Testing Collision Risk Solutions
Can the Turbine Itself Be the Answer?
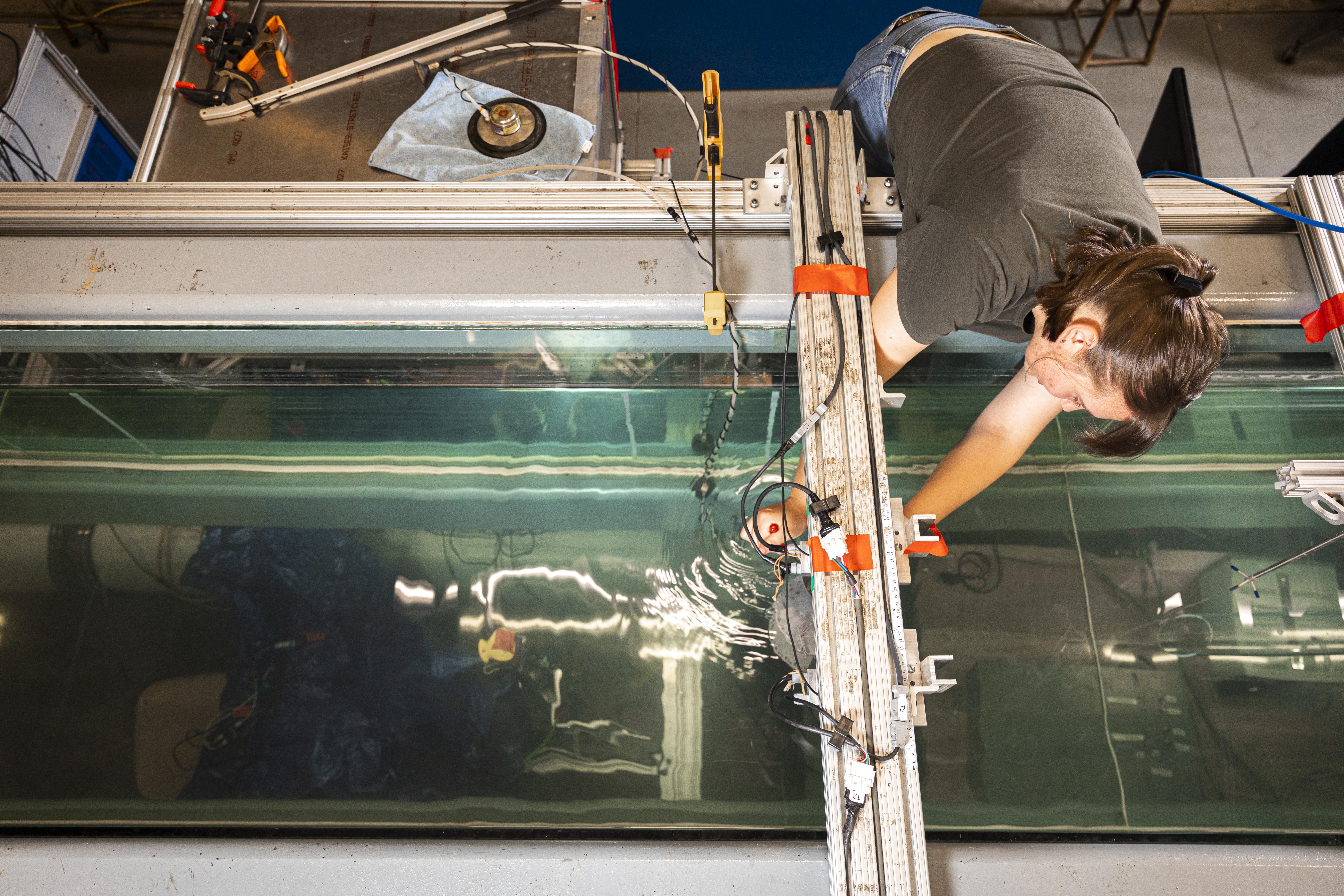
Tidal energy is a renewable marine resource that capitalizes on one of Earth's most consistent phenomena. Because of the gravitational forces of the sun and the moon, tidal cycles create the rising and falling of large bodies of water. This regular and predictable cycle translates to immense power and potential resource just waiting to be harnessed. Similarly, the energy from naturally flowing water from river currents can be captured using turbines deployed in the fast-moving parts of the water column. According to Kilcher et al., 2021, tidal and riverine energy in the United States can generate enough electricity to power over 30 million homes each year.
While this possibility is exciting, introducing current energy converters (CECs) like tidal and riverine turbines into underwater environments comes with potential risks. Moving components of CECs could create potentially injurious hazards for marine animals, including fish, diving seabirds, and marine mammals. The permitting process for tidal and other marine energy devices requires developers to understand the possibility of marine animal-turbine interactions based on scientific evidence. Presently, while the state of the science suggests that collision risk between marine animals is unlikely, it remains a primary concern for permitting and regulatory decision-makers. This is because uncertainty around collision risk remains high due to the challenging nature of gathering empirical data around animal-device interactions. Additionally, several conceivable outcomes with differing severity exist. Consequences of an interaction could include a near-miss event, a collision leading to minimal or no injury, or worst case, contact leading to significant injury and possible mortality. This is of particular concern for threatened and endangered species where a single collision could impact that species’ population.
