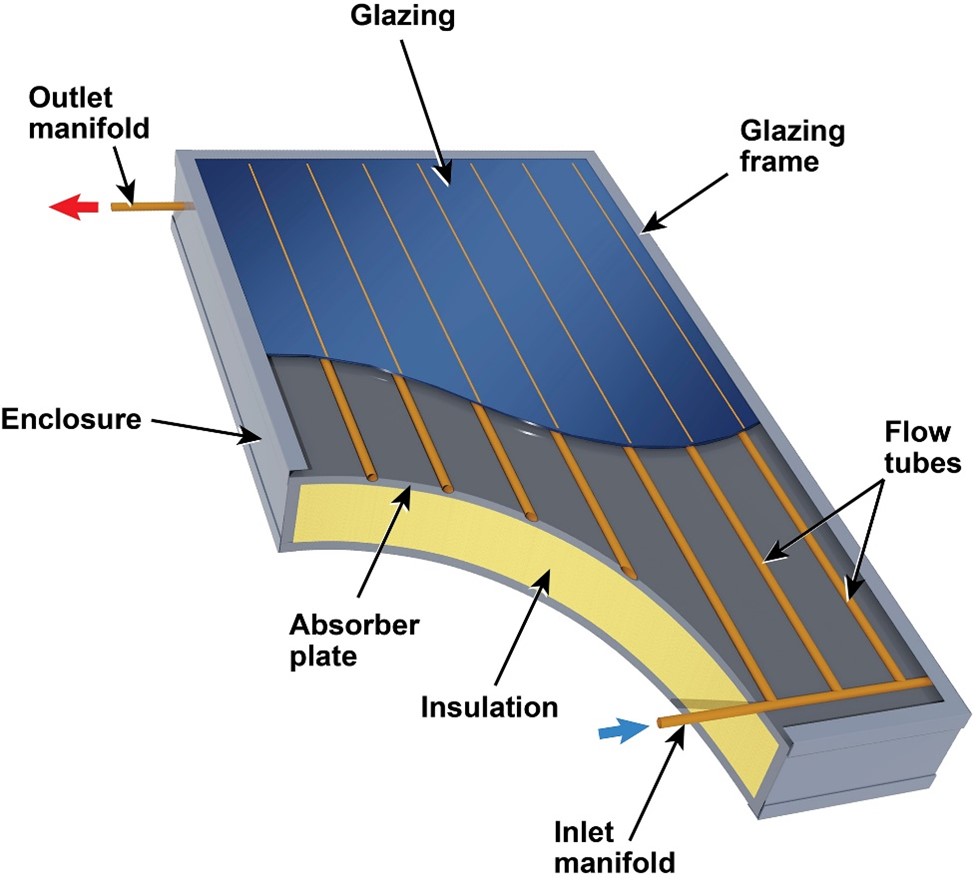
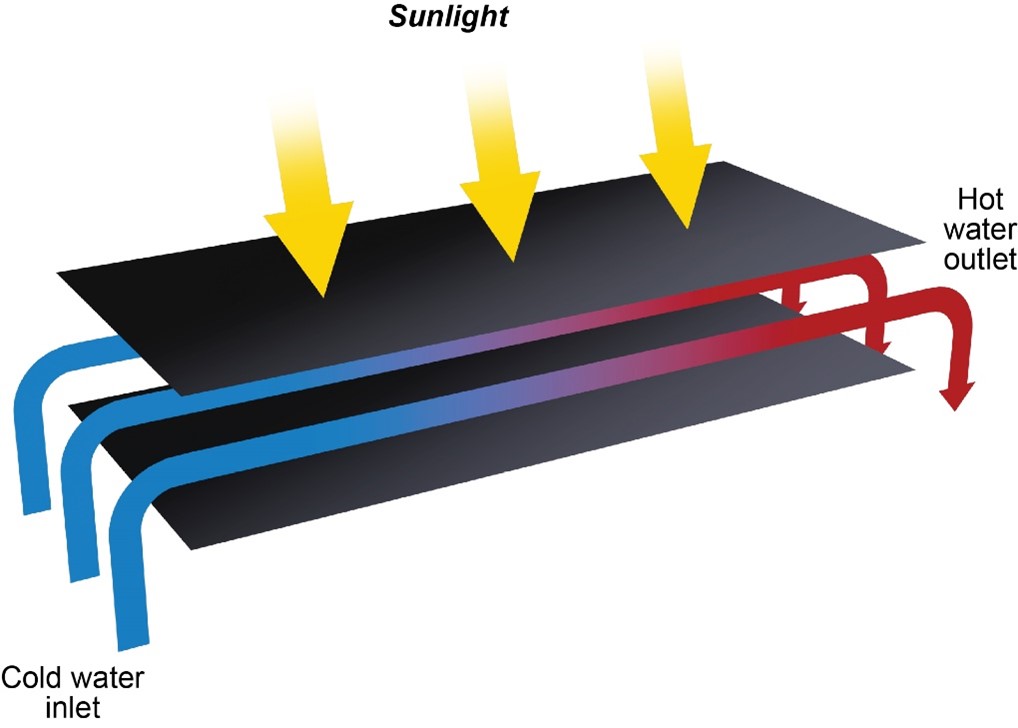
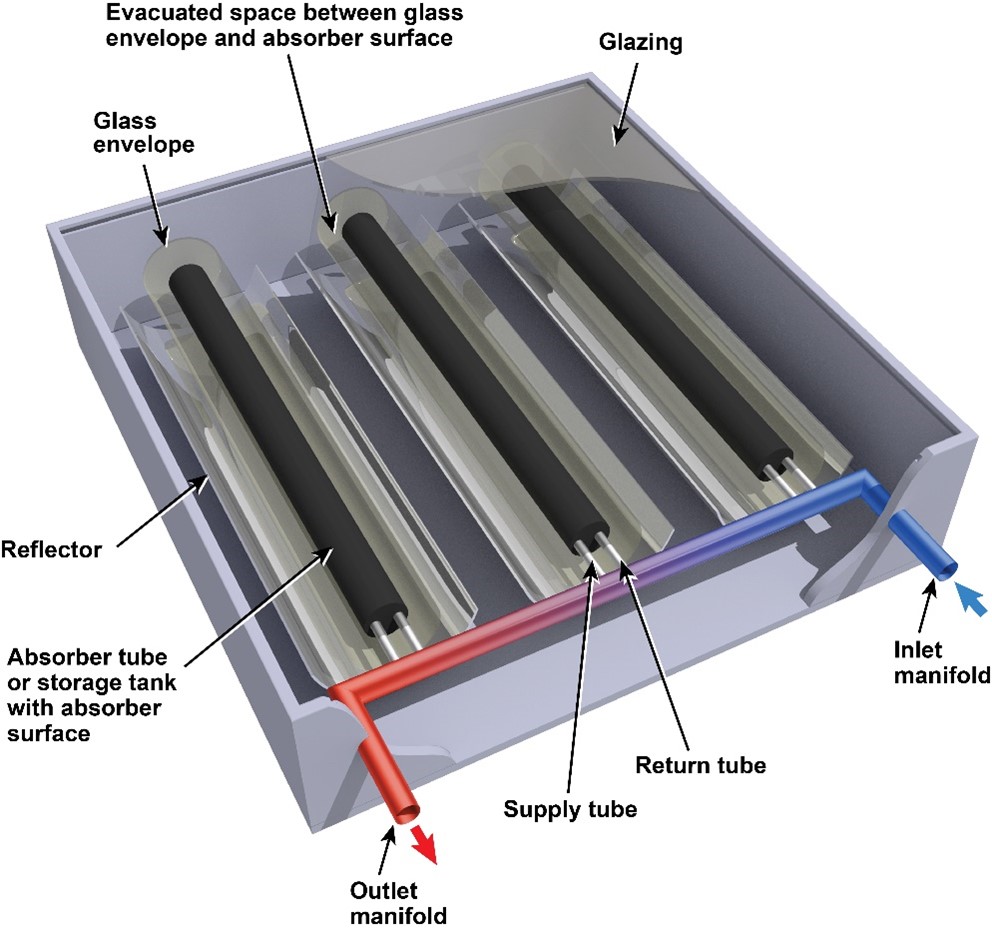
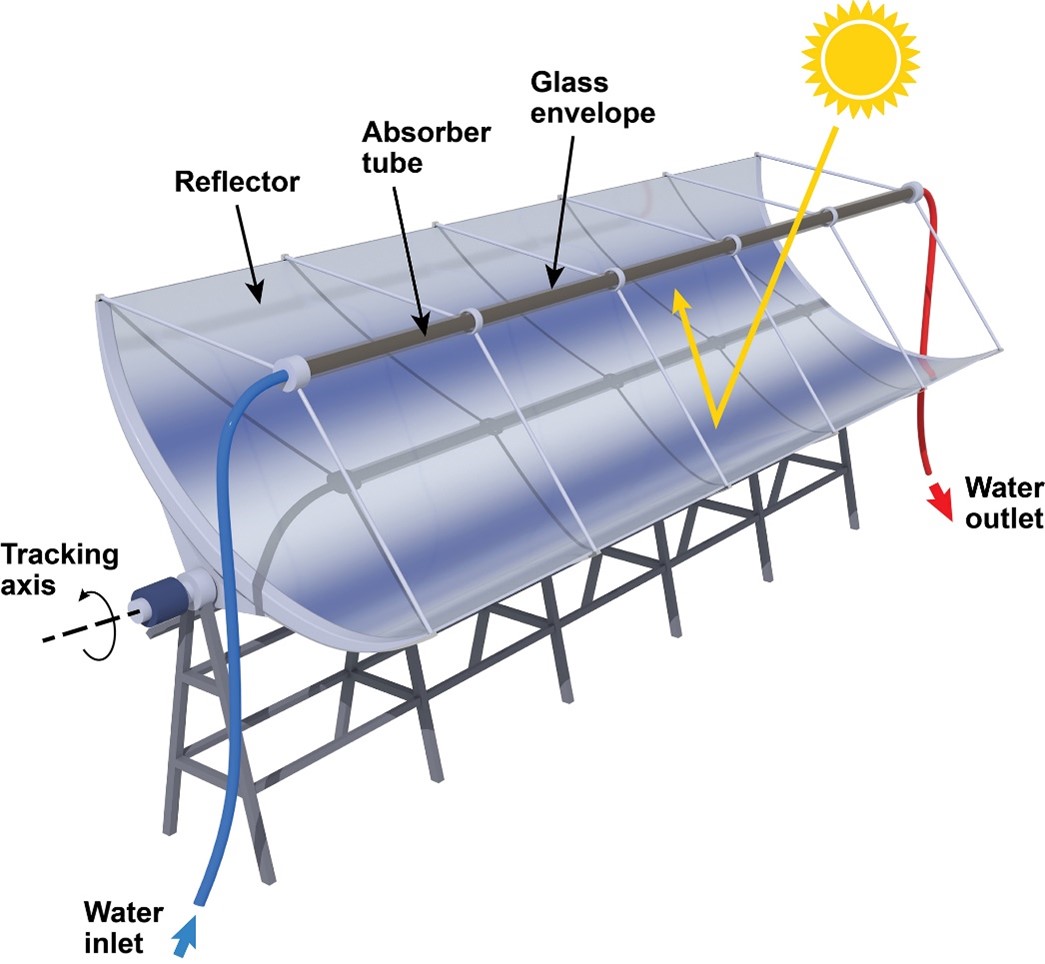
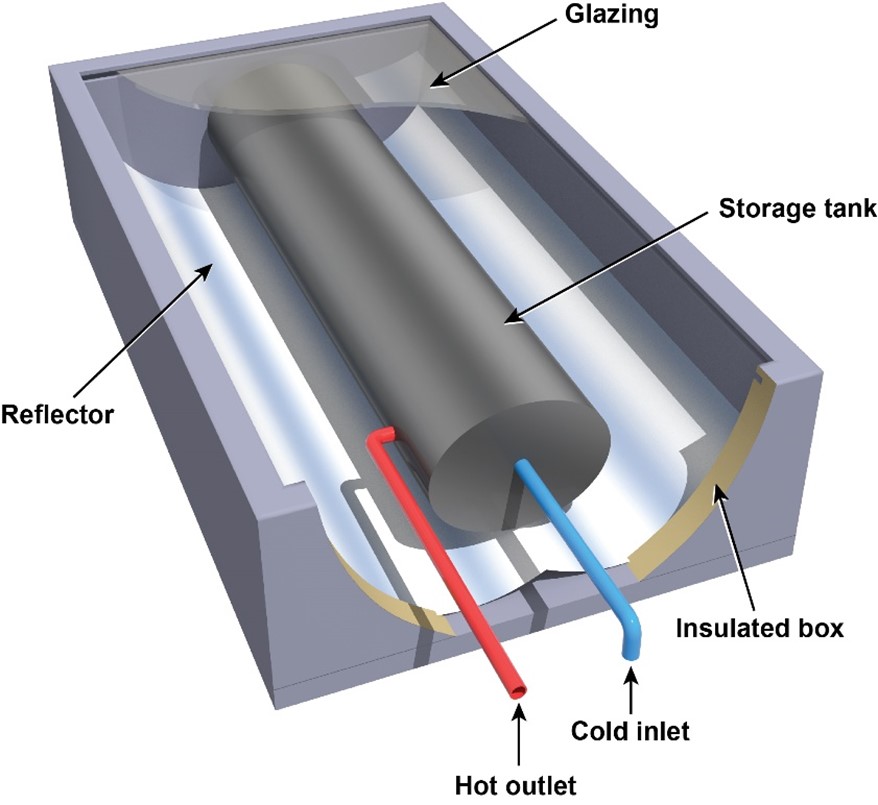
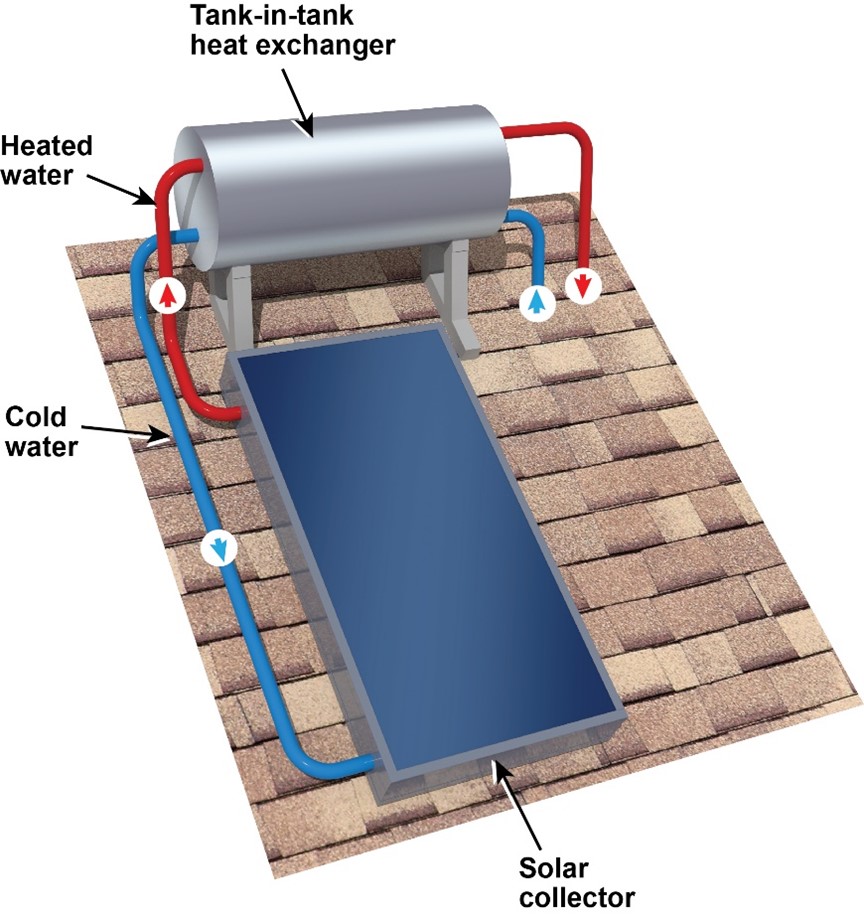
- Heat transfer fluid – The heat transfer fluid is either potable water in the case of direct systems or an antifreeze solution in the case of indirect systems. Locations that experience freezing temperatures must either use antifreeze or shut down and evacuate the system in the winter, so indirect systems are very common in such climates. Antifreeze solutions can use either propylene glycol or ethylene glycol. Ethylene glycol is toxic. Propylene glycol has been classified as an additive that is “generally recognized as safe” for use in food by the Food and Drug Administration. Consequently, propylene glycol and water compose the most common antifreeze solution in solar hot water systems.
- Storage tank – A storage tank stores water heated by the SWH collectors. The storage tank may contain a heat exchanger and/or backup water heating capability. The tank is sized according to the amount and timing of peak hot water consumption compared to SWH production capabilities. It is preferable to have a separate solar storage tank to preheat water prior to the conventional heater; systems that only have one tank have to rely on stratification within that tank to avoid sending already-heated water to the solar array.
