Making Better “Stuff” at PNNL
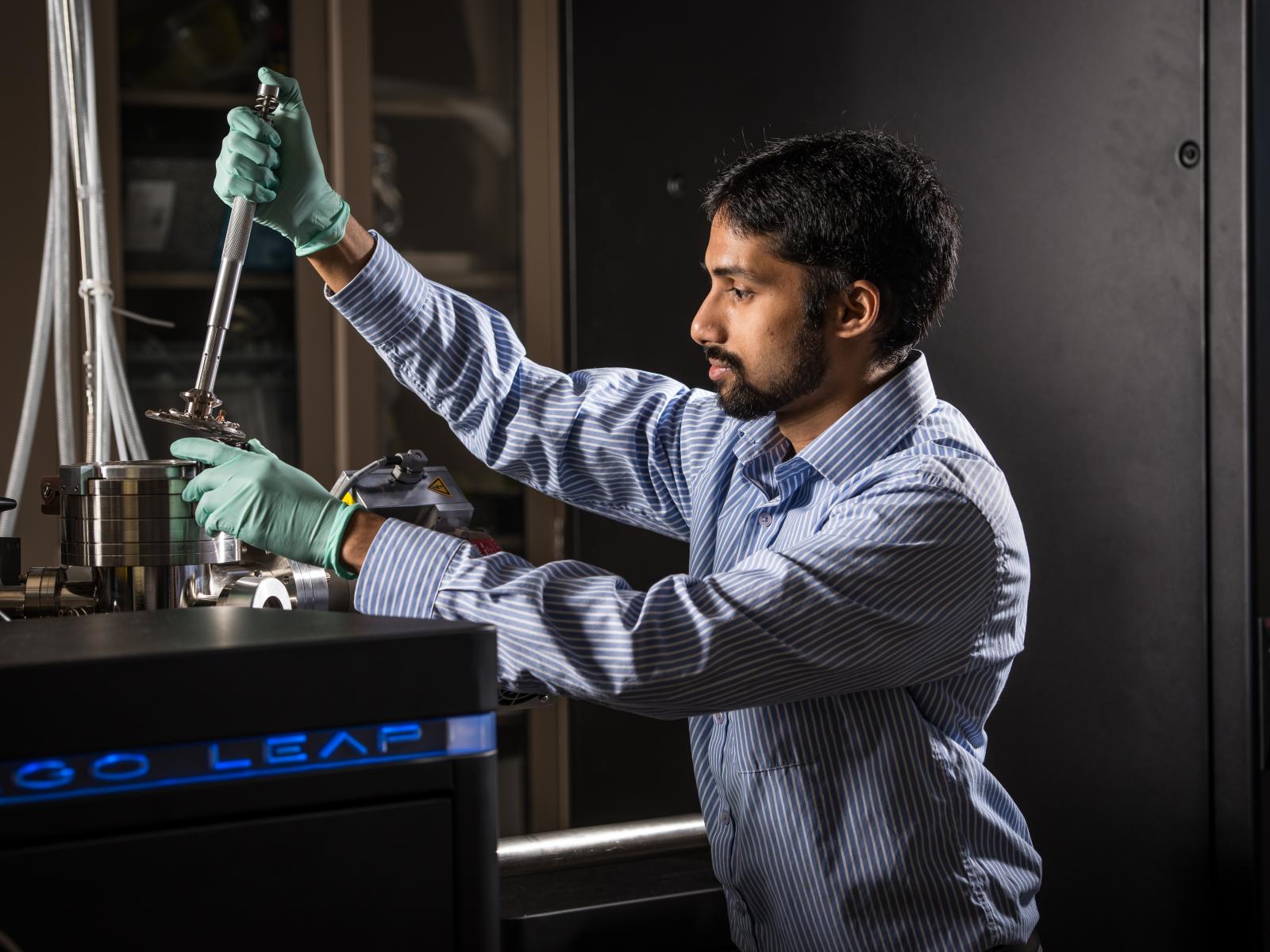
Researcher Arun Devaraj and his colleagues at Pacific Northwest National Laboratory in Richland use an atom probe tomography system, or APT, to create an "atomic map" of how the individual atoms within a titanium alloy are arranged, and then manipulated the arrangement to form a special nanostructure—resulting in the strongest titanium alloy available today. The APT is one of the specialized instruments at EMSL—the Environmental Molecular Sciences Laboratory—a DOE Office of Science User Facility at PNNL.