To address collision risks, the research community studies animal behavior around marine energy devices, the probability of possible interactions, and potential outcomes (read more about Triton's collision risk research here). As part of these efforts, scientists, engineers, and developers are working to design practical detection and mitigation technologies that could be integrated into the turbines themselves to reduce risk of collision with animals. The Triton Initiative is one research team working toward these solutions.
Triton is a project of the Department of Energy Water Power Technologies Office, that aims to build knowledge around the potential environmental impacts of marine energy systems through environmental monitoring research. A valuable contribution researchers can make to the marine energy industry is to theorize and test proactive mitigation strategies that make marine energy devices safer, ecologically sensible, and more sustainable. Triton's Integrated Collision Detection and Mitigation (ICDM) project is conducting proof-of-concept phase research with the University of Washington (UW) through joint appointee Emma Cotter to help explore possible sensors that could offer a tangible solution to alleviate collision risks.
Exploring integrated solutions
Strain gauges can be built within turbine blades that monitor the structural health of the devices. These sensors are designed to measure parameters such as pressure, weight, tension, and resistance, which are all indicators of stress on the device's system and may be designed to have the capability to detect and mitigate interactions with marine animals. By studying and developing the capabilities of strain gauges and adjusting their sensitivities, it may be possible to adapt these technologies to sense collisions, or detect the presence of a marine animal swimming within a certain range of the turbine.
The speed of a turbine is governed by the velocity of the flowing water but can also be changed by a device's control system. This is typically done to optimize the power generated, but suppose a marine mammal comes within close proximity to the turbine and is detected by the turbine’s strain gauge? That information could potentially feed into the control system to slow down the blades. The ICDM researchers are investigating this aspect, wherein the ability for the controller can be utilized to alter the speed of turbine blades and lessen potentially harmful interactions with marine species.
The ICDM project is exploring applications for both strain gauge sensors and turbine regulation systems in a controlled laboratory environment using a flume—a large tank where researchers can change the flow of water to simulate ocean or river currents.
Triton ocean engineers Molly Grear and Cotter are partnering with the UW to run scaled experiments in the Alice C. Tyler flume in Seattle, Washington. These researchers are working with UW mechanical engineering master’s student Isabella Pestovski who has a background in mechanical design and controls. Together, they will conduct a series of tests to better understand the capabilities of strain gauges for detection as well as the ability of turbine control systems to slow and mitigate collisions. Eventually, Pestovski will use the resulting data from the strain gauges to develop a control algorithm for the turbine. “I'm looking forward to this hands-on opportunity to apply my skills in new ways,” says Pestovski, “I’m also excited for the chance to contribute to collision risk research so tidal turbines can one day be safely implemented.”
For the flume experiments, Zhiqun Daniel Deng and his team at the Pacific Northwest National Laboratory have fabricated instrumented, small-scale marine mammal models—called surrogates—that will be sent down the flume at different velocities to simulate possible collision scenarios. These ~10-inch silicone models are made to mimic the shape and texture of a killer whale, with additional scaled surrogates representing different marine mammals or fish. They have customized sensors built in to measure their movement as well as impact statistics if they collide with a lab-scale, axial-flow CEC located in the flume, which was designed loosely based on a reference model. These experiments will provide valuable information about these technologies’ sensitivities, capabilities, and limitations for possible mitigation solutions that developers can use in turbine designs.

“If the strain gauge and control system technologies are effective,” says Cotter, “we may be able to use that information to control the turbine and reduce the force associated with the collision, which could reduce the consequence of collision if it does occur.” Previous work has focused more on using external methods to assess the risk of collision – like cameras and sonars to observe how fish behave around a turbine. What is different about this research is that it uses sensors that are integrated into the CEC turbine blade to detect if collision actually occurs, which is often hard to do with cameras or sonar. Furthermore, this research will also investigate whether or not animals can be sensed before an instance of coming into contact with the CEC.
Before the tests begin, the ICDM team has been hard at work developing experimental design, forging the surrogates to withstand experiments, readying sensors and controls for tests, preparing the flume, and learning how to offload data. Inevitable challenges can be expected to arise when planning never-been done experiments like these. During initial experimental design setup in early December, the team realized the marine mammals needed weight evenly distributed throughout their silicone bodies to achieve equal buoyancy in order to move through the flume’s water channel effectively. This meant that the team had to perform “surgeries” on the surrogates, inserting various weights to determine the right buoyancy to allow the marine mammal models to function optimally. As part of the experimental design phase, the team is also working to design a chute-type contraption that feeds the marine mammals into the flume at a constant speed. This will allow for more consistent deployment of the surrogates during tests to enable effective experimentation. Grear shares, “I’m excited about working with UW and being able to use their facilities to conduct experimental work like this for the marine energy industry. There are a lot of possibilities!”
Stay tuned for updates from the flume and to learn how the ICDM project develops!

Written by Cailene Gunn.