Custom-Designed Materials Processing Made Possible with Simulation Tools
Computational framework simulates complete solid phase processing methods

Materials scientist Ayoub Soulami and computational scientist Lei Li are coauthors on this latest research published in Materials & Design.
(Photo by Andrea Starr | Pacific Northwest National Laboratory)
A novel computational framework developed by Pacific Northwest National Laboratory (PNNL) is the first of its kind to accurately simulate exactly what happens on both a macroscale and microscale when materials are extruded into new products by solid phase processing (SPP). PNNL research published in the journal Materials & Design outlines a newly developed computational framework capable of predicting SPP outcomes. The model can predict an extruded product’s processing conditions and material properties before it ever enters the machine.
Novel manufacturing methods crucial for the transportation industry
Lightweight materials are key to making the wide-scale deployment of energy-efficient transportation a reality. PNNL is paving the way for new manufacturing methods to reduce the energy and cost associated with lightweight materials. Technologies in PNNL’s SPP suite, such as cold spray, friction stir welding and processing, and Shear Assisted Processing and Extrusion (ShAPE™), use extreme levels of deformation to manufacture high-performance materials. However, scientists didn’t fully understand the physics behind these processes until now.
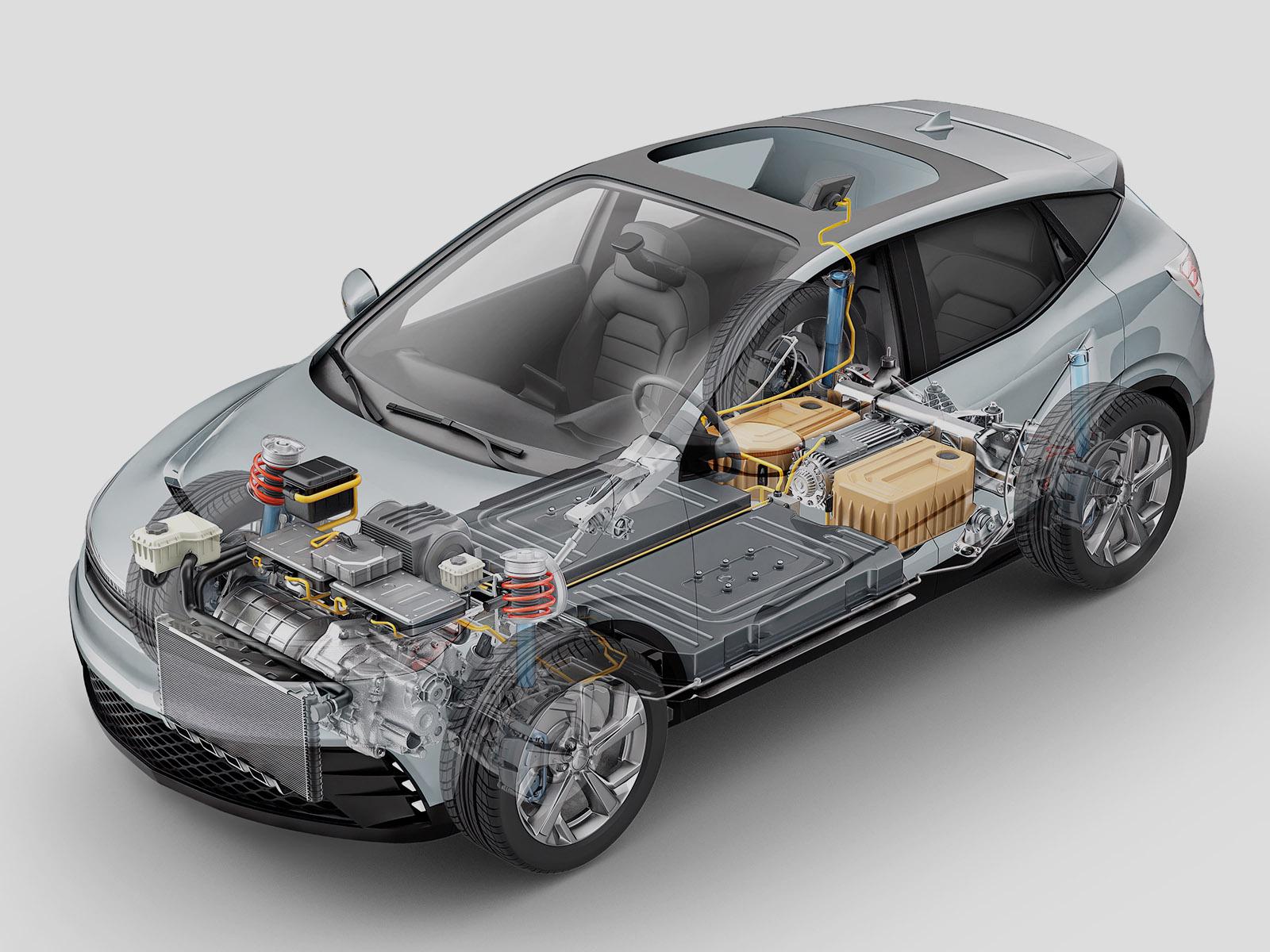
Modeling framework reveals a clearer picture
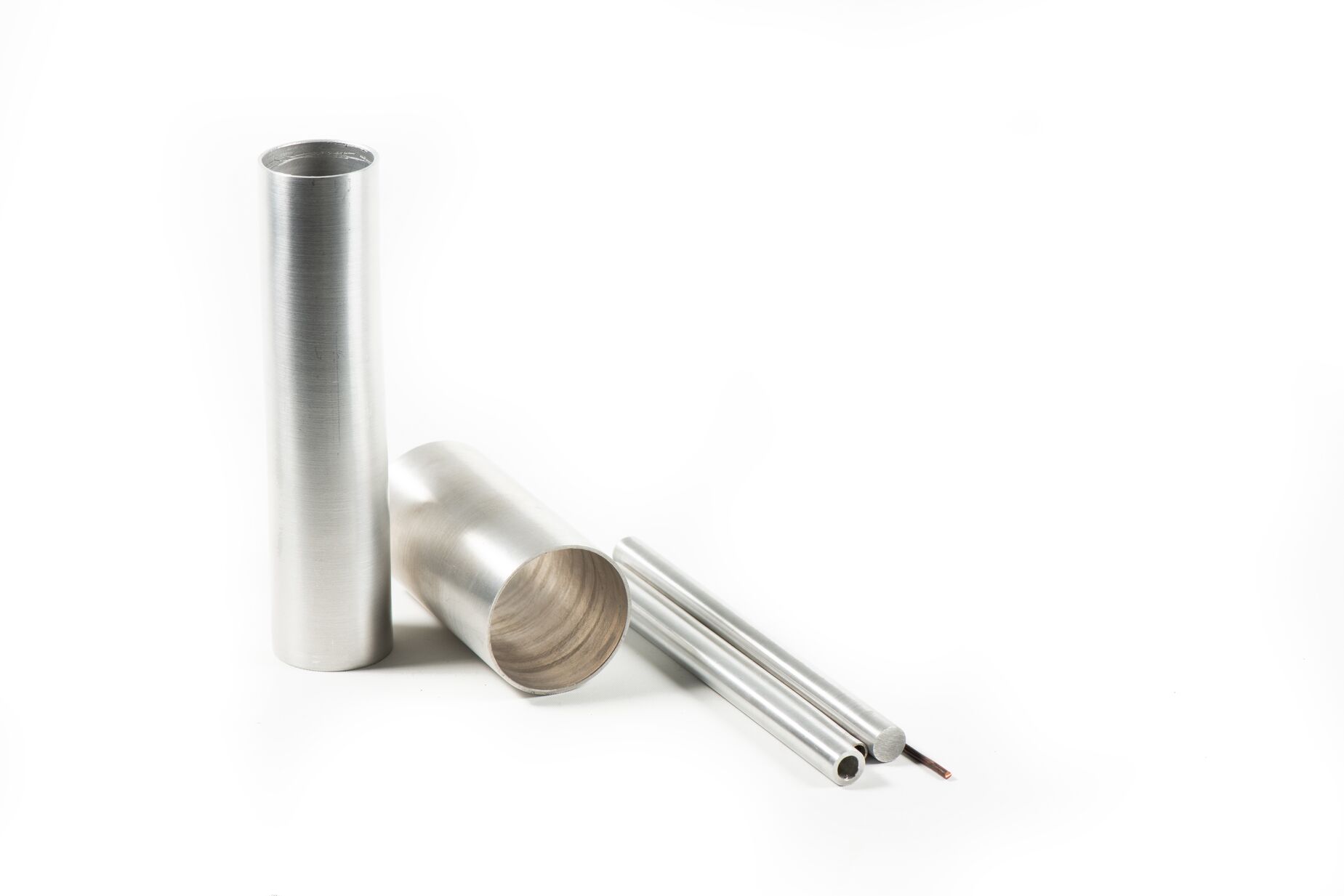
Traditional ways of understanding how materials experience intense levels of deformation are limited. That’s where a new formulation called smoothed-particle hydrodynamics (SPH) comes into place. PNNL’s SPH modeling framework takes into consideration every small detail of the SPP process—the thermomechanical and contact conditions, heat generation, microstructure evolution, and more. This insight can be used by scientists and engineers to modify SPP methods to produce lightweight materials with tailor-made specifications more quickly.
Initially validated using experimental ShAPE data, this SPH-based framework is the only tool suitable to model materials processed under extreme conditions, such as large deformation, high temperature, strain rates, and complex contact conditions between processing tools and materials being processed. The overall advantage to using PNNL’s modeling framework is to reduce the energy and cost to process high-performance materials. The properties of these materials may include increased strength, ductility, corrosion resistance, and electrical conductivity.
Validating the “impossible”
When his team was approached to develop a modeling tool used to study SPP three years ago, project investigator and corresponding author Ayoub Soulami said, “There’s no way we can model this. It’s very complex. We can model pieces of it, but there’s no way we can have a tool to model the process in its entirety.” But that’s exactly what they ended up doing using the SPH method.