- Heat exchanger – Indirect SWH systems use heat exchangers to transfer heat from the antifreeze solution that absorbs heat inside collectors to potable water without mixing the two fluids. Heat exchangers can be external, with inputs and outputs for both the antifreeze solution and water, or they may be incorporated within the storage tank, with the antifreeze solution running through the heat exchanger pipes inside the tank and the potable water circulating freely around it.
- Backup water heater – The backup water heater can be an existing water heater in a retrofit application or a new water heater that is sized to supplement the SWH system during peak consumption or low insolation periods, rather than providing the full hot water load. Backup water heaters can use any fuel that a site typically uses for water heating and can be an on-demand water heater, have a tank, or be integrated into the storage tank as mentioned above.
- Pump – Active SWH systems use a pump to move the heat transfer fluid through the pipes, collectors, and storage tank. Most active systems use a pump station that is attached to and/or integrated into the storage tank. The pump station typically also includes gauges that display system temperatures and pressure.
- Expansion tank – Most domestic SWH systems are pressurized, so an expansion tank is necessary to relieve high pressures resulting from heated fluids. The most robust systems also use expansion tanks for the “pressure stagnation method” to protect systems from overheating and from antifreeze stagnation. When there is no need for water heating, sunny conditions may overheat the antifreeze, turning it acidic and damaging the collectors. To prevent this, the water in the antifreeze flashes to steam at a certain temperature and pushes all the fluid out of the collectors into an expansion tank. When more hot water is needed, the temperature drops, the steam condenses to liquid, and the expansion tank releases the fluid to resume operation.
- Sensors and controls – Active SWH systems use sensors to determine the temperature of the water in the storage tank and the collectors. If the water temperature inside the storage tank is below the setpoint, a control system compares that temperature to the temperature inside the collectors. If the temperature is higher in the collector than in the tank, the control system turns on the pump to move fluid through the collectors and heat the water in the tank to the desired setpoint; it then turns the pump off. Passive systems typically have no controls and rely on the physical properties of fluids to rise when heated and fall when cooled to circulate the fluids between the storage tank and collectors.
- Pipes – Water or antifreeze solution moves through the pipes between the collectors, tank(s), and end uses. The pipes are usually made of copper between the collectors and storage tank and are typically PVC or cross-linked polyethylene (PEX) between the storage tank, backup water heater if applicable, and end uses.
