PNNL Researchers Work to Make Industrial Catalytic Converters More Efficient
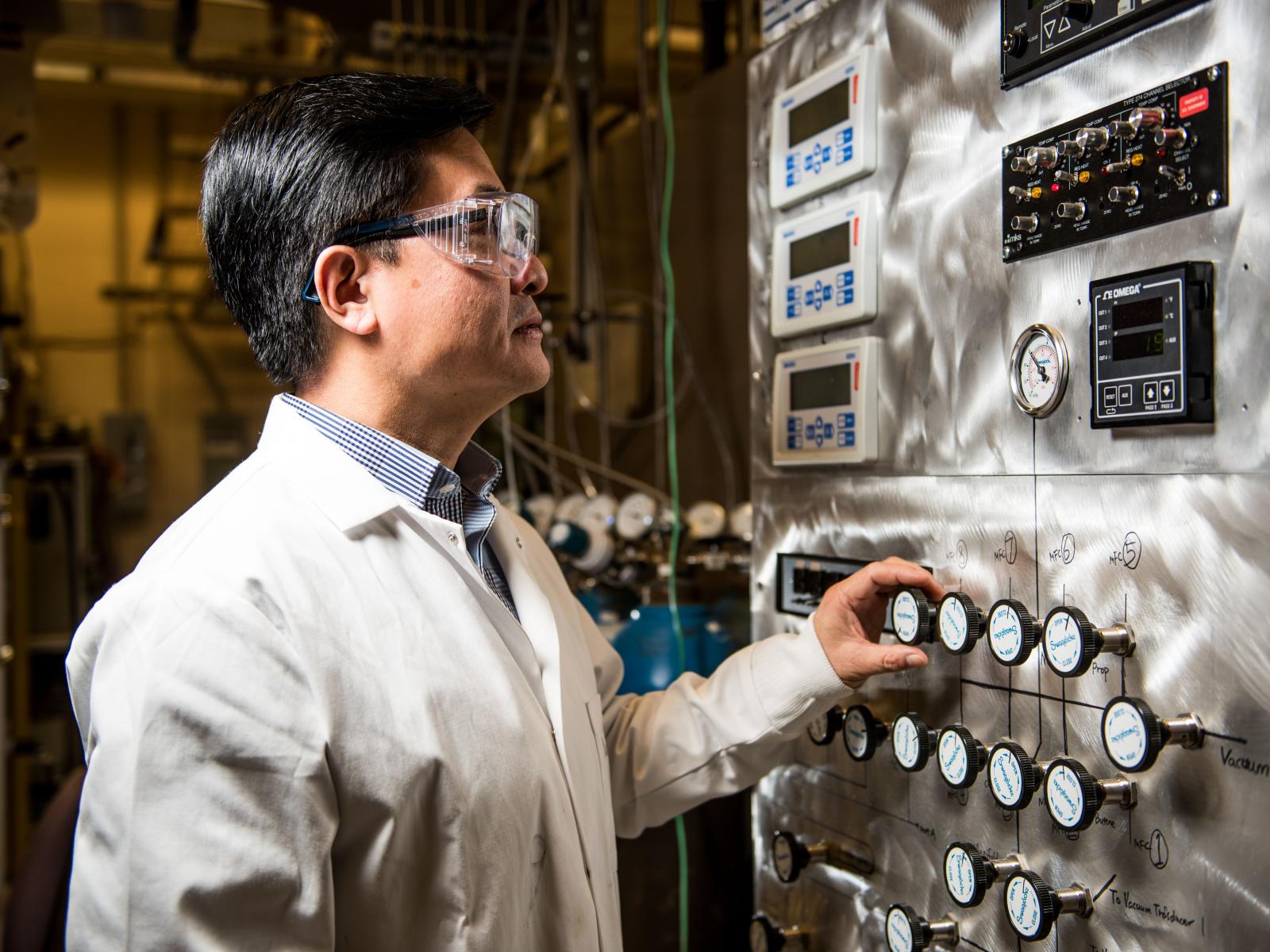
PNNL researchers and collaborators from industry and academia, including Washington State University, apply fundamental research to understand how to increase the efficiency and useful life of catalysts while reducing the need for critical materials. Shown here is Yong Wang, acting director of PNNL’s Institute for Integrated Catalysis and joint appointee from Washington State University.