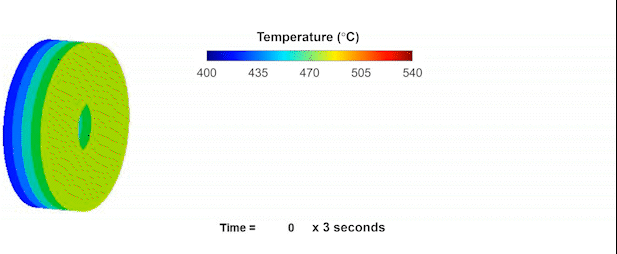
When building the model, the research team conducted many simulations to mimic experiments that had already been done. They were able to validate the model’s predictions against past experiment outcomes published in Materials & Design and the Journal of Manufacturing Process. According to the lead author, Lei Li, “This is a continuum-level model, meaning that we are taking into consideration every single detail in the process.” From the small features in the die used to shear the material to the contact conditions, heat generation, and material thermomechanical response—this model presents the full picture of what is happening in an extreme environment.
The tool is being used to predict the microstructure of many different materials and processing systems in the SPP suite. In addition to being used by SPP researchers at PNNL, the tool is being used by research sponsored by the Department of Energy’s Advanced Manufacturing and Materials Technologies Office, the Industrial Technologies Office, the Vehicle Technologies Office, and the National Nuclear Security Administration.
This work was funded by PNNL’s Laboratory Directed Research and Development program through the Solid Phase Processing Science Initiative.
Published: March 2, 2023