Research in Tri-Cities Could Make Cars and Planes More Fuel Efficient and Super Strong
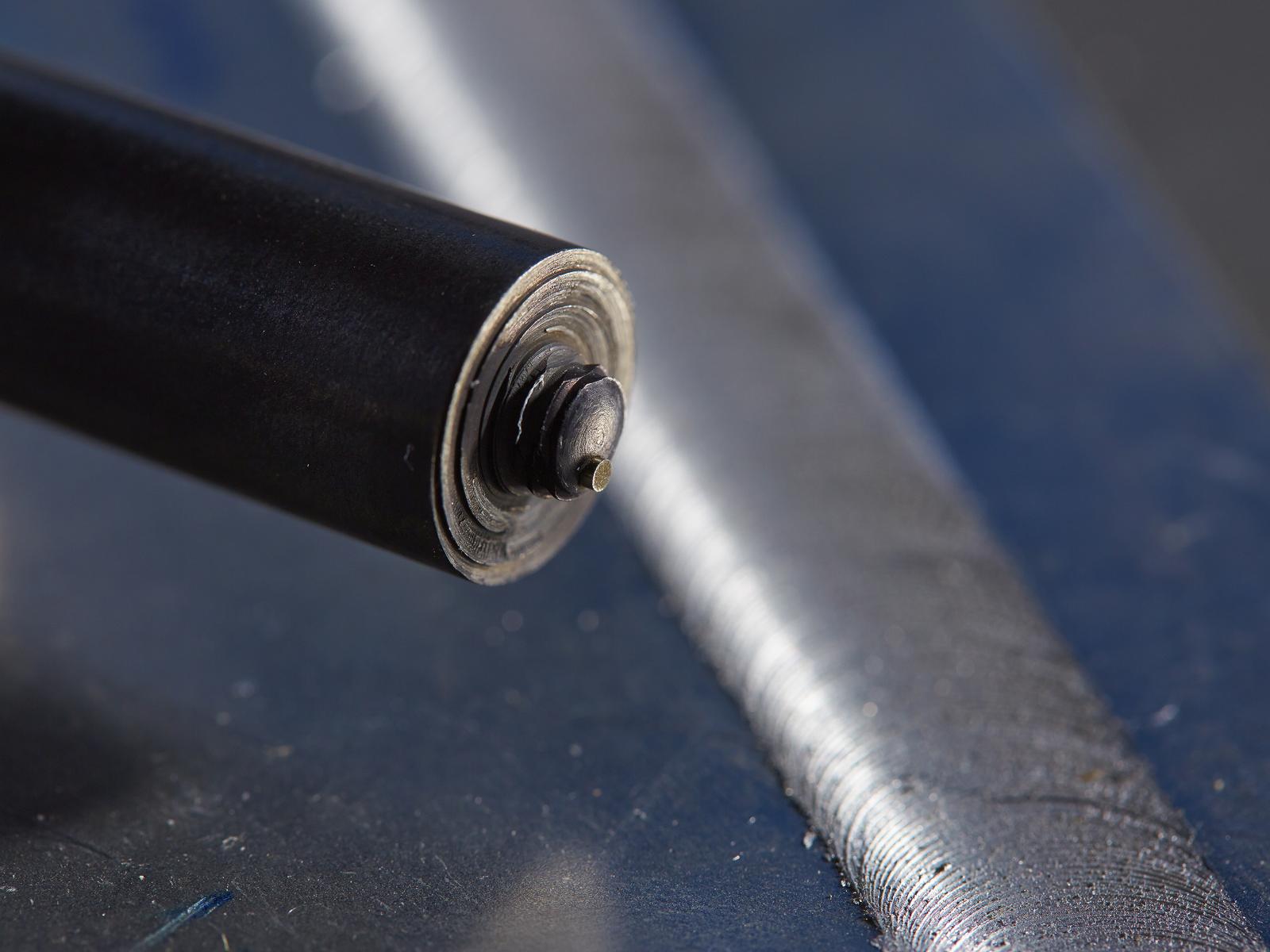
PNNL's award-winning friction stir scribe process makes it possible to join materials with drastically different melting points without needing additional adhesives, bolts and rivets. Using this tool, manufacturers can now incorporate new and different materials into a variety of strong, lightweight parts without sacrificing strength or durability.
PNNL
Superman may be known as the "Man of Steel," but scientific superheroes at the Department of Energy's Pacific Northwest National Laboratory are developing a novel approach for manufacturing metals with superior strength.
