New Manufacturing Approaches Taking Shape at PNNL Could Be the Future of the Industry
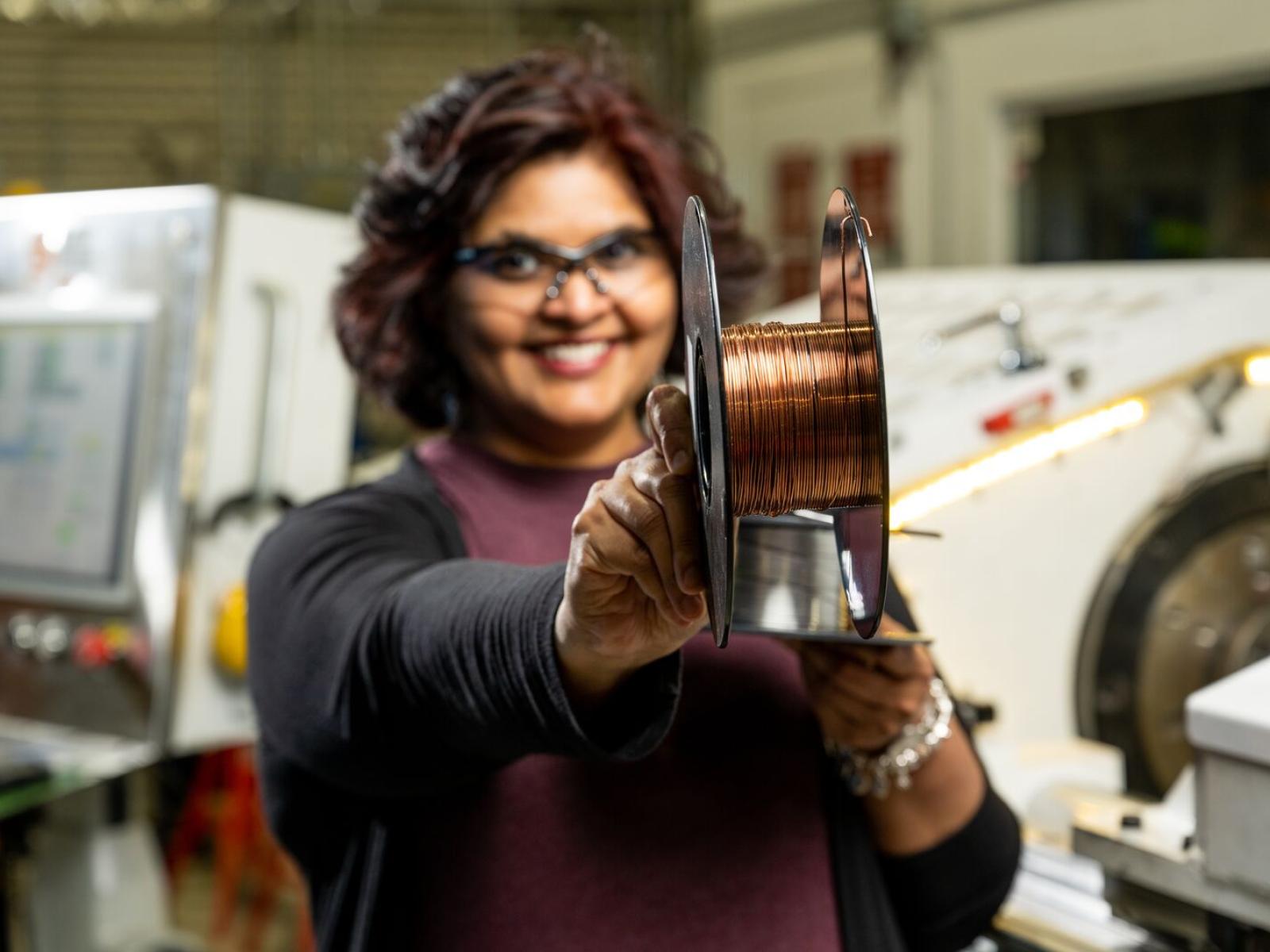
Keerti Kappagantula, a materials scientist at PNNL, is part of a team working to fabricate copper and aluminum wires that are more conductive than regular copper for use in the transportation industry.
