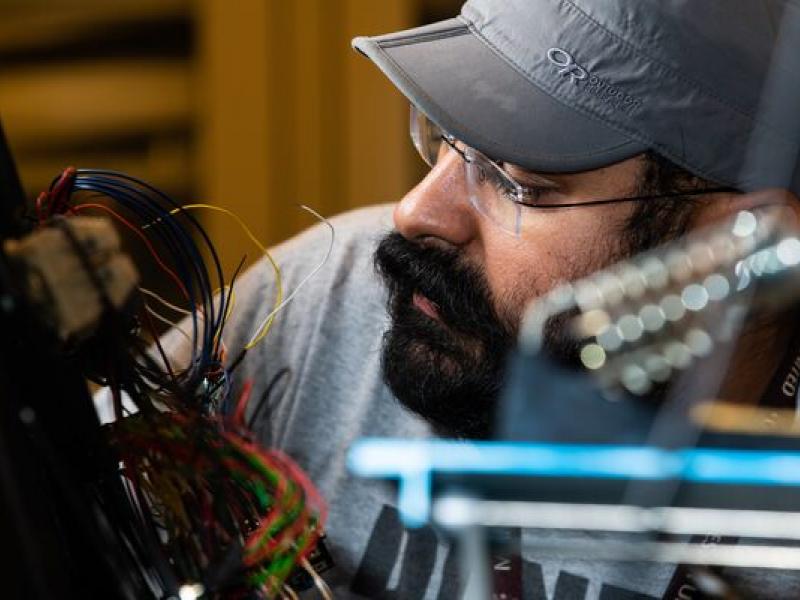
Rapid Prototyping Lab
Where engineering expertise, modern tools, and rapid processes combine to provide efficient, affordable solutions
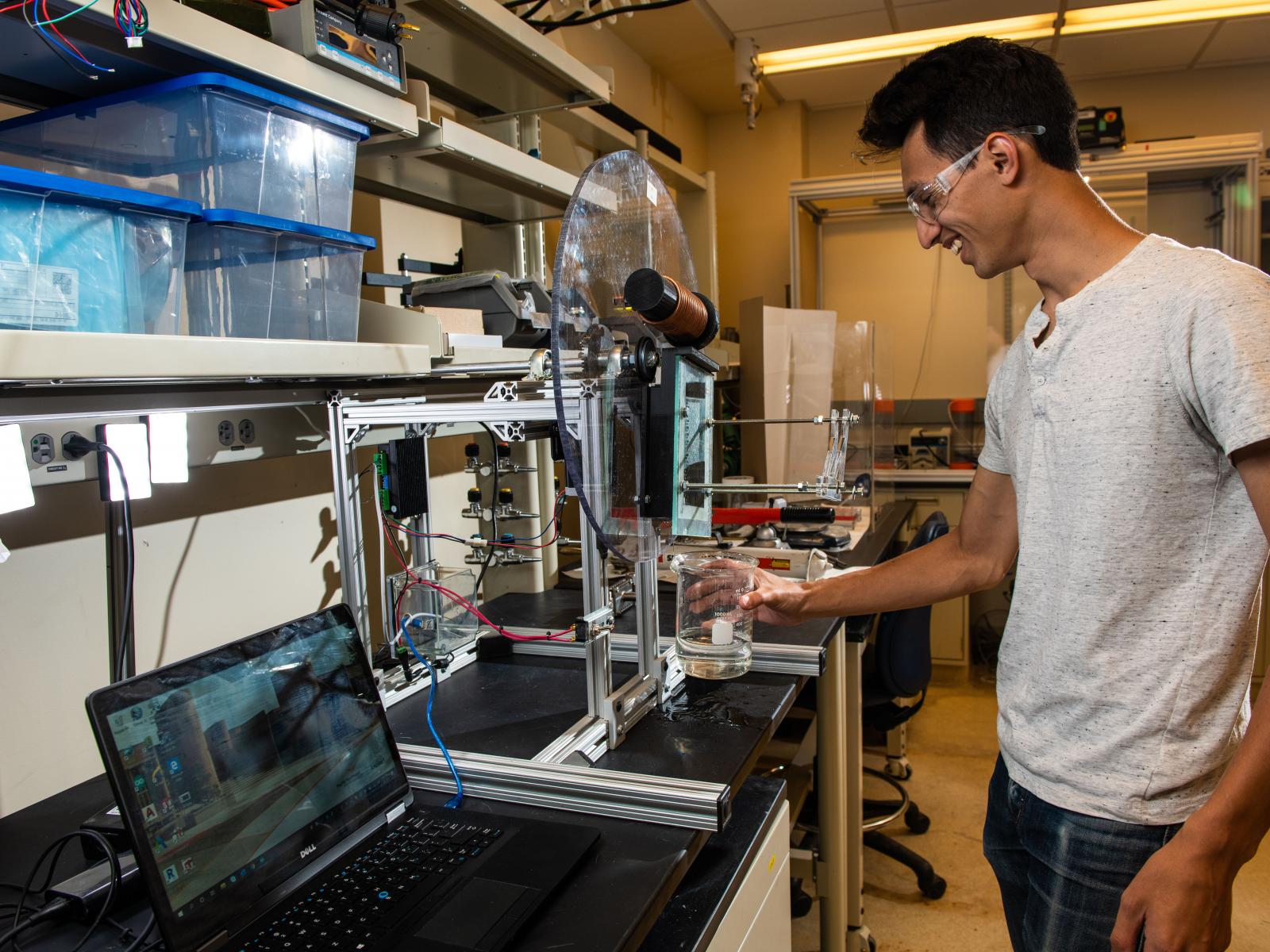
PNNL Rapid Prototyping mechanical engineer, Jason Serkowski, works with a functionalized prototype of an induction melting furnace test stand in the Rapid Prototyping Laboratory. The stand is a product of the team’s iterative approach, using electronics, three-dimensional (3-D) printing, rapid fabricated parts, mechanical construction, parasolid design, computational modeling, and simulant selection.
(Andrea Starr | Pacific Northwest National Laboratory)
The Rapid Prototyping team at Pacific Northwest National Laboratory (PNNL) provides unique engineering services to clients as they work to bring to reality first-of-a-kind systems, materials, and components. The team operates out of the Rapid Prototyping Lab, located on PNNL’s Richland campus in room 1228 of the Biological Sciences Facility.