Drawing on deep materials science expertise and engineering know-how, PNNL researchers are paving the way for adoption of new manufacturing methods that could revolutionize the energy, automotive and aerospace industries.
Known as solid phase processing, their techniques use friction to heat, mix and join metals without melting them.
PNNL's innovations in this area, four of which are already patented and more than a dozen of which have patents pending, promise to decrease the energy required to manufacture components while also delivering higher performance — all at a lower cost.
Solid phase processing involves deforming metals so much that their internal structure completely changes.
The newly formed structures offer reduced defects and enhanced performance advantages, such as exceptionally strong bonds, improved corrosion resistance or increased magnetic properties.
PNNL researchers are focused on better understanding how different process conditions imposed on materials affect the resulting engineering properties.
They are creating new tools to study the underlying physics and using modeling to predict how materials will evolve at the microscale.
Results are most promising.
Better military vehicles
With support from the U.S. Army, researchers are enabling heavy steel components in combat vehicles to be replaced with thicker, lighter aluminum.
Researchers successfully used their novel friction stir dovetailing process to join thick plates of aluminum to steel, something not possible using conventional welding because the materials have different melting points.
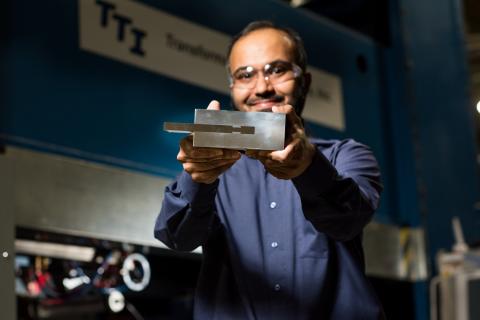
PNNL's approach is similar to the dovetailing technique used in woodworking, where interlocking, trapezoid-shaped pieces are glued together to create a secure joint.
Applying the same concept, researchers form metallic interlocks by using a specially designed tool and precise control of pressure and temperature to deform aluminum into a dovetail groove in the steel.
Simultaneously, the tool rubs along the bottom of the dovetail, forming an ultra-thin, iron-silicon layer that acts like glue.
The resulting joints are lighter and stronger than all-steel components, thereby increasing the efficiency and maneuverability of military vehicles.
This project leverages research funded by DOE's Office of Energy Efficiency and Renewable Energy.
For example, about five years ago, PNNL researchers worked with General Motors, Alcoa and TWB Company to develop the right combination of tool specifications and weld parameters for using friction stir welding to join different thicknesses of aluminum, while meeting auto industry demands for high-speed, mass production.
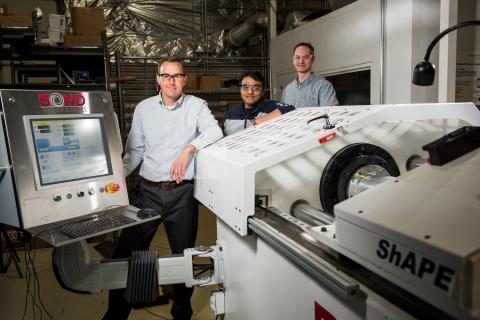
They produced a car door 62 percent lighter and 25 percent less costly than those produced using conventional manufacturing methods.
Today, TWB operates the only fully automated friction stir line in North America for tailored blanks — sheets of metal that are welded together, then cut and stamped into a final shape.
Creating new processes
In other work to develop less expensive, less energy-intensive metals manufacturing processes, PNNL invented a new method for producing wire, bar and tubular extrusions.
Using their patented Shear Assisted Processing and Extrusion system — or ShAPE — researchers create rods and tubes directly from aluminum alloy powder in a single step, which eliminates several of today's energy-hungry processes.
The ShAPE technology is so promising that the Washington state Department of Commerce awarded PNNL more than $900,000 to develop a next-generation ShAPE machine for researching advanced manufacturing of lightweight materials.
Applications being explored include fabricating magnesium tubes for automobile bumpers that absorb as much energy on impact as aluminum — while weighing 30 percent less — and developing graphite-infused copper wire that has higher conductivity than heavier, pure copper wire.
The PNNL researchers and industrial partners advancing solid phase processing may not be able to leap tall buildings in a single bound, but their intellect and innovation are taking metals manufacturing to new heights.
Related videos
Published: August 19, 2019