(Photo by Andrea Starr | Pacific Northwest National Laboratory)
Today’s manufacturing industry faces several challenges. Companies are looking for ways to increase efficiency, reduce costs, lower carbon emissions and improve their products—all while remaining competitive.
At the Department of Energy’s Pacific Northwest National Laboratory, researchers are developing and applying novel approaches to sustainable advanced manufacturing that may help companies overcome these hurdles and, in so doing, strengthen American economic competitiveness.
At the forefront is PNNL’s patented Shear Assisted Processing and Extrusion (ShAPE™) technique. Conventional extrusion typically involves heating feedstock materials that are then pushed through a die to form wires, bars or tubes. ShAPE™, on the other hand, eliminates the separate, energy-intensive step of heating of the material.
Instead, a hydraulic press pushes the material against a quickly rotating head that generates enough frictional heat to soften it. This unique process also deforms materials in a way that enables novel chemistries and microstructures that result in better properties.
For example, researchers demonstrated that ShAPE™ uses 50 percent less energy to manufacture a specific aluminum alloy often used in vehicle manufacturing. In addition to saving energy, ShAPE™ also extrudes aerospace aluminum ten times faster than standard methods and resulting components can stretch 50 percent further before breaking.
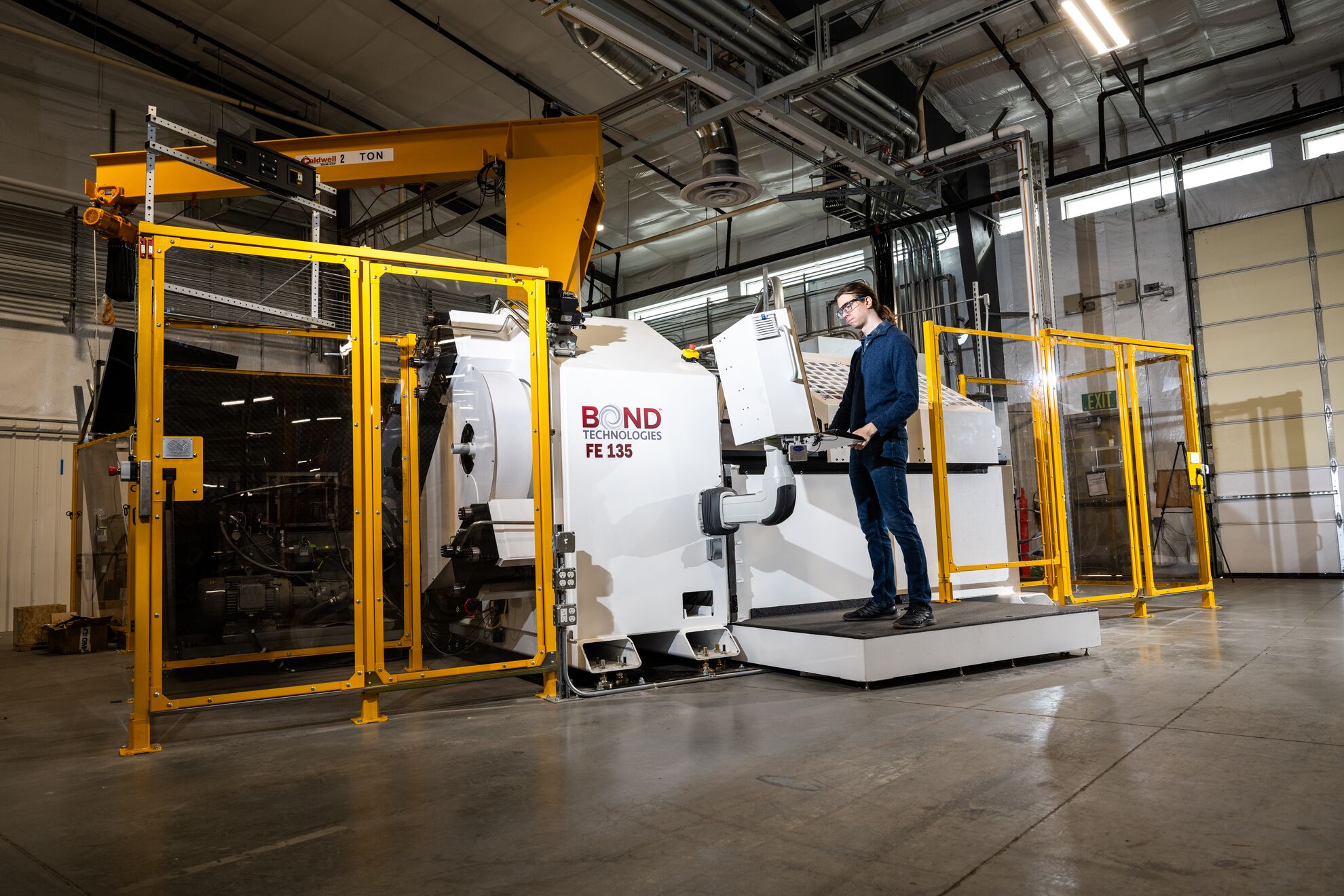