Rapid design development (prototyping) services are based on a collaborative and multidisciplinary approach. Through hands-on development and experimentation, the team works closely with clients—both internal to PNNL as well as external—to move concepts to a prototype stage that can be a starting point for final design development.
From three-dimensional (3-D) computer-aided design (CAD) to 3-D printing, the team has a multitude of advanced tools at its disposal for solving advanced engineering problems. Considered a true makerspace, the laboratory is where experts explore the performance of prototypes through a process of rapid iterations.
Recent R&D 100 awards and multiple patents prove the team’s strengths in problem-solving and designing field-deployable solutions.
This lab is in addition to specific rapid prototyping capabilities developed for national security sponsors.
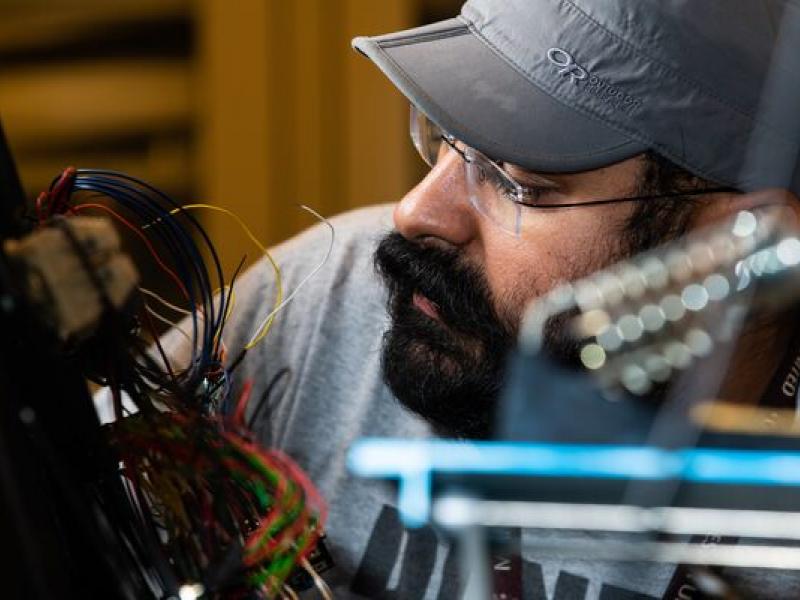
PNNL electrical engineer, Hardeep Mehta, inspects a microprocessor on a device developed by the Rapid Prototyping team.
