Atomically Visualizing the Oxidation of Model Steel
Combining multiple experimental techniques to observe the early stages of oxidation in a model material
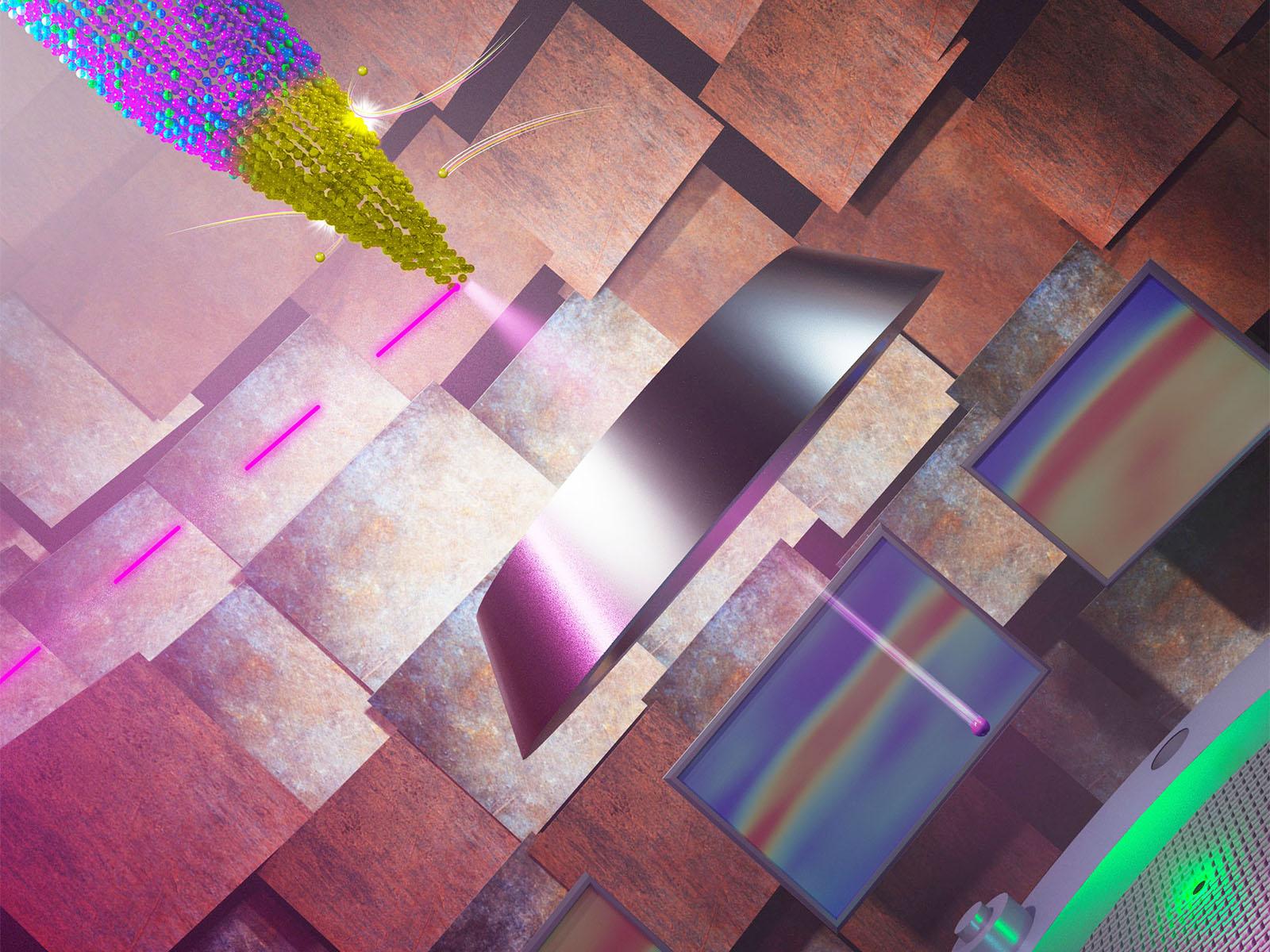
Understanding how steel oxidizes at an atomic level can help researchers develop stronger, longer lasting materials.