- Valves – SWH systems use automated or manual valves to turn the system on and off or bypass the system. They also have a pressure relief valve for safety.
Figure 8 identifies SWH components in a mechanical room.
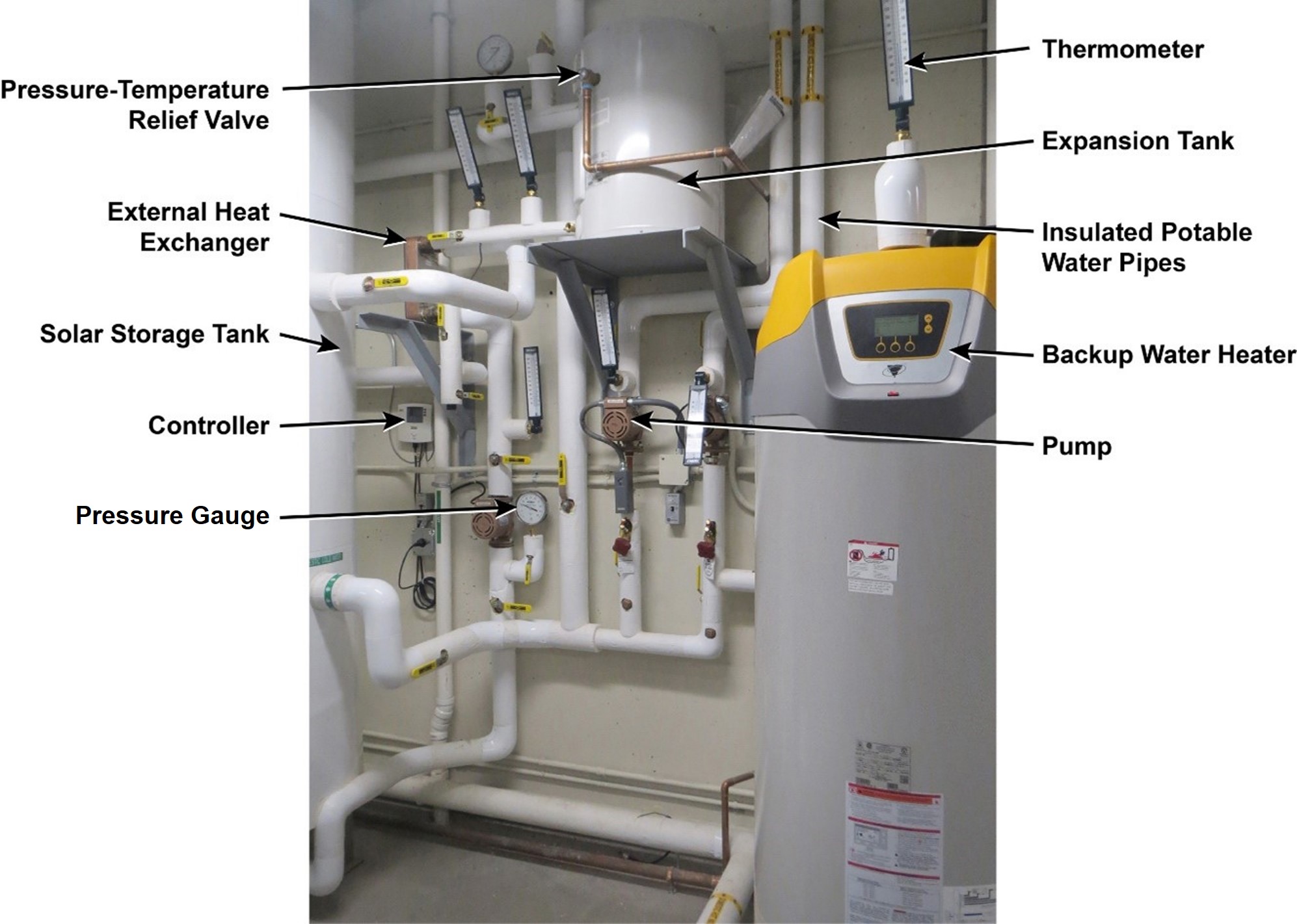
Safety Issues
SWH systems and associated components require knowledgeable and experienced personnel for maintenance, diagnostics, and any additional troubleshooting work. Standard electrical, mechanical, and other safety practices apply to these systems. Systems are typically pressurized and may contain very hot water, so only trained and authorized maintenance providers with approved safety gear should connect or disconnect pipes or system components. Some antifreeze solutions are toxic to humans and animals, so their disposal requires compliance with local regulations.
For units that have backup gas-fired water heaters, ensure that all safety procedures are followed. Undetected gas leaks can pose grave danger by causing a fire or an explosion. Ensure that the gas is shut off before doing any maintenance or troubleshooting work.
Maintenance of Technology
Keeping SWH systems properly maintained through preventive maintenance minimizes overall O&M requirements, improves system performance, and protects the asset. Manufacturer warranties typically cover the first 5 to 10 years for SWH collectors, the first 3 to 5 years for storage tanks, and the first 1 to 2 years for all other components.
SWH systems contain many moving parts that need to be checked weekly, monthly, quarterly, or annually. All systems use a working fluid, so inspection for leaks is vital, not only to ensure system operation but to avoid costly property damage as well. Connections between pipes and fittings are the most common points of failure, so it is important to check each fitting for leaks.
Typically, a trained and authorized heating, ventilation, and air conditioning professional performs the required equipment repairs. However, facility maintenance personnel and other approved on-site representatives can perform visual inspections and other routine checks, as well as document system issues. It is important that the staff member assigned to managing the system O&M keeps a good log of all servicing performed, preferably in electronic form in a Computer Maintenance Management System. This record should include servicing of controller alarms, conditions inhibiting performance, down time, and other relevant issues noted and resolved. Doing so helps identify recurring issues or systemic problems and ensures warranties remain valid. Work orders related to the SWH system also should be recorded.
As shown in Figure 9, a graph of the results of an early (1992) survey of 185 SWH systems in Colorado, many problems could be fixed with very little expense. An example is described as “Temp. Sensor Mount,” which indicates sensors that have simply fallen off the surface they are measuring.