(Andrea Starr | Pacific Northwest National Laboratory)
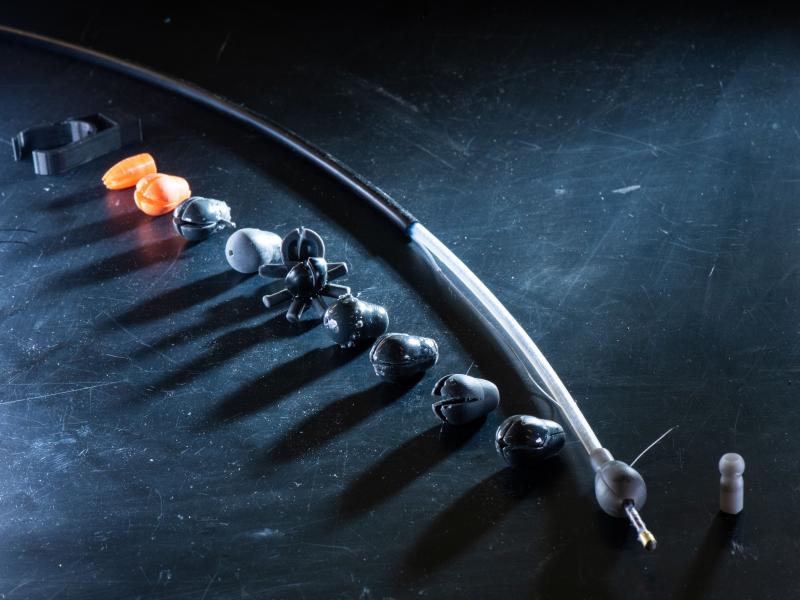
Iterative steps showing the lineage of Rapid Prototyping Lab design, eventually resulting in a successful sample tool head.
(Andrea Starr | Pacific Northwest National Laboratory)

This Prusa filament three-dimensional (3-D) printer was used to print a gyroid prototype (pictured), enabling PNNL researchers to study its periodic minimal surface.
(Andrea Starr | Pacific Northwest National Laboratory)
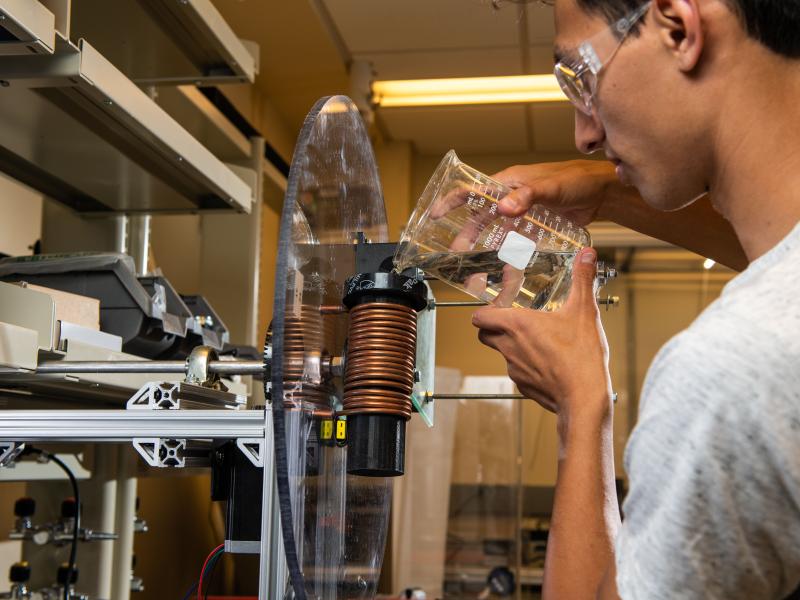
PNNL Rapid Prototyping mechanical engineer, Jason Serkowski, works with a a functionalized prototype of an induction melting furnace test stand in the Rapid Prototyping Laboratory. The stand is a product of the team’s iterative approach, using electronics, three-dimensional (3D) printing, rapid fabricated parts, mechanical construction, parasolid design, computational modeling, and simulant selection.