Results like these have piqued the interest of commercial partners for a variety of applications. Atomic 13, a start-up manufacturing company, is scaling a ShAPE™ process that can convert post-consumer scrap aluminum into building components.
By eliminating the need to mine and refine virgin aluminum, this approach reduces the cost and 80 percent of the energy consumption and carbon dioxide emissions associated with those processes.
Given that the building and construction industry represents about 55 percent of the global aluminum extrusion market, ShAPE™ offers a promising step toward a circular aluminum scrap market, where “waste” becomes a resource for new materials and products.
In another trash-to-treasure success story, researchers at PNNL and a leading North American auto part manufacturer teamed to develop ShAPE™ so it could use recycled aluminum for vehicle components and other applications.
A new collaboration with Ford, Hydro, Padnos and the University of Michigan seeks to advance this process that converts scrap aluminum directly into new parts for electric vehicles.
Unlike today’s approach to recycling, which requires melting the scrap and adding fresh aluminum to “dilute” the impurities, ShAPE™ eliminates the impurities quickly and economically.
The parts produced with this new, more efficient process meet rigorous automotive industry performance standards while making it possible for automobile manufacturers to make next-generation vehicles greener and cheaper.
Researchers also are exploring the potential for ShAPE™ to increase the conductivity of copper alloys and composites beyond that of pure copper. In an emerging effort, they are simulating the possibility of producing ultra-conductive wires from primarily aluminum.
