Surprising Interfacial Strength in a Toughened Tungsten Alloy
Strengthened softer alloy phase increases the toughness of the overall composite material
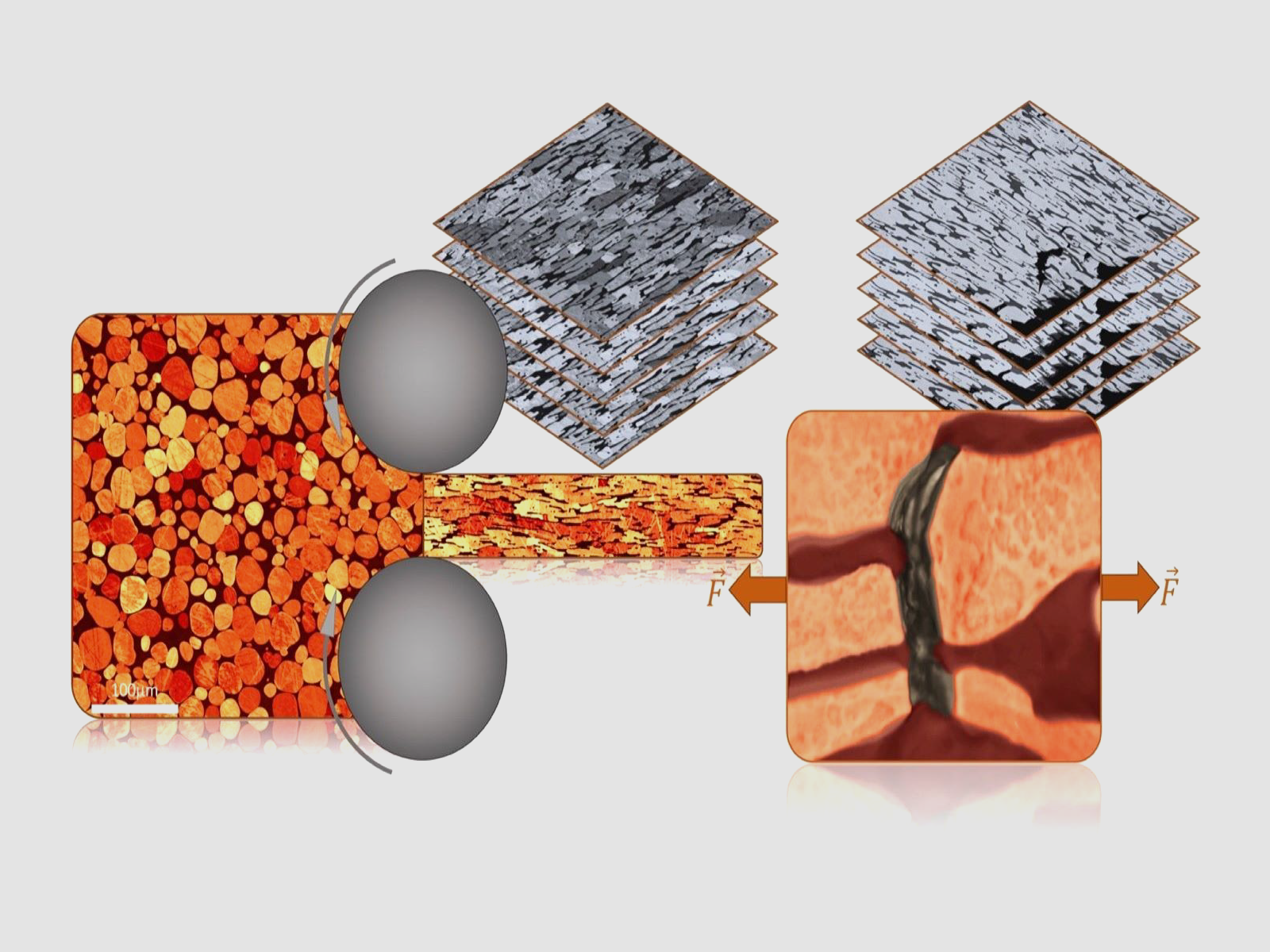
Hot rolling produced a brick-and-mortar composite structure of hard spheroidal tungsten (W) particles in a nickel-iron-tungsten (Ni-Fe-W) ductile matrix. Cracks occurring in W bricks under tension were stopped by the Ni-Fe-W mortar ligament.
(Image by James Haag | Virginia Polytechnic Institute and State University)
The Science
Monolithic tungsten (W) is currently the standard plasma-facing material for future fusion energy devices, but it can be brittle and fracture. Researchers developed W composites that overcome the limitations of monolithic W. Hot rolling and annealing alters the microstructure of the W composite, producing a brick-and-mortar structure capable of distributing stress over a large area and resulting in a more robust material. Microcracks that occurred in the W bricks under tension were stopped by the nickel-iron-tungsten (Ni-Fe-W) mortar phase. Researchers traced the toughening to the remarkable strength of the connection between the brick-and-mortar phases.
The Impact
The materials used in future fusion energy devices must be exceptionally robust, remaining resistant to all types of damage even at very high temperatures. Developing an understanding of how to increase toughness can create better, more robust materials for applications in extreme conditions. In addition, this work used serial sectioning and scanning electron microscopy to create a three-dimensional (3D) reconstruction of the W composite that will aid future computational modelling of changes in the material.
Summary
Tungsten heavy alloys are receiving increasing interest as an alternative to pure tungsten for fusion reactor plasma-facing materials. To justify their use in the extremely harsh environment of a fusion reactor, researchers must develop a detailed understanding of their microstructural features and associated mechanical properties. Researchers chose a W/Ni-Fe-W composite to investigate the effect of hot rolling treatments on the ability of the material to accommodate deformations. Both in-situ tensile testing and 3D microstructural analysis of the samples revealed that the edge of the hard W phase experiences microcracking, which is blunted and arrested by Ni-Fe-W phase. Characterizing toughening mechanisms in these materials has provided deeper insight into the underlying physics governing material behavior in these alloys, revealing a surprising interfacial strength between the different phases.
PNNL Contact
Ram Devanathan, Pacific Northwest National Laboratory, ram.devanathan@pnnl.gov
Funding
This research has been supported by DOE Office of Fusion Energy Sciences under Contract #DE-AC-05-76RLO-1830. M. M. acknowledges a financial support by the DOE Basic Energy Science program (BES) DE-FG02-06ER15786 for 3D reconstruction technical development.
Published: November 19, 2021
Haag IV, J. V., Edwards, D. J., Henager Jr., C. H., Setyawan, W., Wang, J., Murayama, M. “Characterization of ductile phase toughening mechanisms in a hot-rolled tungsten heavy alloy” Acta Materialia, 204, 116523, (2021). [DOI: 10.1016/j.actamat.2020.116523]