(Photo by Pacific Northwest National Laboratory)
There is a science website for kids that defines materials science as "the study of stuff" and, in the simplest of terms, that's right.
Materials science is about understanding how different materials are made, how they change and how they can be used. Research in this area leads to new materials for countless applications that impact our daily lives and benefit society.
Modern materials are all around us. Strong, lightweight composite materials are used in today's sporting goods, automobiles and airplanes. Bio-compatible materials are used in medical devices and implants. Semi-conductor materials make our electronics smaller, lighter and faster. Materials science also helps to keep our water clean and make batteries better.
At the Department of Energy's Pacific Northwest National Laboratory in Richland, researchers are working to understand the principles that govern how materials are formed, also known as materials synthesis. With this knowledge, scientists can make all kinds of new materials for a variety of uses.
For instance, one team of PNNL scientists created a new type of two-dimensional material to mimic a cell membrane. This material, which scientists call a nanomembrane, has straight edges, is thinner than a soap bubble and can withstand being submerged in a variety of liquids at different temperatures. It exhibits a number of features similar to a cell membrane—like changing its thickness in response to the presence of salt.
PNNL materials scientists also have developed a new titanium alloy that is stronger than any on the market and could boost fuel efficiency in vehicles due to its light weight.
With additional research and a better understanding of how these nanomembranes form, scientists hope to customize their size and function. Ultimately, they could be used for water filtration, molecular sensing, medical diagnosis, drug delivery and fuel cells—to name just a few potential applications.
PNNL is a recognized leader in developing materials for energy storage, be it grid-scale batteries used to store energy from the sun or wind for later use, or smaller batteries used for transportation. Earlier this summer, President Obama announced that PNNL would lead the Battery500 Consortium, a partnership of DOE national labs, universities and industry working together to make smaller, lighter and less-expensive batteries that can be adopted by manufacturers for use in future electric vehicles.
The consortium got its name because its goal is to build a battery with a specific energy of 500 watt-hours per kilogram. Specific energy is a measure of how much energy can be packed into a battery based on its weight. Considering that today's electric vehicle batteries are in the 170-200 watt-hours per kilogram range, this is a significant challenge. And it's all about materials. Scientists in the consortium will be studying different materials that could be used for a lithium-metal battery's positive electrode, while working to prevent unwanted chemical reactions that could impair the battery's performance.
PNNL materials scientists also have developed a new titanium alloy that is stronger than any on the market and could boost fuel efficiency in vehicles due to its light weight. It gets its strength from the way its atoms are arranged to form nanostructured phases. Our scientists used advanced imaging techniques to see how the atoms are aligned and then manipulated the nanostructure to develop the new alloy.
Not only is the alloy stronger, but it was made using a low-cost process capable of producing the material at industrial scale. While typical processes start with molten titanium, our team used titanium hydride powder—cutting processing time in half and significantly reducing energy consumption. This process was co-developed with ADMA Inc., an Ohio-based company that serves the aerospace industry and others.
If materials science is the science of stuff, then these are just three of the many ways in which PNNL scientists and their colleagues are advancing materials science to make better stuff. Their knowledge, creativity and tenacity are improving our lives today and in the years to come.
Steven Ashby, director of Pacific Northwest National Laboratory, writes this column monthly. To read previous Director's Columns, visit pnnl.gov/news and filter by Director's Columns in our Latest Stories.
Published: September 20, 2016