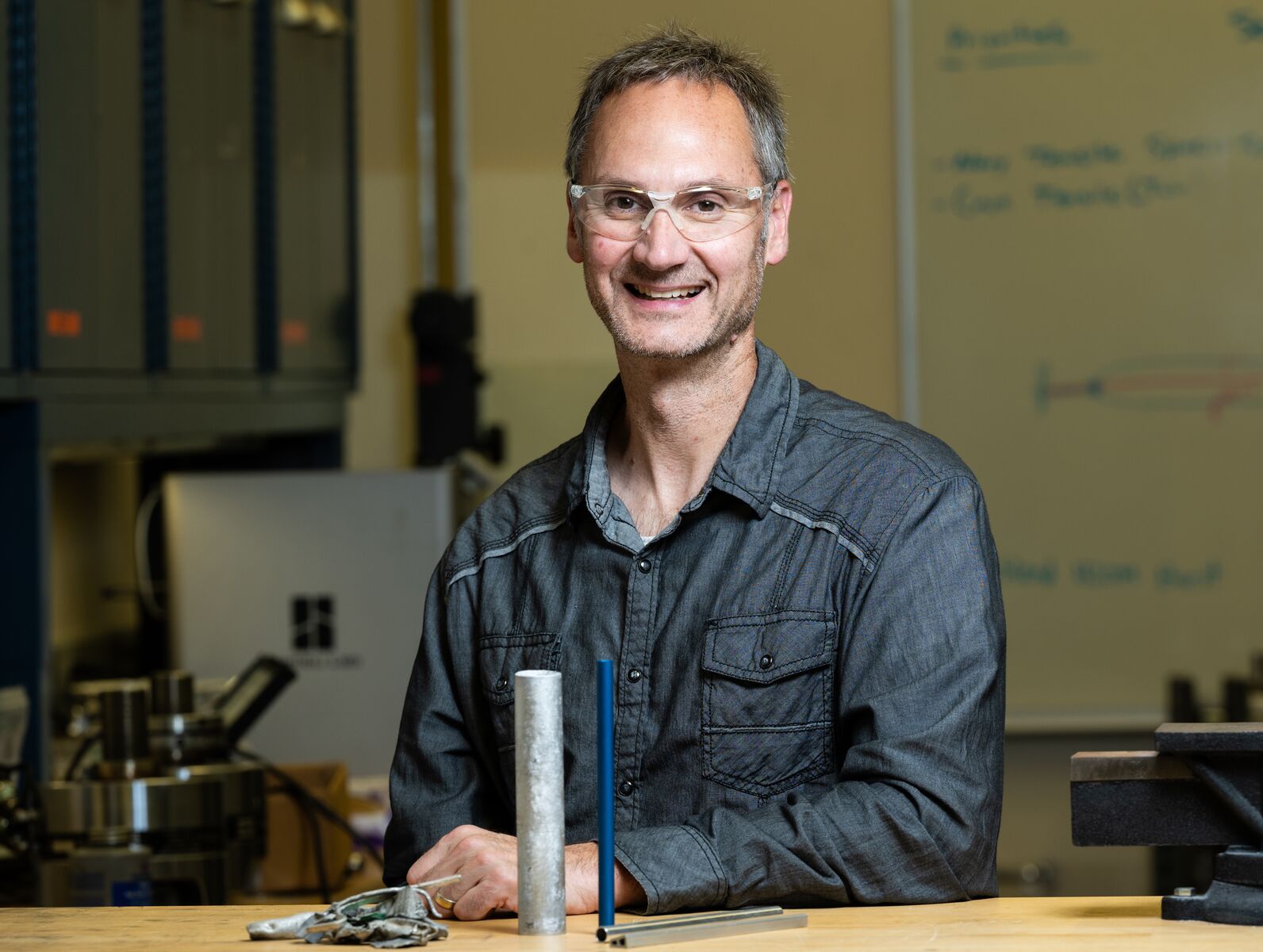
Aluminum is lighter, cheaper and more abundant than copper, which is commonly used in electrical wiring. However, aluminum is only about 60 percent as conductive as its heavier counterpart.
If researchers can use ShAPE™ to make aluminum composites that are nearly 80 percent as conductive as copper, they would be appealing for uses ranging from electricity transmission cables to electric vehicle wiring.
Looking toward even greater impact, PNNL recently installed a bigger, faster ShAPE™ machine that can extrude larger and more complex components than the first-generation machine.
This allows researchers to move beyond proof-of-concept approaches to industrial-scale manufacturing. Additional ShAPE™ machines to support development of other specialized materials for higher-efficiency energy systems also are in the works.
It is exciting to see the real-world applications for—and benefits of—sustainable advanced manufacturing innovations like ShAPE™. By delivering the science and technology to move these solutions forward, researchers at PNNL are literally shaping the future of manufacturing.
Steven Ashby, director of Pacific Northwest National Laboratory, writes this column monthly. To read previous Director's Columns, please visit our Director's Column Archive.