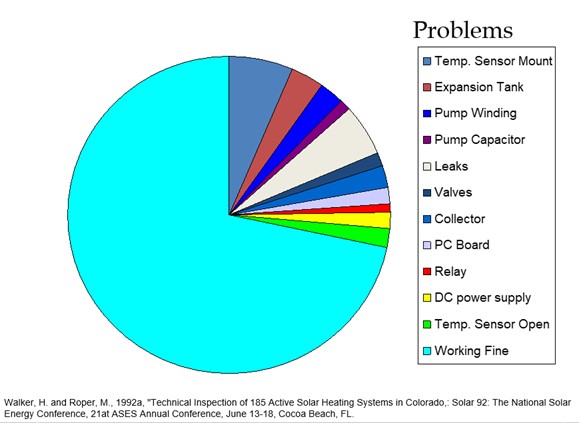
Maintenance Checklist
Table 1 presents a sample maintenance checklist. A site staff member or contractor can be designated to perform all of the listed tasks, but repairs should be performed by a trained and authorized contractor such as a plumber who has SWH experience. This checklist does not supersede maintenance recommendations from the equipment manufacturers, nor is it a replacement for contracted O&M or warranty services.
Table 1.
Component |
Action |
Maintenance Frequency |
|||||
Daily |
Weekly |
Monthly |
Quarterly |
Annually |
As |
||
General Inspection |
Perform an overall visual inspection to be sure all equipment is operating properly and safety systems are in place. |
X |
|
|
|
|
|
Inspect all roof and wall penetrations to ensure their integrity. |
|
|
X |
|
|
|
|
Inspect the system for signs of corrosion. |
|
|
X |
|
|
|
|
Inspect collectors, seals, pipes, and connections for signs of leakage. |
|
|
X |
|
|
|
|
Check for animal infestations. |
|
|
X |
|
|
|
|
Monitor ground erosion, if applicable. |
|
|
X |
|
|
|
|
SWH Collectors |
Ensure collectors remain unshaded. Remove any obstructions due to tree or vegetation growth, dust/dirt, or heavy ice accumulation. |
|
|
X |
|
|
|
Inspect collectors and frames for damage or deterioration. |
|
|
X |
|
|
|
|
Check for insecure mounts – ensure that collectors are firmly bolted and anchored. |
|
|
X |
|
|
|
|
As necessary, wash panels with a water-fed pole and scrub them with a brush and mild detergent, per the installer’s recommendation. |
|
|
|
|
|
X |
|
Drain direct systems before winter or when freezing temperatures are expected. |
|
|
|
|
|
X |
|
Check mirror surfaces for parabolic-trough collectors and clean them regularly to maintain their efficiency. |
X |
||||||
Equipment Controls |
Monitor the system controller screen for errors. |
X |
|||||
Check for malfunctioning controls (check thermometers to ensure the leaving fluid temperature from collectors is higher than the entering fluid temperature). |
X |
||||||
Check building control system for monitoring and control; adjust setpoints if needed (applicable to sites that have a SWH system integrated into the building automation system [BAS]). |
X |
||||||
Plumbing, Pipes, and Valves |
Ensure that the pressure relief valve is not stuck open. |
X |
|||||
Check and secure all pipe hangers, expansion joints, and associated items. |
X |
||||||
Check pipes and wiring for degraded/missing insulation. |
X |
||||||
Inspect the system for scaling; direct systems in areas with hard water need to be checked. If scaling occurs at water fixtures, it is likely to be occurring within the SWH system. Water treatment is necessary. |
X |
||||||
Pumps |
Ensure that the SWH circulating pump is operating when it is sunny and the SWH system is not shut down. |
X |
|||||
Check for malfunctioning pumps (circulating and distribution pumps). |
X |
||||||
Check flow rates and adjust them if necessary. |
|
|
|
X |
|
|
|
Clean the pump, strainer, controls, switches, and starters. Check the condition of the pump seal. Lubricate the motor if required. |
X |
||||||
Storage Tank |
Ensure that storage tanks are free from cracks, leaks, rust, or other signs of corrosion. |
|
|
|
X |
|
|
Ensure that there are no storage losses (insulate storage tank if necessary). |
|
|
|
X |
|
|
|
Drain the storage and expansion tanks. Flush them to remove sediment, scale, etc. |
|
|
|
|
X |
|
|
Replace the sacrificial anode in the storage tank. |
|
|
|
|
|
X |
|
Electrical Components |
Verify all electrical connections are tight. |
|
|
|
|
X |
|
Check for balanced three-phase power. |
|
|
|
|
X |
|
|
Check for over-voltage or under-voltage conditions. |
|
|
|
|
X |
|
|
Heat Transfer Fluid and Components |
Check glycol strength: run a pH test on glycol-water solution and adjust/replace it as necessary. |
|
|
|
|
X |
|
Only if a loss of efficiency is indicated or signs of leaking are evident around header, remove the heat exchanger element and clean it. |
|
|
|
|
|
X |
|
Follow the manufacturer’s recommendation for antifreeze replacement, usually not more frequently than every 5 years; must be performed by an experienced SWH contractor. |
|
|
|
|
|
X |
|
System Documentation |
Document all maintenance activities in a log book or electronic Computerized Maintenance Management System. |
Upon activity completion |
Performance Monitoring
Monitoring the performance of SWH systems is important to ensure cost savings. Measurement and verification (M&V) of SWH systems can be accomplished by purchasing M&V monitoring equipment from a specialized manufacturer, and system production can be checked and recorded monthly on an interface attached to the pump station. Unfortunately, SWH systems rarely include monitoring equipment with their installation. Monitoring equipment can be added to a new installation or retrofit at an additional cost to the project. Energy delivery is mass flow rate of water times specific heat times temperature increase, with the water flow measuring device being the expensive instrument to install and maintain. For collector loops that have a fixed on/off flow rate, the mass flow rate is often measured or calculated once and then stipulated as a constant.