(Photo by Andrea Starr | Pacific Northwest National Laboratory)
Researchers at the Department of Energy’s Pacific Northwest National Laboratory are helping to reduce the nation’s dependence on critical minerals and increase energy efficiency by improving the performance and longevity of catalysts for a variety of industrial applications.
Catalysts, which are materials that initiate or accelerate chemical reactions at lower temperatures, often use materials that are on the nation’s critical minerals list and subject to supply chain disruptions.
PNNL researchers leverage their world-class chemistry expertise and unique instrumentation to take a science-to-solutions approach to their catalysis research. By analyzing catalysts in new and different ways, they can understand how the catalyst’s active critical minerals behave, what causes them to degrade and how they can be improved.
One area of their research is focused on advancing catalytic converters for heavy-duty, off-road vehicles like agricultural and construction equipment. Researchers are driving innovations that will reduce catalyst costs by extending their useful life and optimizing the use of expensive and scarce critical minerals. These efforts, in partnership with industry collaborators, seek to lower costs for farmers and businesses.
PNNL’s research related to catalytic converters is applicable to gasoline and diesel internal combustion engines, as well as engines powered by alternative fuels, such as hydrogen, methanol and biofuels, in support of a diversified domestic energy supply.
Recently, scientists studied the interactions taking place between hot engine exhaust gases and cerium, a key component of catalysts that stores oxygen and supports chemical reactions.
China is the world-leading producer of cerium, which is on the U.S. critical minerals list. In collaboration with industry and university partners, including Washington State University, researchers discovered a process that improves the performance of cerium and reduces how much is needed to effectively treat undesirable exhaust gases.
In controlled experiments, the researchers artificially aged the cerium-based catalysts. While steam is often used in experiments like this, scientists used more realistic hot exhaust gases instead. Employing their suite of advanced analytical tools and techniques, they got a first-ever look at how pretreating the catalyst with exhaust caused cerium oxide to form thin, nanosized clusters about one atomic layer thick. These clusters covered the surface of the catalyst, increasing the number of active cerium catalytic sites exposed to the exhaust gases, thereby improving the catalyst’s performance.
The experiment also revealed that pretreatment with exhaust gases creates an oxygen “sponge” that can improve many common catalytic reactions that require adding oxygen or taking it away. Based on this discovery, scientists are pursuing options to purposely pre-activate catalysts with hot exhaust at the beginning of their life to increase their efficiency and durability.
PNNL has a strong history in catalysis research that includes advancements that revolutionized the approach to active and stable catalyst designs for multiple industries. As the originator of single-atom platinum group catalysts, PNNL is developing technologies that can react at lower temperatures while remaining durable at higher temperatures—a key attribute for many applications beyond engine exhaust.
Applying this foundational research, scientists revealed a path to significantly reduce the need for rhodium, another critical mineral with a volatile price tag that often exceeds the cost of gold. They discovered that, contradictory to conventional wisdom, rhodium atoms do not need to be adjacent to each other to enable the desired chemical reactions. Their experiments showed single atoms of rhodium are more active than nanoparticle clusters that contain more rhodium. Based on these results, they are developing catalysts with dispersed atoms of rhodium and cerium oxide that maximize efficiency and reactivity.
Looking ahead, PNNL will continue to advance catalyst design and enable the use of alternative fuels. By working with large engine and equipment manufacturers, such as Cummins and John Deere, and catalyst suppliers, such as BASF and Johnson Matthey, PNNL is informing commercial manufacturing and catalyst production. At the heart of it all is PNNL’s catalysis prowess, which is helping deliver innovations that meet the needs of industry and end users, while reducing dependency on critical materials and lowering the cost to consumers.
Steven Ashby, director of Pacific Northwest National Laboratory, writes this column monthly. To read previous Director's Columns, please visit our Director's Column Archive.
Published: July 14, 2025