(Image by Nathan Johnson | Pacific Northwest National Laboratory)
The Science
Since the iron age, humanity has relied on steel. While scientists have made substantial progress toward creating more robust steel, its corrosion and degradation remains a problem. Researchers studied the degradation mechanism of an iron-chromium-nickel (Fe-Cr-Ni) alloy—a model material for steel—in the presence of oxygen at high temperatures. Using isotopically labeled oxygen coupled with in situ atom probe tomography, complementary electron microscopy, X-ray diffraction, X-ray absorption, and computational models, researchers were able to understand how the alloy oxidized at an atomic scale. They found that metal ions diffused through the initial oxide on the material surface to react with additional oxygen, rather than oxygen diffusing through the initial oxide to metal underneath.
The Impact
Steel corrosion is a major problem with associated costs of billions of dollars. It affects infrastructure, including buildings, cars, and bridges, with direct implications for human safety. There is a critical need to better understand and mitigate the causes and effects of corrosion. This work shows that the outward diffusion of metal ions to the metal-air interface primarily dictates the oxidation kinetics of model stainless steels at high temperatures. Insights gained from these types of atomic scale in situ studies can help researchers across the globe better understand how corrosion happens in different materials.
Summary
Human civilization deeply depends on infrastructure, including conventional bridges and building and advanced installations, such as nuclear reactors. All these installations use large quantities of steel, which requires costly maintenance to deal with corrosion-induced degradation. Although stainless steels are resistant to corrosion at room temperature, at high temperatures they can degrade through oxidation. Designing better and longer lasting stainless steels for safety critical applications requires understanding the atomic scale mechanisms of high temperature corrosion and oxidation. Researchers characterized the oxidation of a Fe-Cr-Ni alloy using in situ atom probe tomography with isotopically labeled oxygen, as well as additional advanced electron microscopy and X-ray spectroscopy measurements. With the help of computational modeling, they then proposed atomic scale oxidation mechanisms. Researchers found that under high temperature conditions, the iron atoms preferentially diffuse through an initial chromium oxide layer to the alloy/air interface. Once there, the metal atoms react with atmospheric oxygen to form a new iron oxide layer. This produces a material with a top layer of iron oxide, followed by chromium oxide and nickel segregated at the oxide-metal interface. These results help elucidate the atomic scale diffusional mechanisms responsible for the high temperature degradation of stainless steels. Future work will explore how this oxidation mechanism will be modified under the combined effects of high temperature water and stress—conditions common in nuclear reactors that can lead to stress corrosion cracking.
PNNL Contact
Arun Devaraj, Pacific Northwest National Laboratory, arun.devaraj@pnnl.gov
Funding
This work was supported as part of FUTURE (Fundamental Understanding of Transport Under Reactor Extremes), an Energy Frontier Research Center funded by the Department of Energy (DOE), Office of Science, Basic Energy Sciences. A portion of the research was performed using EMSL, the Environmental Molecular Sciences Laboratory, a DOE Office of Science user facility at Pacific Northwest National Laboratory.
Published: June 14, 2022
A. Devaraj, D. Barton, C.-H. Li, S. Lambeets, T. Liu, A. Battu, S. Vaithiyalingam, S. Thevuthasan, F. Yang, J. Guo, T. Li, Y. Ren, L. Kovarik, D. Perea, M. L. Sushko, (2022), “Visualizing the Nanoscale Oxygen and Cation Transport Mechanisms During the Early Stages of Oxidation of Fe-Cr-Ni Alloy” Advanced Materials Interfaces, 2200134. [DOI: 10.1002/admi.202200134].