In the absence of monitoring equipment, system production needs to be estimated for M&V purposes. The system designer should have documentation indicating the estimated or modeled savings. If it is not available, system output can be modeled (for instance, with RETScreen [RETScreen International]) using the building size, use type, and occupancy.
O&M Cost
All types of SWH systems require very little maintenance, and O&M costs are generally between 0.5% and 2% of the initial cost per year, depending on the technology type and complexity of the design (Walker 2016). O&M costs include a combination of work, such as inspection and cleaning, performed by on-site staff, as well as skilled labor performed by hired contractors such as plumbers.
Additional Support
The Department of Energy’s Solar Water Heater website features details of different SWH system types, how they work, and how to choose which is best for a given application. It also features tips and links for system O&M (DOE [n.d.]).
FEMP24 Renewable Energy Technology Applications - Solar Thermal and Concentrating Solar Power Technology is a one-hour online course that addresses how solar energy technologies can help federal sites meet agency goals and legislative mandates, improve energy security, and reduce environmental impacts while efficiently providing electricity, heating, cooling, and other applications.
The National Renewable Energy Laboratory (NREL) provides rule-of-thumb information about installation and O&M costs for thermal technologies, including SWH systems.
NREL has a Standard Work Specifications tool to assist maintenance staff, training instructors, and program administrators. Topic 7.0302.6 describes SWH systems.
Definitions
Operations and maintenance (O&M). Decisions and actions regarding the control and upkeep of property and equipment.
Preventive maintenance. An equipment maintenance strategy based on replacing, overhauling, or remanufacturing an item at a fixed interval, regardless of its condition at the time; also known as scheduled maintenance.
Sources of Information
American Society of Heating, Refrigerating, and Air-Conditioning Engineers (ASHRAE):
- ASHRAE Central Solar Hot Water Systems Design Guide
- ASHRAE 90336: Guidance for Preparing Active Solar Heating Systems, Operation and Maintenance Manuals
- ASHRAE 90342: Active Solar Heating Systems Installation Manual
- ASHRAE 90003: Active Solar Heating Design Manual
International Association of Plumbing and Mechanical Officials (IAPMO):
- Uniform Solar Energy Code Safe Solar System Requirements (2006)
Solar Rating and Certification Corporation (SRCC):
- SRCC OG-100-06: Operating Guidelines For Certifying Solar Collectors
- SRCC OG-300-08: Operating Guidelines and Minimum Standards for Certifying Solar Water Heating Systems
DOE (n.d.). Solar Water Heaters. U.S. Department of Energy, Office of Energy Efficiency and Renewable Energy.
National Renewable Energy Laboratory. Distributed Generation Renewable Energy Estimate of Costs.
National Renewable Energy Laboratory. Standard Work Specifications Tool. Topic 7.0302.6 Solar Water Heater.
RETScreenInternational. 2004. Clean Energy Project Analysis: RETScreen® Engineering & Cases Textbook. Minister of Natural Resources Canada, Ontario, Canada.
Walker, Andy. 2016. Whole Building Design Guide: Solar Water Heating. Prepared by A Walker, National Renewable Energy Laboratory, for the U.S. Department of Energy, Federal Energy Management Program, Washington, D.C.
Whole Building Design Guide. Renewable Energy Technology Applications - Solar Thermal and Concentrating Solar Power Technology. Continuing Education Course.
Published May 2022