(Andrea Starr | Pacific Northwest National Laboratory)
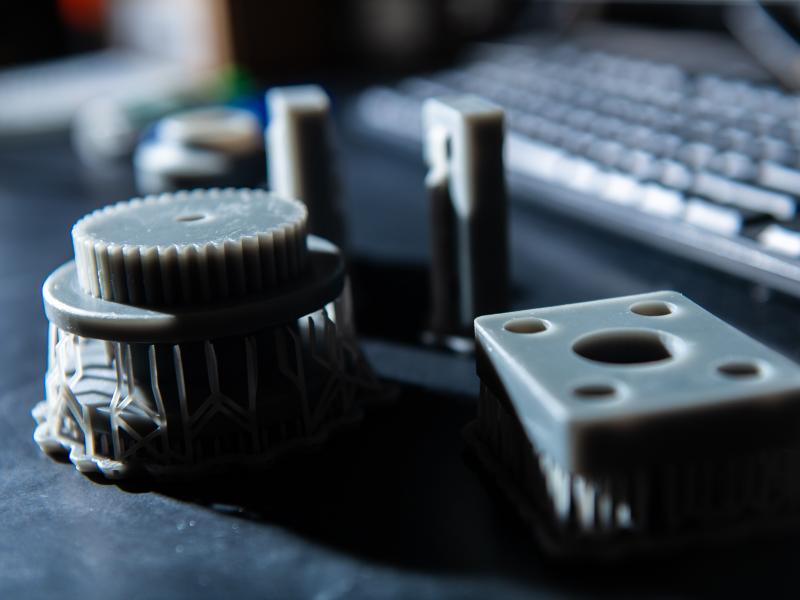
Resin-printed parts used by PNNL’s Rapid Prototyping team to test friction effects in a conceptual gear box. These parts are integral in testing for friction, as it is an extremely difficult factor to account for conceptually.
(Andrea Starr | Pacific Northwest National Laboratory)
Expertise
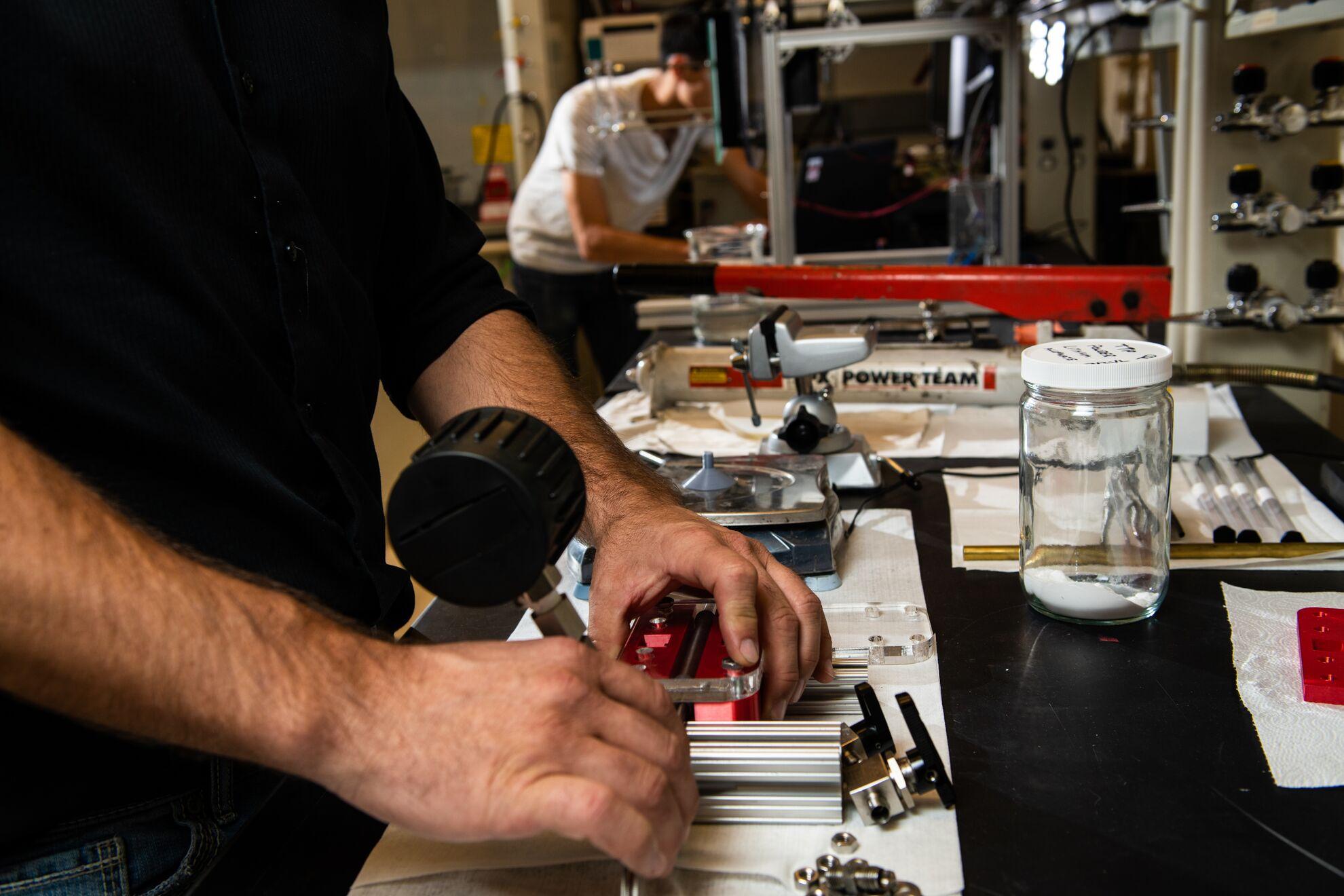
PNNL’s Rapid Prototyping Lab is the perfect one-stop shop for all phases of a client’s project life cycle, from prototype design to experiment, and throughout phases of testing. This not only assures continuity, but also the following additional benefits:
- Design development, even with a limited budget or tight schedule
- Design concepts, even with limited information or not-yet-known correlation to published information
- Problem solving, even if design is not optimized, limits are not known, or a solution is not obvious
- Assistance when conventional fabrication techniques are not practical
- Innovative engineering review or analysis; brainstorming
- Independent analysis and testing
- Computer code validation of designs that may include thermal, flow, and similar.
