Friction Stir Processing Gets a Boost from New Machine Learning Model
Physics-informed model helps improve precision and protect machinery
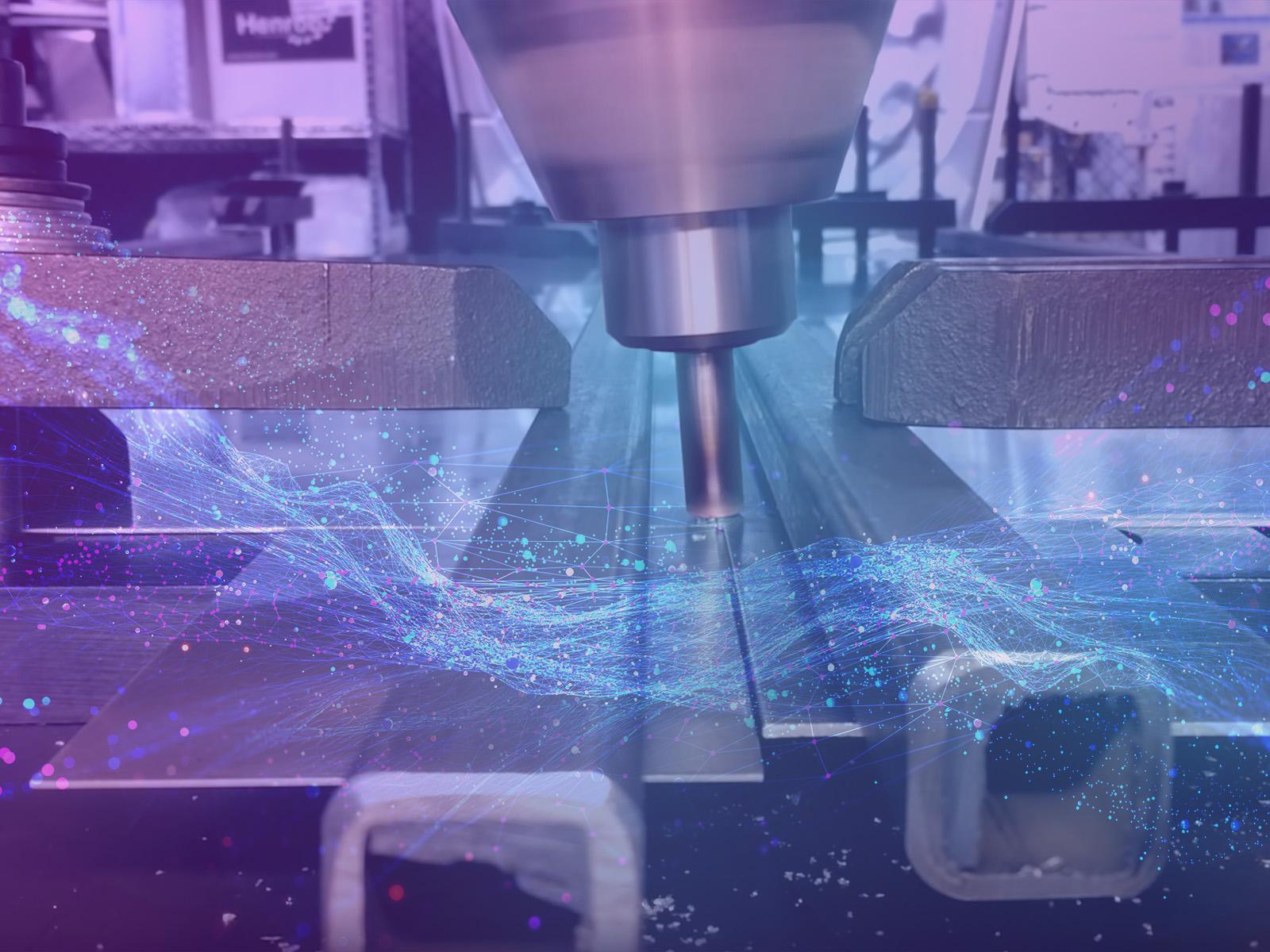
Machine learning can help researchers optimize friction stir processing.
(Composite image by Jeffrey London | Pacific Northwest National Laboratory)
Friction stir processing (FSP) runs a spinning tool along the surface of a material, using the heat generated by friction to transform the material microstructure—an approach that can help quickly and precisely engineer alloys for next-generation vehicles.
Now, researchers at Pacific Northwest National Laboratory (PNNL) have developed a new, physics-informed machine learning model that accurately predicts how heat accumulates and dissipates during FSP. The model will help researchers improve the precision of the technique and reduce the risks of wasted energy, wasted material, and tool breakage.
Causing a stir
“Temperature plays a critical role during friction stir processing,” explained David Garcia, a materials scientist in PNNL’s Solid Phase Processing Materials Research group. “A constant temperature helps to control the microstructure and prevents defects from forming.”
Spin up too fast—or too slow—though, and the tool might degrade, or even break. Over-cautious ramp-ups can also degrade the microstructures of the material, leading to wasted energy and material.
“The FSP tool has a preferred temperature range,” Garcia said. “At low temperatures, the tool is very brittle and prone to cracking; at high temperatures, the features on the surface of the tool start to wear away. Ideally, the process would involve a slow ramp-up to temperature, but this can degrade the microstructure in the surrounding area due to excessive heat input.”
As a result, the goal is usually to bring the FSP tool from room temperature to the desired temperature—typically around 800° Celsius—as quickly as possible without breaking it.
“To prevent damage to both the FSP tool and the material, it’s vital that we understand how the temperature evolves in response to process parameters,” Garcia said.
Staying informed
But modeling FSP is a tricky task.
“From a physics-based perspective, there’s just so much going on with FSP,” explained James Koch, a data scientist at PNNL. “There are different time scales, different length scales. Modeling how those physics interact—often very complicated, nonlinear interactions—with enough fidelity to be confident? That’s a tall order.”
Using ground-up, physics-based approaches, like smoothed-particle hydrodynamics modeling, produces detailed results but is time- and resource-consuming. On the other hand, conventional deep learning approaches would produce “black box” models that lack explainability—and thus lack industrial applicability.
The PNNL team incorporated the best of both worlds, building a model combining machine learning and ordinary differential equations. The model was trained on sparse data from just ten FSP experiments, but its predictions are informed by the principles of thermodynamics—an approach called physics-informed machine learning that enhances accuracy and explainability, particularly when training data is limited.
“We account for what energy goes into the region of interest, approximate internal heat generation, and approximate what’s leaving,” Koch said. “We can build a robust model on those first-principle physics, helping us get around issues of data availability, complexity at different scales, and so on.”
Turning up the heat
The resulting model is quick and accurate, reliably predicting how heat accumulates and dissipates in FSP experiments with similar parameters to those used to train the model. The approach is also remarkably lightweight: the researchers were able to run both training and inference on a laptop.
The researchers explained there is much more opportunity to expand the model’s applicability—both by incorporating different variables and by expanding the range of experiments used for training. Still, the model is a big step toward achieving that balance between speed and reliability.
“Fast, accurate prediction of the temperature response has significant value for real-time control of the friction stir process,” Garcia said. “This type of model can be directly integrated into the friction stir equipment to make the technology more robust and attractive to industry partners.”
The research paper, published in the Journal of Intelligent Manufacturing, was written by James Koch, Keerti Kappangantula, WoongJo Choi, Ethan King, David Garcia, Hrishikesh Das, Tianhao Wang, and Ken Ross.
Published: October 22, 2024