CDI Scientists Adapt Intrinsically Porous Polymers for Filament-Based 3D Printing
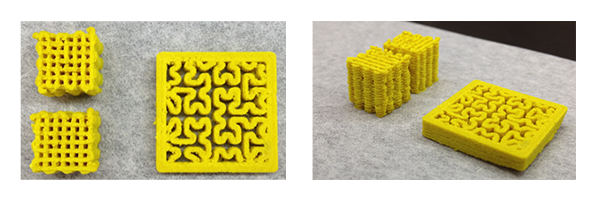
Return to CDI News & Highlights
Research Team: Zack Kennedy, Josef Christ, Bruce Arey, Lirong Zhong, Chris Barrett
Summary: Because they are high-performing and can be produced at a low cost relative to other microporous materials, Microporous polymers (MPPs) are now emerging in areas such as gas separations and storage. Further advancement of MPPs requires new processing methods for broad application. In this work, an archetypical MPP was systematically blended with thermoplastics, enabling processing by extrusion and 3D printing. Techniques developed led to complex free-standing MPP-based 3D objects with desirable microstructural features.
Science Impact: Microporous polymers are currently in rapid development for use in applications aligned with energy and national security missions. The PNNL research team anticipates that their thermoplastic-blending and extrusion 3D printing approach will be a powerful strategy to produce engineered microporous polymer-containing composite structures.
Contribution to CDI: Development of feedstocks and detailed characterization of printed objects is central to identifying part- and process-specific chemical signatures that can be leveraged for forensics or for performance prediction.
Abstract: Future advances and usage of all-organic polymeric materials with permanent void spaces and high surface areas, in applications such as separations or as supports, depends heavily on the development of processing techniques to produce complex geometry objects. Here, the high free volume glassy microporous polymer PIM-1 was fabricated, as a major component in a polymer blend, into complex and customizable 3D objects by fused filament fabrication (FFF). PIM-1 was found to be compatible with polycaprolactone (PCL) and polylactic acid (PLA) and thus could be processed by extrusion into filaments with high loadings of PIM-1 (50% by mass). Ternary PCL/PLA/PIM-1 composite filaments provided an optimal balance of durability and melt flow characteristics for consistent FFF 3D printing of intricate structures. As printed, the micropores of PIM-1 were blocked and inaccessible to N2 during sorption experiments; however, the ternary composite structures displayed significant meso- and macroporosity and nanostructured phase separation. Postprinting immersion in 3-chloro-1-propanol was identified to selectively remove PCL within the composites, re-expose the characteristic micropores of PIM-1, and retain the macrostructure of the printed object. After postprinting treatments, specific surface areas by the Brunauer–Emmett–Teller method (as high as 460 m2 g–1) were found to directly correlate with the PCL content originally present. The extrusion-based processing methodology provides a new approach for production of intrinsically porous polymer objects in custom and complex shapes by reinforcement with thermoplastics (PCL and PLA).
Citation:
- Kennedy ZC, J Christ, B Arey, L Zhong, C Barrett. 2019. “Tunable Porosity in Fused Filament 3D-Printed Blends of Intrinsically Porous Polymer and Thermoplastic Aliphatic Polyesters Polycaprolactone and Polylactic Acid.” ACS Applied Polymer Materials, 1 (3), 482-492, 10.1021/acsapm.8b00172