Approach
The Rapid Prototyping team prides itself in its “design thinking,” an iterative and collaborative, nonlinear process that starts from a deep understanding of clients’ challenges. This, in turn, drives a cycle of new prototype development and testing that rapidly evolves ideas into solutions.
Using an agile methodology, clients partner with the team on project management, resulting in “sprints” that ultimately shorten a potentially onerous feedback loop.
Services
Rapid Prototyping Team
Team members utilize broad hands-on engineering expertise and modern equipment to design, fabricate, and test prototypes to meet clients’ mechanical, electrical, chemical, and control systems objectives. The team overcomes clients’ problems by using electronics, 3-D printing, rapid fabricated parts, mechanical construction, parasolid design, computational modeling, and simulant selection.
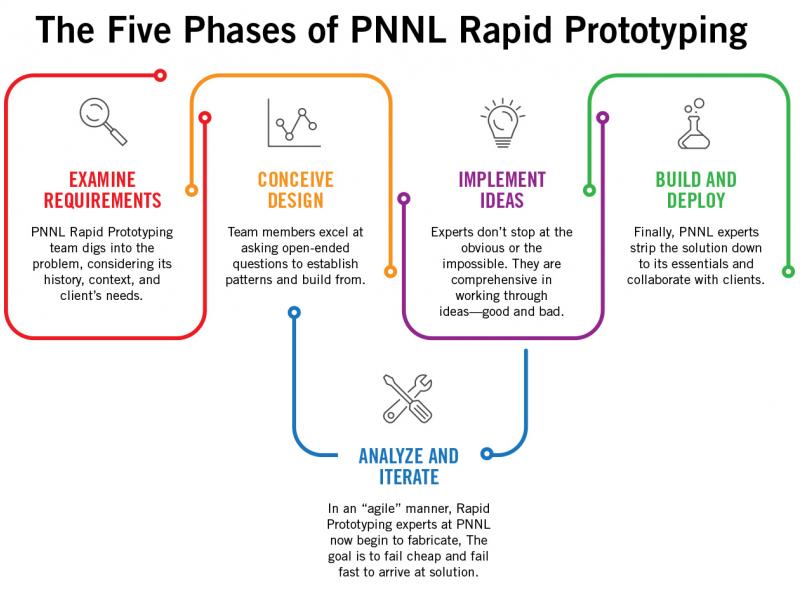
A Closer Look
Examine – digging into the client’s problem, making considerations for its history, context, and the client’s unique needs.
Design – using open-ended questions to establish patterns and use the answers to build from. Some of the approaches and tools used in this process include:
- Parasolid modeling
- Computational modeling
- Piping and instrumentation diagrams (P&ID)
- Schematics
Implement – comprehensively work through all ideas—good and bad—generated in the design phase. Some of the approaches and tools used in this process include:
- Scaled systems
- Instrumentation and control
- 3-D printing
- Resin, filament, metal
- Product mockups
- Scaled models
- Mechanical construction
- Laser cutting
- Soldering
- Functional testing
Iterate – fabricate in an agile manger, with the goal to fail cheap and fail fast to quickly arrive at a solution.
Deploy – strip the solution down to its essentials and collaborate with clients on final steps.